Editors’ Picks
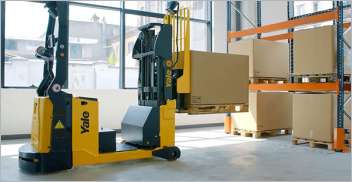
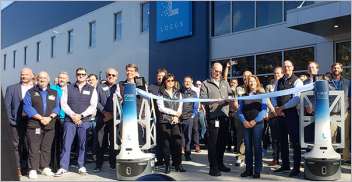
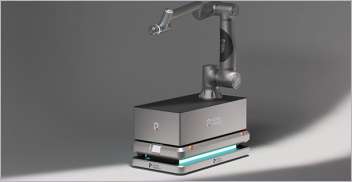
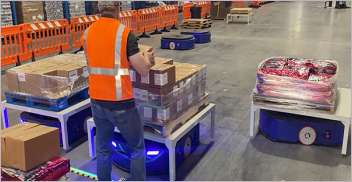
Found in Robotics News & Content, with a score of 24.87
…stainless steel 316L. “Most manufacturers today are investigating metal additive manufacturing, but they’re wary of the investment it requires. For many companies, using a sintering partner like Sapphire 3D is a very economical way to start,” Suess points out. “They can help you work through a variety of part design, printing and sintering issues to ensure that you can create the highest-quality metal parts.” “As you become more knowledgeable about designing for additive manufacturing with metal and its unique post-production requirements, you can always invest in your own sintering equipment later,” she points out. For more information about Sapphire 3D’s…
Found in Robotics News & Content, with a score of 24.82
In October, novices to additive manufacturing (AM) have the chance to take a special DfAM (design for additive manufacturing) course to understand how to design parts and assemblies to take advantage of 3D printing. Offered in partnership with America Makes, the event will be organized and led by Terry Wohlers, president of Wohlers Associates, and other instructors. DE is also a media partner of America Makes. The one-day DfAM course will take place in Youngstown, OH, on October 24. Wohlers Associates publishes the annual Wohlers Report that outlines the market trends and leading players in the AM industry. According to…
Found in Robotics News & Content, with a score of 24.80
…2024 as part of a grant from NASA for additive manufacturing research and education as it relates to space technology and applications. Work on this grant is a collaboration between the Navajo Technical University (NTU), who is acting as the lead on the project, with the Marshall Space Flight Center Advanced Manufacturing Center (MSFC), University of Alabama Huntsville (UAH), V&M Global Solutions and Optomec. The team will collaborate on additive manufacturing research around directed energy deposition (DED) of bi-metallic parts for NASA applications and build institutional capacity in STEM research and education. “We’re very excited to be working with this…
Found in Robotics News & Content, with a score of 24.59
Markforged Inc. yesterday announced that its manufacturing facility in Billerica, Mass., has met the rigorous quality management and quality assurance standards of ISO 9001:2015 to obtain certification from TUV Rhineland of North America. The additive manufacturing company said the certification will help streamline the supplier audit process. “Reliability is key for additive manufacturing. We're trying to help manufacturers meet traditional standards of quality, accuracy, strength, etc.,” Shai Terem, president and CEO of Markforged, told Robotics 24/7. “Without industry certification, that effort has been done application by application, one customer at a time.” Markforged said its Digital Forge is designed to…
Found in Robotics News & Content, with a score of 24.51
…management and automation of 3D printing workflows and large-scale additive manufacturing fleets. They include the new HP Universal Build Manager Powered by Dyndrite, which provides increased productivity and efficiency as well as automation to additive build management for leading 3D printing processes. The company also introduced new digital HP 3D Factory Services to provide customers with facilities and equipment analysis, staffing and training, and help implement production processes. In addition, HP announced the new HP Automatic Unpacking Station, developed in partnership with Rösler Group’s AM Solutions, to enable greater automation for post processing. “Automation, software, and data are key to…
Found in Robotics News & Content, with a score of 24.43
…conferences. Guha teaches a graduate lab course on metal additive manufacturing (AM) and design, which typically involves designing and producing parts in AM hardware. With everyone staying home and connecting via individual webcams from separate places, how can this class continue? Somehow, Guha and his students found a way. “Before the [Coronavirus] outbreak, the class was divided into smaller groups. We had round-robin schedules, with one group working on reverse-engineering, one on manipulation of the point-cloud [scan] data, one group on setting up the build plate, and one group on process simulation,” he recalled. “[Teaching on Zoom video conferencing] is…
Found in Robotics News & Content, with a score of 24.43
…conferences. Guha teaches a graduate lab course on metal additive manufacturing (AM) and design, which typically involves designing and producing parts in AM hardware. With everyone staying home and connecting via individual webcams from separate places, how can this class continue? Somehow, Guha and his students found a way. “Before the [Coronavirus] outbreak, the class was divided into smaller groups. We had round-robin schedules, with one group working on reverse-engineering, one on manipulation of the point-cloud [scan] data, one group on setting up the build plate, and one group on process simulation,” he recalled. “[Teaching on Zoom video conferencing] is…
Found in Robotics News & Content, with a score of 24.41
…the U.S. Navy sees positive results as it tests additive manufacturing for ship-building applications. Back in October, Naval Sea Systems Command announced it had approved a 3D-printed metal drain strainer for use on the aircraft carrier the Harry S. Truman. The prototype part was installed in the carrier’s steam system as part of a one-year trial. The strainer was originally a cast part that required a nine-month lead time to produce. The printed piece was created by Huntington Ingalls Industries and Newport News Shipbilding, which has been working on on its own maritime printing projects. The printed part took just…
Found in Robotics News & Content, with a score of 24.36
…traditional methods. According to Chris Botting, Materials, Processes and Additive Manufacturing Engineer at Marshall ADG, the ability to create accurate, repeatable and reliable 3D printed parts using aerospace-approved materials are key factors in achieving the performance requirements necessary for use within aircraft. “When manufacturing on complex engineering programs, we need a method that can create an accurate, complex, functional and lightweight duct efficiently with minimal tooling costs – this is where 3D printing fits perfectly,” says Chris Botting, Materials, Processes and Additive Manufacturing Engineer at Marshall ADG. “But we also need to ensure that the ducting work produced will be…
Found in Robotics News & Content, with a score of 24.35
…and certifying new materials are ongoing challenges in the additive manufacturing (AM) space. The same material may perform differently depending on which 3D printing process is used, and different applications may require unique material properties. In January, St. Petersburg, FL-based Jabil announced it was offering a new solution for creating and validating custom engineered materials for AM, and opened a new Materials Innovation Center in Minnesota to provide these 3D printing services in an end-to-end environment. “Materials is the elephant in the room,” says John Dulchinos, vice president of digital manufacturing at Jabil. “From a cost standpoint and availability standpoint,…
Found in Robotics News & Content, with a score of 24.23
Walk into any manufacturing company and you’ll discover the same set of challenges: Excel spreadsheets containing critical data are stored on the local hard drives of various team members’ systems. CAD/CAM packages whose only integration to the rest of the business is a file share on the corporate server. Enterprise resource planning (ERP) systems that offer visibility to every department in the company, yet are somehow blind to the activities of the factory floor. And product lifecycle management (PLM) software that does a great job of managing product data but keeps that valuable information to itself. Corralling the Chaos Many…
Found in Robotics News & Content, with a score of 24.23
The new FELIX Pro L and Pro XL additive manufacturing systems from FELIXprinters have been designed to perform at scale. These are manufacturing tools for every stage of the product development and manufacturing workflow. The FELIX Pro L and XL 3D printers have been developed with increased build volumes, up to 144 Litres (the Pro L can build parts up to 300x400x400 mm or 11.8x15.75x15.75-in., while the Pro XL has a build chamber of 600x400x600 mm or 23.62x15.75x23.62-in.). TBoth of these larger systems incorporate engineered print chambers, which incorporate an enclosed warm zone and a cold zone. The warm zone…