The Virtual Foundry has named Sapphire 3D as the first certified sintering partner for its plastic-infused metal filaments.
This Chicago-area firm has developed expertise in heat-treating “green” parts made from The Virtual Foundry’s open-architecture plastic-infused metal Filamets to produce high-purity finished metal parts.
“In addition to their proficiency with our materials, the team at Sapphire 3D also shares our vision, which is to make metal 3D printing attainable to everyone,” explains Tricia Suess, president of The Virtual Foundry.
“Successfully sintering a metal part involves some trial and error,” explains David Lawson, the founder of Sapphire 3D. ”The decisions you make during part design and printing affect the outcome of the sintering process.”
Lawson says his firm has maintained a database of every sintering cycle it has performed with The Virtual Foundry’s metal Filamets. That has enabled them to achieve 100% success with copper and bronze. They’re also approaching that level of proficiency with stainless steel 316L.
“Most manufacturers today are investigating metal additive manufacturing, but they’re wary of the investment it requires. For many companies, using a sintering partner like Sapphire 3D is a very economical way to start,” Suess points out. “They can help you work through a variety of part design, printing and sintering issues to ensure that you can create the highest-quality metal parts.”
“As you become more knowledgeable about designing for additive manufacturing with metal and its unique post-production requirements, you can always invest in your own sintering equipment later,” she points out.
For more information about Sapphire 3D’s services, click here.
Sources: Press materials received from the company and additional information gleaned from the company’s website.
About the Author
Press releases may be sent to them via [email protected]. Follow Robotics 24/7 on Facebook
Follow Robotics 24/7 on Linkedin
Article topics
Email Sign Up
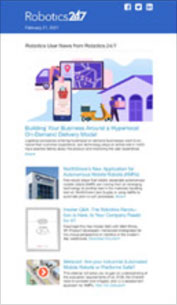