Editors’ Picks
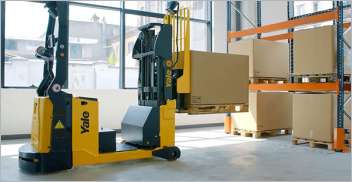
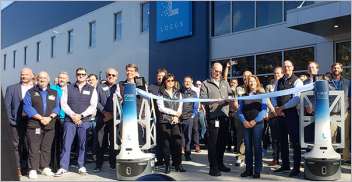
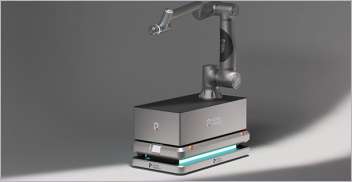
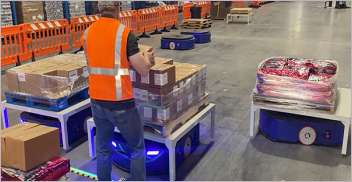
Found in Robotics News & Content, with a score of 6.60
…of degradation early is crucial. Now, Spot can perform ultrasonic inspections of rotating equipment using the Fluke SV600. This enables operators to detect early indicators of bearing failures before they cause a breakdown. Companies can capture more data without installing more inline sensors or requiring more contact sensors. Spot can serve as a four-in-one tool to uncover maintenance priorities: from air leaks, to equipment running hot, to out-of-range gauges - and now, potential bearing failures. Spot and digital twins with reality capture Industrial facilities are dynamic environments where tracking change, predicting issues and planning for what’s next are persistent challenges.…
Found in Robotics News & Content, with a score of 4.55
…from a bunch of laser measurements or from other ultrasonic measurements.” Slamcore’s proprietary AI stack takes in images and outputs object positions with labels. Nicholson said deep learning and generative AI are making it easier for computers to identify objects. “There's lots of companies out there who do labeling of images,” Nicholson said. “But if you don't know where that object is, you really limit the amount of value you can bring.” Because Slamcore’s software is foundationally a localization system, the computer knows where the cameras are within the facility space, and therefore can tell robots both what things are…
Found in Robotics News & Content, with a score of 7.27
…called Rapid Welding of Thermoplastic Composite Structures, robotic continuous ultrasonic welding was shown to increase the speed of induction. This project will build on the outputs from the prior project in order to scale it to production use. Fixtureless robotic assembly and manufacturing environment (FRAME) 2.0 Principal Investigator: Lockheed Martin Project Team: University of Southern California, Carnegie Mellon University, and Yaskawa Motoman Description: This project will build on the outputs from the ARM Institute-funded FRAME project. FRAME is a fixtureless high mix/low volume (HMLV) manufacturing cell with widespread applicability to both defense and commercial manufacturing challenges, highlighted by human-machine interaction…
Found in Robotics News & Content, with a score of 5.81
…underneath a tree canopy. Hamilton and Otteman also said ultrasonic sensors are embedded in the M.52 frames for development of the next generation of mowers. As Scythe’s robots autonomously mow, camera images are streamed for logging. Images are also collected from run-in, development, and test robots. “We have an employee who somedays literally takes out the robot to various properties, just so we can make sure that we're capturing a variety of images, obstacles, dogs, trees, and brush,” Hamilton said. The Scythe Robotics team recently held a launch party at their expanded production line in Longmont, CO. Source: Scythe Robotics…
Found in Robotics News & Content, with a score of 38.73
Sonair, a Norway-based ultrasonic sensor company, revealed its innovative developments in sensor technology designed to improve safety in industrial automation. The company, which has now exited stealth mode, also announced the upcoming launch of their first evaluation kit this summer, signaling a significant advancement in the field of robotic and machine autonomy. Confident navigation with a 3D ultrasonic sensor The Sonair 3D ultrasonic sensor allows autonomous mobile robots (AMRs) to detect distance and direction to all objects in a 180x180 field of view, up to a five-meter range. Combined with 2D images and AI, the outcome is confident navigation. The…
Found in Robotics News & Content, with a score of 10.13
…and scalability using existing carts Multiple sensors, including LiDAR, ultrasonic sensors, and depth cameras protect the safety of workers and objects being transported. LexxPluss’ open architecture approach allows for integration with existing systems. AMRs can be managed together with most field devices and the status of the entire site can be monitored in real time on a tablet. Lexx500 automated transfer robots with multi-sensor safety features can be deployed from just a single unit and increased to a multi-AMR fleet, providing scalability. The Lexx500 requires no fixed equipment and can automatically transfer loads up to 300 kilograms, about 660 pounds,…
Found in Robotics News & Content, with a score of 11.60
…conveyancing robots with multi-sensor safety that combines LiDAR sensors, ultrasonic sensors, and depth cameras to ensure they can operate safely and collaboratively with a human workforce. With a range of sensors, a multi sensor guidance system, and open architecture, the Lexx500 AMRs are designed to be highly scalable and interoperable - from a single robot to a fleet of units working together alongside existing automated systems and human workers. LexxPluss said the low upfront cost and ability to transport irregular cargo and large payloads of up to 500 kg is ideally suited to manufacturing and logistics businesses. LexxPluss was created…
Found in Robotics News & Content, with a score of 15.83
…from spot-welding, riveting, and dispensing to flow drilling and ultrasonic weld inspection. Each package is a ready-to-use, customer-proven combination of hardware, software, and services and will be implemented at Volvo Cars’ facilities in Torslanda, Sweden, and Daqing, China. Alongside the hardware and functional packages, ABB’s latest range of OmniCore robot controllers will help deliver energy savings of up to 20 percent at sites due to their highly efficient power electronics and use of regenerative braking within the robot. “The automotive industry’s historic transformation, driven by increasing consumer demand for electric vehicles and a desire to operate more sustainably, is creating…
Found in Robotics News & Content, with a score of 5.87
…as cameras, laser imaging, detection, and ranging (lidar), and ultrasonic time-of-flight (ToF) sensors, to detect objects and avoid collisions. However, because AGVs can only change their route or destination with manual intervention, they are generally limited to a particular task. Lack of flexibility and limited decision-making capabilities have led to more advanced robots. AMRs take the AGV concept a step further with the ability to navigate more complex environments. Unlike AGVs, AMRs are able to adapt to changes in their surroundings, flexibly navigating through the warehouse without colliding with other objects or causing damage. This is where simultaneous localization and…
Found in Robotics News & Content, with a score of 13.84
…and camera systems, the repair wagon includes integrated scanners, ultrasonic devices, and eddy-current measuring systems. “The use of robots ensures a consistent, well-documented quality of the work,” noted Weis. “In this way, we rule out damage that is not visible to the naked eye and make measurement and process data available to our customers digitally.” FANUC sees future for robotic maintenance Ralf Völlinger, general manager for robotics at FANUC Europe, said he is optimistic about the future use of robots for infrastructure maintenance. The Robel repair wagon. Source: FANUC “There is a great need for modernization in both the rail…
Found in Robotics News & Content, with a score of 9.48
…in the additive manufacturing industry, for which it provides ultrasonic sieving and reclaim machines. Piab said IB's portfolio will enable it to offer full powder-handling solutions, particularly in the food, pharmaceuticals, and chemical industries. IB's powder-handling expertise will join Piab's product portfolio. Source: Piab Group Piab said it expects to finalize the IB acquisition shortly, and it was also fully funded through internal sources. The global market for robotic grippers could experience a compound annual growth rate (CAGR) of 10.9%, expanding from $1.32 billion in 2022 to $3.03 billion by 2030, according to Next Move Strategy Consulting. The research firm…
Found in Robotics News & Content, with a score of 15.55
…destroyer. This expansion follows the approval of Gecko’s Rapid Ultrasonic Gridding (RUG) process by the Navy. Gecko said it will use its wall-climbing robots and AI-powered software platform to build digital models of the vessels to increase the speed of maintenance cycles and reduce the time Navy vessels spend in dry dock. “We built Gecko Robotics to solve the hardest physical problems facing the world’s most important organizations,” said Jake Loosararian, CEO and co-Founder of Gecko Robotics. “We are proud to have a mature technology that has been tested and approved by both Navy technical leaders and the sustainment officials…