Robotics may not be poised to take human jobs, but they have become a vital tool in a variety of industries. And they require a certain level of maintenance to keep running smoothly.
What are some of the most common problems that each commonly used type of industrial robot experiences? What should operators and technicians look for when performing regular maintenance on industrial robots?
Standard industrial robot maintenance
Regardless of the type of robot on the floor and the type of productivity bonus it provides, there are going to be some standard types of maintenance that are present in each situation. The only major difference is going to be in the recommended maintenance intervals, which can vary from manufacturer to manufacturer.
Daily inspections are essential, but beyond that, operational manuals may recommend maintenance after a certain amount of time or operational hours. Daily inspections and maintenance might include:
● Tightening any loose bolts
● Monitoring for leaks in hydraulic or pneumatic systems
● Listening for any out-of-place sounds
● Testing all moving parts for functionality
● Ensuring that operators (if applicable) are able to safely and efficiently control the device
The goal of these inspections is to make sure that everything is functioning correctly and that there are no issues that would require taking the equipment offline for more extensive and costly repairs.
Adding industrial robots to the average production line can result in up to a 40% increase in output, unless the robots are poorly maintained and fail when they’re needed most.
While most of these can be applied to nearly every type of robotics, there are more specific types of maintenance that apply to the different types of industrial robots.
Articulated robots
Articulated robots are the ones that most people picture when they think of industrial automation. They resemble human arms and are among the most common types of industrial robots in the world. Such robot arms are popular because they can rotate on a variety of axes and have multiple degrees of freedom, so they can reach nearly every inch of their workspace with ease.
These robotic arms can work incredibly fast and in a variety of positions, but that can also be their downfall. Articulated robots require complex kinematics to control their motion. A breakdown in one of these systems will take an entire robot offline.
A high component density means these robots are often more challenging to maintain and have many points prone to failure.
Inspection to ensure the articulated arm is moving correctly on every axis is essential. The speed with which they can complete their tasks also means it’s very easy for things to break down quickly.
Collaborative robot arms, which move more slowly and have more sensors for safety reasons, share many design features with articulated robots.
SCARA robots
In the robotics industry, the concept of compliance refers to a robot’s ability to move its joints. If someone pushes a compliant robot, it can move in any direction that it’s capable of.
Selective compliance assembly robot arms, known as SCARA, can move freely on the X and Y axes. However they don’t provide the same sort of free movement on the Z axis. They’re valuable for moving items from one point to another, or for single-plane assembly applications.
SCARA robots share many of the same issues as articulated robots, including a high number of parts that are prone to failure. Their limited configurations mean that it’s also easy to overload them, as most SCARA robots have a maximum capacity of 10 kg (22 lb.).
Providing extra inspections for these moving parts can help keep things running smoothly.
Delta robots
Delta robots use three arms attached to a single base, which earns them their “spider robot” moniker. These robots are used almost exclusively in low-weight, fast-paced pick-and-place operations such as those you’ll find in the pharmaceutical, electronics, and warehousing industries.
This high-speed operation means they can complete up to 200 picks per minute. They are a popular choice for high-speed operations that could cause repetitive stress injures, but the high-speed delicate work creates its own challenges as well.
Delta robots use a ball-and-socket construction to connect the arms to the main drive. The insulator rings that cushion those ball-and-socket connections need to be replaced twice a year or so to ensure they are providing the correct level of insulation. One failure can take an entire delta robot offline while it waits for repairs.
Looking forward
This is by no means an exhaustive list. There’s a variety of robot types that can carry out all sorts of broad or specialized tasks in multiple industries. Each type of robot has its own tasks and its own maintenance schedule to guarantee that it continues to operate successfully regardless of how long it stays online between tuneups.
Sticking to the manufacturer-recommended maintenance schedule is only part of the equation. It’s also necessary to understand the individual idiosyncrasies of each type of robot, and how to manage them to prevent costly failures.

About the author
Zachary Amos is a writer at ReHack, which explores the latest tech innovations and trends. He covers topics including artificial intelligence, machine learning, and other technologies.
Article topics
Email Sign Up
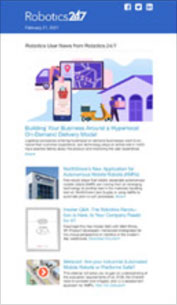
