Warehouse control system (WCS) solutions are evolving, both upward into the order-handling domain of warehouse management system (WMS) software, and outward to include more types of wearables, robotics and sensors seeing use in distribution centers.
Originally, WCS grew out of the need to coordinate the material flow between major types of automated systems such as conveyors, sorters and pick-to-light systems. Now a new breed of WCS solutions - dubbed warehouse execution systems (WES) - have entered the market, taking on some higher-level fulfillment challenges.
So, is WES just the latest supply chain execution software jargon? Well, it may be the new acronym on the block, but if your DC is trying to adjust to the high-velocity world of omni-channel, it may be worth knowing more about WES and how it differs from the traditional WMS or WCS layers on either side of it.
Do you need to break from releasing orders in large, batch-like waves because of the tight cycle times and item picking needed for omni-channel fulfillment? That’s one function providers of WES or next generation WCS suites say they can meet. According to suppliers, easing such pain points takes a combination of the real-time view into equipment and labor provided by WCS, combined with knowledge of orders and inventory, as well modules with optimization logic.
Related Article: WCS Drives Higher Profitability through Synchronized Pick, Pack & Ship Omni-Channel Fulfillment
With some providers, modular WCS/warehouse execution functions may be paired with WMS-level modules in a flexible way to scale to the needs of the specific user company. (Diagram courtesy of Intelligrated)
A key goal with WES, according to Steve Banker, a senior director and analyst with ARC Advisory Group, is to have a system that has a near real-time view of automation, labor status and other inputs, and can apply that knowledge to a more dynamic way of optimizing DC operations. “The idea would be to optimize based on what is happening with order priorities as well as synchronizing all the different materials handling systems,” Banker says. “There has to be some sort of interaction back and forth between the WMS and WCS to achieve this type of global optimization, and right now, that’s pretty much what is lacking.”
The new breed of WCS/WES solutions have the potential for achieving this level of optimization because they have visibility into multiple automated systems and also are easier to configure than earlier generation WCS, says Banker. However, he warns, optimizing all the automated assets in a DC and coordinating them against order priorities and labor resources isn’t an easy proposition, even if generally the tools for configuring WCS are getting better.
Other observers also see potential for WES. John Sidell, principal and co-founder with New Course, says the new WES solutions are better equipped to optimize the handling of orders in highly automated, omni-channel fulfillment facilities. “What’s happened is that the warehouse control vendors have built out more functionality to handle all the marshaling and the waving and sequencing of work that needs to pass through the various automated materials handling systems,” says Sidell. “All that marshaling of resources and work sequencing goes beyond the original ‘traffic cop’ role WCS played between the mechanization.”
Central Role of WES
The first thing to understand about WES, suppliers say, is that it doesn’t fully replace WMS, but augments it when it comes to things like “wave-less” order picking.
The rise of omni-channel means that more DCs can no longer batch orders into large waves that must be completely processed before tackling more orders. “Now fulfillment needs to be more real-time and transaction based,” says Gene Billings, director of software products for Intelligrated, which acquired Knighted Software in late 2012.
Intelligrated’s WCSPlus solution, says Billings, is able to handle the new style of fulfillment including wave-less picking. In effect, he says, the WCS suite is generating “continuous waves” that steadily drop picks into each operator’s pool of work. “Instead of having a batch of work these operators are working with, they now have what is basically a fluid and continuous body of work,” he says.
To accomplish this style of dynamic fulfillment, it takes more than a traditional WCS, but also modular applications with knowledge of inventory and order information, adds Billings.
Miguel Pinilla, vice president of Global Logistics Solutions for Dematic, agrees WES solutions are modular solutions with a WCS core. He also points out that where traditional WCS was focused on controlling automated materials handling equipment, the new breed of solutions takes in higher-level challenges such as dynamic handling of e-commerce orders and lean/pull fulfillment. “It’s moving from equipment control to a more integral platform for execution,” says Pinilla.
Advanced WCS solutions integrate with multiple subsystems and span multiple functions, allowing subsystems to operate in concert while accelerating overall material flow. (Diagram courtesy of Fortna.)
The WCS foundation of WES gives these suites the ability to pace fulfillment work based on real-time inputs from the floor, says Pinilla, rather than sequentially working through large waves. “The thought leaders are looking at lean/pull in distribution,” he says. “Within this type of pull environment, your decision making comes down the shop floor, and therefore the WCS needs to support that. It becomes a different way of optimizing, which is more dynamic and real time.”
Art Eldred, client executive for systems engineering with Vargo Companies, which offers a WES solution, also sees the ability of WES to support lean DC operations as a key development. To manage lean dynamically, WES solutions benefit from WCS-like visibility into machine status, but WES can also track labor status through ties to terminals and other systems used by operators.
In effect, says Eldred, because a WES knows the pace at which operators are completing tasks that feed automated systems, WES can orchestrate the overall flow of work. “For us, the induction of work into one area is triggered by the completion of work at another area,” he says. “WES is able to synchronize and sequence these activities.”
WCS definitely has evolved beyond its role as a machine control layer, says Nikko Pianetto, group vice president of integrated technology solutions for Fortna, a distribution professional services firm offering modular WCS solutions that incorporate algorithms to dynamically adjust operations. “The environments are becoming harder and much more complex,” Pianetto says. “You can’t just continue to throw conveyor at the problem. You need to be thinking about optimization, and algorithms, and real-time sortation.”
Optimization is enabled by the ability of WCS to know the real-time status of all the automation in a DC such as conveyors, carousels or print-and-apply stations, and dynamically make decisions about where to route work based on resource availability, throughput and service level factors. This is more than conventional flow control, adds Pianetto, because it can juggle order priorities, service levels and the availability of labor. “That’s the Holy Grail - this type of wave-less, real-time control of the flow of work within the building, while at the same time meeting your service-level demands,” he says.
Configuring Modules
Providers including Fortna offer modules that “snap onto” a WCS to handle particular types of optimization says Pianetto. Configuring the right solution takes some assessment of a DC’s equipment and processes, he adds.
WES solutions are modular, agrees Tom Rentschler, vice president for sales and marketing for Forte, meaning they can be used to augment WMS in some areas, but not necessarily all areas, so that the user company might not need the entire WES suite.
“What we hear over and over is that clients want to deploy only the functionality that they need,” Rentschler says. “We address this with a modular, configure-to-order approach with our software, which isn’t new in software markets, but in this field [warehouse operations] is a much newer approach.”
For example, notes Rentschler, order-handling logic from Forte’s Warehouse Director module can be combined with automation visibility and control from its Automation Director module to dynamically reroute work to needed lanes. For instance, if a DC had three pack lanes and one audit lane, but the audit lane became choked with work, Forte’s solution could automatically change one of the pack lanes into an audit lane, complete with the ability for the operator to look up missing inventory on an order and request picks to complete the order, says Rentschler.
This dynamic reassignment of lanes would have been impossible in past eras with simpler, machine-focused WCS, says Rentschler. “This all happens on the fly based on full line conditions,” he says. “Years ago that would have been a situation where you can only have one station, or someone would have had to go in and change the system.”
New Course’s Sidell also sees WES as being modular, but typically requiring assessment and services to properly set up. “The operations engineering services bring you a better understanding of the optimal flow of work, as well as insight into the high-end throughput you are capable of achieving,” says Sidell.
A modular WES suite means you should be able to combine it with existing WMS functions that are working well for your operation, according to Tim Brown, digital marketing coordinator for Reddwerks. With Reddwerks’ WES, he adds, users often continue to use WMS for functions such as receiving, but use the WES to optimize picking or sortation.
Brown also agrees with the notion WES deployments benefit from operations engineering studies to identify what needs improvement. “A lot of what WES is about is optimizing what you already have,” says Brown. “We don’t want to be confused with a rip-and-replace approach. It’s more about filling the functional voids you have.”
Future Trends
The newer WCS solutions also are evolving to manage newer types of automation becoming part of the Internet of Things, says ARC’s Banker. These newer nodes might include materials handling robots, driverless forklifts, or even visual signals captured by a digital imaging system or camera.
For instance, a worker at a dock might use a simple hand signal - captured by digital image - to trigger a conveyor feeding goods to the dock to pause or slow down, says Banker. While the raw sensor and imaging technology exists, software suppliers have to configure the logic and rules to manage such inputs. “The first thing I think about with this new breed of WCS is that they will need to evolve to accommodate a larger range of systems,” says Banker.
WES solutions able to tie into new technology, like sensors and wearables, will be able to analyze real-time trends to adjust operations, says Pinilla. “I like to call it contextual computing in the sense that through the platform’s visibility into devices and systems, and we know the context in which they need to be used,” he says.
Pianetto also sees the new breed of WCS as tying into wearables such as Android watches, as well as wearable glass devices. The Android platform offers a built-in voice recognition engine, which Pianetto believes will lower the barrier of entry for creating voice-picking apps.
With advanced WCS integrating with wearables, adds Pianetto, suppliers are in a strong position to offer solutions that leverage real-time insight into worker activity. “Imagine now not only being able to use WCS for visibility into all your conveyors and other automated systems, but you also are able to see and manage the location and activities of people,” he says. “So not only do you know where your parcels are, but you are able to address the second part of the equation - which is where your people are, and better yet, where they should be.”
This infusion of new capabilities into the WCS market carries the side benefit of attracting talented developers, says Pianetto. Trends like omni-channel and technologies such as Android watches have combined to make WCS more attractive to top tier talent, says Pianetto. “You now have young, smart developers being attracted to the market, and that in turn is going to enable us to produce better solutions,” he says.
Companies mentioned in this article:
Related Article: Warehouse Management Systems & Warehouse Control Systems in the Age of the Internet of Things
Article topics
Email Sign Up
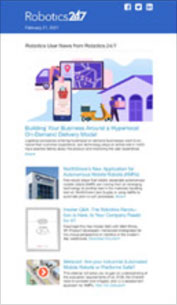
