The market for warehouse automation is exploding because companies with fulfillment operations can’t find enough workers to stick with largely manual processes in the face of rapidly growing e-commerce volumes. At least that's what conventional wisdom posits.
That idea has companies looking at autonomous mobile robots (AMRs) and other types of warehouse automation, such as robotic, high-density goods-to-person (GTP) systems, as well as more traditional automation, to do more with less for crucial processes.
All of this thinking is true, but it glosses over a fundamental challenge operations face as they implement more automation: getting multiple systems to work together in unison and releasing work to these assets in a way that both achieves high utilization and gets orders out the door on time.
This ability to coordinate multiple systems and resources—what’s come to be known as orchestration—is where software comes in. And it’s a core reason why the materials handling automation market is becoming more software focused.
Software takes center stage
“Historically, the main value proposition was more on the hardware,” said Rueben Scriven, a senior analyst with research firm Interact Analysis, which tracks the automation market. “If a company wanted a good automation solution, they would turn to a company with reputable, innovative hardware. But over time, these systems have gotten commoditized, where by and large the automated equipment you can get from various vendors is going to be similar.”
For vendors, said Scriven, hardware commoditization creates a need to differentiate their solutions and create lasting ties to customers. While maintenance and services of automated equipment has been one way to do that, increasingly, it’s software that sets vendors apart, and helps operations achieve a better flow of goods through more highly automated distribution centers.
“It’s partly about vendors needing to differentiate and create lock-in; and viewed more optimistically, software can add a lot of value by helping operations achieve a better flow of goods,” said Scriven.
Of course, anyone who uses a mobile phone, or a robot vacuum, knows that good hardware needs good software to be effective. That dual nature has long existed in the warehouse automation market as well, with warehouse control system (WCS) software having been applied for decades to configure and monitor automation.
But market observers say that what is happening now with software is less about governing the speeds and feeds of each zone of automation and more about orchestration of the entire DC as a system, as well as knowing when and how to adjust specific resources to accommodate peaks.
Software is an important component of robotics
With robotics solutions, software plays at multiple levels. AMR vendors, for example, don’t just make robots, they also offer fleet manager software, performance monitoring and analytics.
Some vendors are also expanding into broader orchestration with functions like pack-out lines. Of course, AI is in many robotics solutions, so the system can continuously learn over time when it comes to issues like path optimization, or how to best grasp and manipulate items.
In the piece picking robotics market, solution providers typically partner with leading vendors of industrial robots with articulating arms, rather build their own robots, and the same typically holds true for sensors. The value and intellectual property of piece-picking robotics vendors is typically centered on AI software and associated vision technology that permits a robot to perceive and understand what is presented to it.
Clinton Smith, chief technology officer at RIOS, a provider of AI-powered robotic piece picking solutions, explained that while RIOS designs its own end effectors or grippers, AI-based software gives the hardware the needed intelligence to know how to grasp and manipulate items.
In practice, robotics piece-picking solutions call for a combination of software, hardware and engineering capabilities from the provider.
Smith:
“I would say that hardware and software are equally important—one can’t function without the other.”
Cloud technologies enable more complex robotic tasks
RIOS’s AI software uses artificial neural network technology that mimics how brains function in determining how to grasp and handle items, Smith explained.
“Such techniques are required given the complexity and challenge of piece-picking use cases, which can include high SKU variation, changing environmental and visual conditions, difficult visual properties involved with certain SKUs, fast cycle times, and precision and accuracy requirements.”
In addition, RIOS offers hybrid-cloud software for real-time monitoring of cell performance, such as count statistics, while offering application programming interfaces (APIs) for integration to WMS. RIOS partners with FANUC for articulating robotic arms, though it has developed its own end effectors for different classes of items.
Smith adds:
“End-effector hardware is extremely important because, in these new and challenging use cases, where you may have changing SKUs, jumbled items, and irregular geometries, it needs to replicate the capabilities of the human hand.”
“As a result, practically speaking, an end effector usually needs to be designed for a particular class of use cases, such as by size, geometry, weight, or whether an item is hard or soft. This requires a sufficiently sophisticated software stack that can adapt not only to these different use cases, but to the appropriate manipulation with a given end effector.”
Take a step back from visual “wow factor” of the latest in warehouse automation and robotics, and it is really software at the WES and analytics levels that will allow users to flex multiple zones of automation to current demand patterns and rapidly changing resource availability, vendors agree.
Most WCS software can’t optimize the overall DC like WES can, explained Laura Bickle, senior offering manager for WES at Honeywell Intelligrated, a major provider of warehouse automation and related software.
“The WCS system is focused on product throughput, but not optimizing the process end to end like a WES can,” Bickle said. “By utilizing artificial intelligence and machine learning, WES enables the customer to make real-time, last-minute decisions based on system status to avoid congestion and maximize throughput.”
WES essential for orchestration
Over the years, vendors with WCS have enhanced their software with more capabilities around functions like order release logic and load balancing to come up with what is known as a warehouse execution system (WES).
Today, said Howard Turner, director of supply chain systems at consulting firm St. Onge, WES software, offered by multiple types of vendors including automation vendors, is key to orchestrating multiple automated systems.
“When implemented properly, WES does carry out this vital orchestration role where the software acts much like an orchestra conductor, getting multiple assets to work as one, so you can achieve the throughput and customer service you are after,” Turner said.
WES is offered by various types of vendors, including major warehouse automation OEMs, systems integrators, and some warehouse management system (WMS) providers.
In addition, some vendors may offer related predictive analytics tools, and robotics providers also stress the software capabilities of their systems when it comes to monitoring performance and order fulfillment progress. That makes examination of software more important when putting in place effective warehouse automation.
“When a company acquires some automation today, they are not just getting equipment,” Turner said. “They are getting the software elements and all that comes with that in terms of orchestration and order release, and being able to look at throughput and picking efficiencies. You can’t overlook the importance of the software, which is essentially the brains of the operation.”
What’s in WES
WES is offered by a variety of vendors, including major automation vendors who also make hardware, systems integrators who’ve evolved full-fledged WES from WCS, and a few of the major providers of WMS, which typically remains a key system for warehouse transactions and inventory management, even when WES is deployed.
But what does WES really do, and why are these functions important to deriving maximum value from automation?
Robotic piece-picking systems are driven by artificial intelligence that gives the robotic arm the smarts to know how to best grasp different items.
Coordination of multiple automated systems is WES’s overall purpose. “Because of all the fulfillment challenges posed by e-commerce and omnichannel trends, we’re pulling in more and more technologies to create efficiencies, and it’s really the responsibility of the software to tie all those together efficiently,” said Mary Elliott, chief product and technology officer at Fortna, an automation supplier that offers WES. “The ability to orchestrate those varied systems in an intelligent, optimized way is what the software provides.”
One way WES coordinates the allocation of work across automated systems is with smart order release, which instead of the big “waves” of work, releases work to systems in smaller chunks with the current status and capacity of multiple zones of automation in mind.
This order release function can be thought of as the starting point for orchestration, with WES’s ties to lower-level control systems alerting of any unexpected events, or bottlenecks, that might be developing, with some software offering “load balancing” features to help adjust to the present reality on the floor.
Warehouse automation benefits
“The other main benefit from WES is real-time visibility into what’s happening with your systems and processes,” said Elliott. “It can be really hard for someone in operations to look at different systems and try to understand what is happening and react appropriately. Again, that is where the intelligence of WES solutions comes in, and why the software is so important, because you can’t get that understanding from the equipment alone. You need a layer of software intelligence that sits over that equipment and monitors behavior.”
Another way WES helps get more from automated equipment, in addition to the higher-level coordination role, is to provide logic and rules for maximizing throughput of GTP and automated storage and retrieval systems (ASRS).
This happens on an ongoing basis as work is assigned to a system, while the software’s visibility features help managers decide when it’s time to scale up the system’s performance by doing things like opening more picker workstations, or adding robots or carriers to a system, pointed out Markus Schmidt, president of Swisslog Logistics Automation Americas, a provider of warehouse automation and WES. Being able to maximize the throughput within a zone of automation is largely a matter of software, he explained.
“Software is critical when it comes to getting the most utilization out of an ASRS solution, and knowing when to scale up and down,” said Schmidt. “For instance, some software might only require a system to bring the nearest item in an order to the pick station.
“Excellent software will take into consideration multiple variables including where the item is located, if the bin or shelf is full or empty, or assign priority for expiry dates among many other requirements. This allows the user to get the most utilization and throughput out of the system,” Schmidt added.
Visualizing the operation
Since many WES solutions grew out of WCS, they have close ties to the control systems that directly govern the automation on the floor. Add analytics, and WES shapes up as an overarching dashboard for DC management.
“Correctly tailored to the solution, [WES] can provide tangible benefits to operators and maintenance personnel by showing robotic battery utilization and capacity, path utilization using heat mapping to identify choke points, ASRS capacity utilization, handling device cycle times, and other relevant machine performance metrics that can drive operational decisions related to preventative maintenance schedules and mechanical intervention,” said Schmidt.
“Unification of WES and WMS simplifies business intelligence analysis and can speed decision-making in the front office as well with inventory management, slotting and operational staffing,” Schmidt added.
Solution providers with WES and predictive maintenance software are in an ideal position to offer dashboards to managers who don’t want to scour separate user interfaces and performance monitoring visualizations to see what is going on with an operation, said Michael Conrath, chief product and technical officer for Kuecker Pulse Integration (KPI). It provides warehouse automation and WES software.
“What we want to do is figure out how we can take data from multiple disparate sources and consume and view it in a unified manner that’s useful to our customers,” Conrath said. “We may never have a generic, one-size-fits-all dashboard because of the different systems used by customers, but there is value in a more unified approach to visualizing operational trends.”
Warehouse execution software manages order release, offers visibility into throughput, and provides a user interface for GTP workstations.
To make that work, Conrath said, solution providers need to have expertise in using applications programming interfaces (API) to automation and robotics solutions from various vendors, rather than just offering the dashboard piece.
Besides WES functionality and dashboarding, Conrath sees modeling and simulation of warehouse processes and material flows, and predictive maintenance software, as other key aspects of what solution providers need to bring to the table to make the design of warehouse automation systems, and their operation, more effective.
Asset analytics
A natural area of focus for materials handling automation vendors is to offer software for predictive analytics over equipment uptime. This may be separate from a WES or WCS solution, but it all ties back to the notion that an automation solution’s value increasingly comes from software.
Sebastian Titze, manager of digital transformation in North America at Beumer Group, a provider of automated materials handling solutions, says software and other digital solutions are an important focus for Beumer, since automation systems generate an enormous amount of data that can be analyzed for productivity gains.
Beumer is well known for its sorters, but as Titze explains, it also offers machine control, WCS and digital products such as its BG Insight software that offers data analytics with visualizations and machine learning to inspect root causes of inefficiencies and alarms.
“Optimized systems will rely more and more on the data, especially when more automated systems become increasingly complex to operate,” said Titze.
Beumer’s systems generally can integrate with any WES or WCS, though its own WCS can be configured and used to optimize the sortation equipment and coordinate material flow with other systems such as inbound doors, loading and unloading equipment, conveyors, or other materials handling systems.
“This [orchestration role] is absolutely critical, and every machine manufacturer wants as much information about the surrounding processes as possible, so they can optimize the outcome of their specific process within the facility,” Titze said.
About the Author
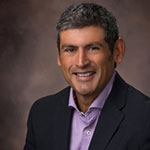
Follow Robotics 24/7 on Linkedin
About the Author
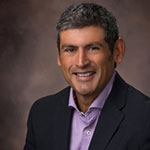
Follow Robotics 24/7 on Linkedin
Article topics
Email Sign Up
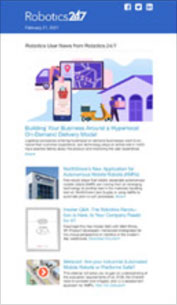
