Strong communication networks are essential for the success of any organization, especially manufacturing facilities with robots.
Robots and other automated systems need to send information to software, and robots require instructions from software to perform their tasks. Communication networks enable the smooth flow of information between machines and software residing on a central server.
Here are some best practices to keep in mind while building and maintaining them.
Network segmentation
You can have a single network that connects to all the automated machines in your facility, but this introduces a significant risk to production. When some component of the network fails, the complete production process will be impacted. This is a problem when different parts of your facility can work independently.
The better solution is to implement network segmentation where different independent parts of your facility have separate networks. This eliminates the risk of shutting down the complete facility when there is a fault in just one area of the network. Network segmentation also helps in reducing network congestion enabling smoother communication.
Equipment choice
Equipment plays an important role in the network's performance. Choose high-quality equipment that fulfills the requirements of your manufacturing plant.
Access control
Access control determines who can access the network to transfer and access information in the network. All the employees and machines do not need access to all the network resources.
Role-based access control helps to limit access to resources to only the personnel that need the information. Access control limitations also can apply to robots and other automated equipment connected to the network.
Use the “Principle of Least Privilege” to determine the access control levels. According to the principle, you only provide access to the minimum set of resources required for the personnel to carry out their duties. They should not have access to any more resources than that.
Installation
When network installations are exposed there is a chance of tampering with the devices intentionally or by accident. It is prudent to keep network installations in locked enclosures. Ethernet and other cables should be run through concealed conduits.
Network devices such as Wi-Fi installations should be inside locked enclosures. Additionally, power supply must be provided near the network components where required.
The central room that houses the servers, switches, and hubs need to be air-conditioned. Network devices generate heat during their operations.
Climate-controlled rooms help to maintain the temperature and performance of the devices. Such rooms also minimize the chance of dust accumulation. Dust accumulation has the potential to hamper the performance of the devices.
Monitoring
Regular monitoring of network activity has to be done to keep an eye on the health of the network. You can make use of different software available for the purpose. Such tools help to identify any anomalous activities in the network that could be potentially harmful.
You need to investigate the root cause of any such anomalies. Because of the large volume of transactions in an automated manufacturing facility, it is difficult to manually monitor the network traffic. You should invest in artificial intelligence tools in such cases.
Security
Cybersecurity is a concern for modern automated facilities. Hackers have the ability to disrupt production operations without access to the physical location of the production. You need to protect your digital infrastructure with efficient cybersecurity tools to prevent the loss of data.
Firewalls and identity providers are essential tools in cyber defense. You can also opt for private networks to limit the threat of cyber attacks. You should conduct regular penetration testing to identify any loopholes in your cybersecurity strategy.
Maintenance
Regular maintenance of the network and network components is essential in conserving the health of the network. Regular cleaning prevents dust accumulation.
Timely replacement of network components maintains the performance of the network. In addition to that, regular software and security updates have to be installed to keep the network up-to-date.
Strong network, better facilities
A communication network is like the central nervous system in the human body. It should be present in every nook and corner. It should also have the capability to deliver the right information at the right time.
When this communication network experiences a failure or a breakdown, the information transfer between the servers and machines comes to a halt.
Without instructions from the software, machines cannot continue with their tasks. The complete production of your facility has to be halted in such a scenario. Network congestion can also cause downtime for your production facility.
Downtime in production impacts the efficiency of your organization. It has downstream effects like delays in delivering customer orders, losing customer loyalty, etc.
These downstream effects impact the profitability of your business. A reliable communication network is essential for the long-term success and profitability of manufacturing businesses that use robotics for process automation.
By investing in reliable hardware and software, implementing security measures, and using the latest technologies, you can create a communication network that will drive your facility to higher efficiency and profitability.
About the author
Patrick Chown is the owner and president of the network installation company, The Network Installers. The Network Installers specializes in network cabling installation, structured cabling, voice and data, audio/visual, commercial Wi-Fi, and fiber optic installation for industrial and commercial facilities.
Article topics
Email Sign Up
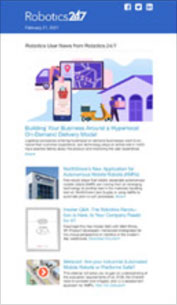
