The familiar technology stack of warehouse management systems (WMS) to manage transactions and inventory at the distribution center level and then hand order requirements down to the automation layer is not as simple as it used to be. With the complexities of e-commerce fulfillment, the need to orchestrate and optimize operations is driving the need for advanced execution software in the middle of the stack and for more optimization tools.
In short, the DC tech stack has changed. It’s no longer just WMS on top, warehouse control system (WCS) software in the middle, and automated materials handling systems at the floor level. The stack has expanded, and while not every DC needs the same foundation, failure to grasp evolving areas could end up stacking the deck against omni-channel success. What’s more, while automation hardware—including robotic goods-to-person systems, pick-to-light systems and high-end sortation—play a role in the tech stack for e-commerce, even automation providers say the stack is software driven.
“The new types of automation hardware are extremely important, but I think it’s a matter of hardware and software as a combined solution that give users the advantages and throughput they are after, especially when you have Amazon pushing the same-day delivery model, and everyone is chasing and trying to achieve that same panacea,” says Michael Howes, vice president of software and controls for Swisslog Warehouse and Distribution Solutions (WDS) Americas, which offers automated materials handling as well as software solutions.
E-commerce means that DCs have a greater volume of small orders that make it more complex to orchestrate systems, not only within the four walls of the DC, but with order fulfillment and transportation management decisions. “Everyone is being pushed to ship smaller and faster,” says Joe Vernon, senior manager of North America supply chain technologies for the consulting firm Capgemini. “The demand/fulfill cycle has been cut from days to hours, and freight costs are more often absorbed now, rather than passed along to a customer.”
Vernon sees distributed order management (DOM) solutions, as well as new types of optimization software that can synchronize pick sequencing, staging and loading, as gaining in importance.
Perhaps the biggest shift in the DC tech stack for e-commerce has been the emergence of warehouse execution system (WES) software, an evolution of WCS. WES brings in richer functionality around order releasing and wave management, resource optimization and analytics, in addition to WCS solutions’ more traditional role of coordinating automation and material flow.
The role of WES
WES solutions provide visibility and management capabilities around order requirements, inventory information, and equipment and labor resources, observes Mike Dunn, group vice president with Fortna, a distribution consulting and engineering firm. “The interesting technology questions inside the DC are: ‘What systems should I own to have visibility into those three components,’ and then, ‘What software can I use to really optimize my processes?’” Dunn says.
WES tends to be at the center of things in today’s tech stack, says Dunn, because with its WCS roots, it has real-time knowledge of equipment processes; it knows labor availability details; and it can take the order requirements from the enterprise level to manage the order pool and decide what should be processed next by the DC’s resources. While some WMS systems are getting better at grouping orders into smaller waves for processing, most WMS systems tend to batch work into large static waves, says Dunn, whereas WES excels at releasing chunks of work to the floor in the right size and sequence to satisfy orders while squeezing maximum efficiency from resources.
“When we think about how to really optimize inside of a warehouse, it’s about creating chunks of work that are large enough to drive productivity, but small enough to react to and satisfy customer demands,” says Dunn. “And the optimal size for work may change every hour. In the morning, you may be able to process a larger chunk of work efficiently while still meeting demand, but later in the day, you may need to use much smaller chunks of work, which are suboptimal from a productivity standpoint, but are necessary to meet demand.”
While WES has gained in importance, it can’t do everything, says Dunn. Omni-channel companies have often turned to DOM to manage where orders should be fulfilled from, and at many companies, a WMS handles overall inventory, says Dunn. Down at the automation level, he adds, DCs often have strong interest in technology such as goods-to-person systems or pick-to-light systems that minimize or simplify the labor requirements for order picking. But Dunn sees WES as the best solution for the order releasing and resource management decisions that need to be made around order priorities.
“We believe the best solve for many of these business problems is going to be a combination of WCS and WMS capabilities,” Dunn says. “Finding a way to have those two types of systems work well together to release and process work is going to be the optimal solution.”
No one wants chaotic, inefficient peaks and lulls in the pace of work, so WES providers often focus on enabling a demand-driven, level pull of work through a DC and its various points of automation. So it’s not just software bells and whistles to consider with WES, but the approach used to achieve flow, explains Walter High, vice president of marketing with Invata Intralogistics, a WES provider and consulting firm.
“In building out system infrastructure, we take a whole system approach to optimizing process flows that embraces lean engineering techniques in the physical layout of our systems, the intelligence of our software, and the application of advanced technology that maximizes the efficiency of human interaction, while eliminating toilsome labor requirements,” says High. “In doing so, we eliminate as much manual and planned push-based processing as possible, and replace it with pull-based, self-regulating and self-maintaining systems.”
Projects around orchestrating flow also benefit from a data science approach in which data analysis, modeling and simulation are used to determine how to best configure the DC’s technology stack, adds High. “Using data science, we are able to look an existing operation and test options to determine their affect on that operation,” he says. “So while the technology stack can dramatically affect a company’s strategic advantages in the market, changing it out when productivity languishes is not always the right answer. The answer is derived through understanding a customer’s data, business requirements and growth expectations, and scientifically modeling that information in a way that delivers direction.”
Broader needs
While some omni-channel retailers are leveraging WES solutions, there remains a big chunk of the market with simpler tech stack needs, observes John Sidell, principal with supply chain consulting firm New Course. For many consumer goods manufacturers or other companies that aren’t at the bleeding edge of omni-channel, but do have growing e-commerce needs and more pressure from small rush orders, the key concern is identifying when e-commerce volumes force a change to the tech stack, explains Sidell.
“There are consumer goods companies and others who are asking, ‘where is my tipping point—in terms of e-commerce volume and complexity—when I either bring in a third-party logistics partner or create a new operation dedicated to e-commerce?’” says Sidell. “Where they are with that tipping point greatly influences what they need in a technology stack.”
For some companies who have relatively modest e-commerce pressures, the tech stack will tend to be more streamlined compared to what an omni-channel retailer would put in place at a DC, says Sidell. A WMS with a more agile approach to wave management, some zone picking, or perhaps a voice-picking solution combined with WMS might be key pieces of a tech stack for many organizations. “For some companies, the current tech stack can be adapted to support new methods of order picking,” says Sidell. “If they can tap additional functionality from their WMS vendor, turn that on and train the users, that may meet their needs. That said, as your online business grows, the need for more automation grows with it.”
The growth of e-commerce also has elevated the importance of DOM and the inventory visibility DOM relies on, says Sidell. Well-implemented, accurate WMS systems support this visibility, says Sidell, as do accurate store-level systems. “One of the most crucial elements with omni-channel is real-time inventory visibility across your supply chain network,” says Sidell. “To have effective DOM and fill orders with confidence in the promised service level, this inventory visibility is a must.”
The solution stack for DCs increasingly needs to look beyond the four walls of a single site to optimally process and ship orders, says Capgemini’s Vernon. Some sites might have multiple buildings within a “campus,” notes Vernon, which adds to the complexities of the DC-level inventory moves, processing and staging. The whole process constitutes a “multi-tiered, multi-constraint optimization puzzle,” says Vernon, to get the right goods to the right dock doors at the optimal time for pickup by carriers.
To solve this challenge, says Vernon, DCs are adopting solutions for pick sequencing, staging and loading optimization with integration to robotics and automation. Vendors in the space such as warehouse optimization can help DCs schedule complex activities in a synchronous way to achieve flow and better use labor, according to Vernon.
Capgemini is involved with pick sequencing, staging and loading optimization by offering data science services that assess actual performance in shipping orders against the model in the software, so that the model can be improved for further efficiencies.
Providers of robotic goods-to-person systems and other warehouse automation systems also employ data science to refine the effectiveness of their solutions, says Vernon. The data science for pick sequencing and loading will build on data science from the automated equipment providers, rather than replicate it, he adds.
Expect to see more data science from solution providers and consultants, says Vernon, since some DCs are becoming highly automated and generate a constant data stream that can be analyzed to refine optimization engines. “The future is to make this whole ecosystem smart, optimized and predictive,” says Vernon.
On the edge
Another aspect of the tech stack for omni-channel is various “edge” hardware such as sensors, mobile computers, and voice-system components that enable workers and processes. Much of the value from this hardware comes from the ability to consolidate data generated on the edge and make real-time decisions with it, says Bruce Stubbs, director of supply chain marketing for Honeywell Safety and Productivity Solutions.
One enabler of these actionable insights is Cloud-based gathering of data generated by sensors in trucks or other supply chain locations, says Stubbs. Honeywell has already leveraged its Cloud platform capability gained from its acquisition of Movilizer to do things like generate Cloud-based insights into “cold chain” events in sectors such as food and pharmaceuticals, according to Stubbs.
Another tech stack evolution Honeywell is involved with is performance analytics of data generated by voice systems. Whereas once the software component of voice systems was mainly about generating effective voice prompts and integration to WMS, now there also is analysis software that combs data generated by voice-based processes to improve performance.
To this end, says Stubbs, Honeywell offers an operational intelligence software for its voice system that provides actionable insights for associates on the floor, such as slot skipping that degrades efficiency, while also generating reports for managers on issues like how actual, current performance compares against productivity standards, or to budget targets.
According to Stubbs, such software is an increasing part of the value proposition today. “We’ve transformed from a hardware-oriented company to a total solutions provider, and that involves a lot this software on the edge to enable connected workers,” says Stubbs. “We’ve enhanced our [operational intelligence] platform to be able look at all the task-related data that exists and leverage it in a real-time, actionable way to improve work processes and head off problems before they start.”
Companies mentioned in this article:
- Capgemini
- Fortna
- Honeywell Safety and Productivity Solutions
- Invata Intralogistics
- New Course
- Swisslog Warehouse and Distribution Solutions
About the Author
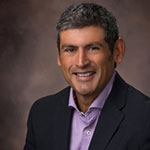
Follow Robotics 24/7 on Linkedin
About the Author
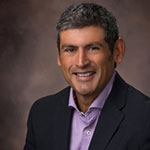
Follow Robotics 24/7 on Linkedin
About the Author
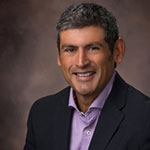
Follow Robotics 24/7 on Linkedin
Article topics
Email Sign Up
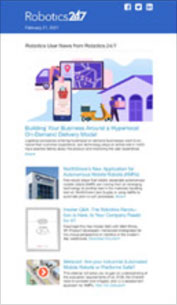
