From working alongside humans in pick-and-place operations to material handling in the warehouse, robots are starting to deliver unprecedented levels of performance. But why now? What has changed in the technology’s composition that has enabled such a transformation? To a large extent, the answer is the introduction of a multitude of new, innovative sensor technologies.
Numerous factors have converged to position sensing technology as the driving force behind the expansion of robot functionality. For starters, the cost of sensors has steadily declined. Growing use of micro-electro-mechanical systems devices has advanced miniaturization and integration, enabling smaller form factors. Furthermore, sensing devices now boast greater energy efficiency and communications capabilities. All these advantages have proven to be crucial. The heartbeat of robotics’ advance, however, lies in sensors’ ability to support previously unattainable accuracy and precision.
Distinguishing Between Accuracy and Precision
Users often make the mistake of seeing accuracy and precision as interchangeable. Within the context of robotics, however, the terms have completely different meanings.
Robotics providers define accuracy as the difference between the requested level of performance and the performance actually delivered by the robot. No robot delivers 100% accuracy; there is always a margin of error. As robotics mature and advance, however, the average error rate has dramatically decreased. This is particularly important because a robot’s accuracy plays a large part in determining the tasks it can perform.
Developers define precision as a robot’s ability to repeatedly perform a programmed task. This is measured by the degree to which a robot can bring its frame or end effector to the same position and orientation over and over again.
Internal and External Sensor Roles
Accuracy and precision affect robot performance in two areas. Internal sensors guide the robot’s operation, such as its speed and room orientation or its effectors’ positions.
Observe an example of this function in the calibration of a robot’s axes. The device’s control system must adjust this measurement regularly. Mounted on the robot’s axes, the measuring sensors (e.g., a linear variable differential transformer displacement sensor) identify the zero point while the axis is being rotated. Without a high level of accuracy here, the robot can only perform simple tasks.
External sensors provide data on the robot’s operating environment. This can involve camera systems, temperature sensors to detect the presence of human co-workers and laser triangulation sensors to determining micrometer-precise distances to—and positions of—tools and the production goods. Many of these applications depend on sensors to provide the accurate, high-speed measurements required by advanced functions.
Additionally, the introduction of sensor fusion has enabled even greater accuracy and precision. This technology combines sensory data from multiple disparate sources, providing a more in-depth picture of the parameter of interest than can be determined by individual sensors.
Giving Robots the Sense of Touch
Robot makers are now adding sensor technologies to their designs that enable robots to more accurately sense their work environments and to more precisely perform tasks. These technologies include force torque sensors and tactile sensors.
Force torque sensors help give robots a sense of touch, allowing them to manipulate objects in less-structured environments with more precision, accuracy and flexibility. Instead of simply following a predefined path, robots with force sensing can adjust to real-world variables and sense when a part is complete or in place.
Tactile sensors impart robots with the precision to delicately manipulate physical objects. An application in which these sensors excel is called piston stuffing—the process of inserting a piston into an engine block. In most cases, the gap around the piston measures less than 1/10 the thickness of a human hair. Vision systems aren’t precise enough to ensure the accuracy of piston stuffing. Only tactile sensors achieve this level of performance, providing a major productivity boost for automotive manufacturers.
The new sensor technologies deliver greater accuracy and precision. These improvements enhance robot productivity, enable a new class of applications and lay the groundwork for the next generation of robots.
About the Author
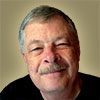
Follow Robotics 24/7 on Linkedin
Article topics
Email Sign Up
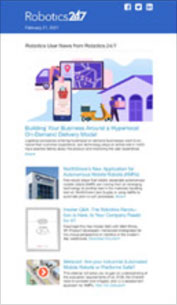