Robot arms equipped with the right safety features can operate in close proximity to people. But not all collaborative robots are built for constant work alongside humans.
The Association for Advancing Automation (A3) defines four major types of collaborative robots recognized by the ISO. Some primarily move autonomously, abiding by visual sensors telling the robots to slow down or stop if people get too close. Others are built with collision sensors that stop robot arms when they contact obstacles. And others still are guided by hand, either in operation or during programming.
Yaskawa America Inc. Motoman Robotics Division (Yaskawa Motoman) produces a wide array of industrial robot arms. Yaskawa Motoman’s “Human-Collaborative,” or HC series of cobot arms, are designed for different kinds of interactions between robots and people.
Cobots designed with people in mind
From the ground up, Yaskawa designs robot arms that are applicable for as many applications as possible. All of Yaskawa’s cobots are IP-67 rated, with food-grade grease and corrosion-resistant paint as standard features.
“Not all applications will need any one of those individual design elements,” said Chris Caldwell, product manager at Yaskawa Motoman. But because each model in the HC line is “safe for any application,” he added that “they can easily be deployed anywhere.”
Caldwell said Yaskawa’s HC10 workstation was designed for a global market - primarily European customers, but with American and Japanese influence. Yaskawa’s designers considered what size doorways the workstation would need to fit through and an ergonomic mounting height to match typical human reach.
I/O cabling, air hoses, ethernet, and other utilities run through the robot arms. For the HC10 workstation, the remaining lengths of cable are routed internally. Caldwell said through-arm and internal cable management prevents utilities from getting caught on objects in the surrounding environment and also enables simplified connections.
HC series cobots also feature a “pinchless” design - which prevents injury if someone gets too close to articulating joints - and additional finishing work to smooth out aluminum castings that prevents abrasion from skin contact.
Fenceless operation for greatest flexibility
If a preliminary risk assessment determines it would be safe, companies can deploy fully “fenceless” cobot arms. Caldwell said fully fenceless operation allows free movement of humans and equipment around a robot at all times during operation without any physical safety barriers.
“With the HC10 workstation, you can drop that in place, not put up any other fencing or guarding around it, and allow that robot to operate in that entire area,” Caldwell said.
Yaskawa’s HC20 and HC30 cobot arms can reach up to 1.9 meters, or just over six feet, from their mounting point. “Ultimately the entire reach of that robot is the amount of space and footprint that that cell can take up.”
Under the right circumstances, human and equipment traffic could be allowed to pass freely through the reach of a cobot arm. But if reach reduction is required for a cobot to operate safely, Caldwell said boundaries can be defined in safety logic circuits. Within functional safety units, software-based limits can be set that restrict areas robots can reach or the speed at which they operate.
Yaskawa’s cobot are built with the same motors, servos, drives and fully cast aluminum construction as its industrial robot arms. But Caldwell said Yaskawa’s customers expect full-time capability for cobot arms to cooperate with humans. To increase throughput, Yaskawa’s cobot arms can run at different speeds depending on proximity to nearby people.
Switching between industrial and collaborative speeds
As defined by A3, safety-monitored stop cobots are designed to stop completely when a human or object enters the work area. But speed and separation type cobots can slow down and continue operating as humans get closer.
Caldwell said when operating in “industrial mode,” robots can move up to 2 meters per second. For a cobot to run at industrial speed, it relies on additional sensors to detect that humans are not in or near its work area.
“If the robot is able to operate knowing that there is no human present, you can get an increased amount of throughput running at a higher duty cycle,” Caldwell said. “But the design is trying to really blend the needs of operating with a human in mind and operating without.”
For “collaborative” mode, a variety of speeds can be defined up to 1 meter per second for multiple collaborative zones.
Caldwell said when a robot is operating at a distance where it can expect direct interaction, speed is typically limited to 200-400 millimeters per second depending on end-of-arm tooling (EOAT) and size of product being handled. Further zones are commonly set at 400-1000 millimeters per second.
On the end of its cobot arms, Yaskawa installed an indicator light that turns green when the robot is operating in collaborative mode - meaning humans can safely approach it - and turns off when the robot operates in industrial mode.
Minimizing footprint while maximizing workflow
One challenge manufacturing and logistics warehouses must consider is how to accommodate the footprint of robotic workcells. The goal is to limit how much floor space each robot takes up.
“In brownfield-type sites where there's already existing work cells set up, you don't worry about fencing in a human,” Caldwell said. “But there are only certain amounts of access points in and out of any kind of workflow.”
While complete fenceless operation is suitable for many applications, Caldwell said the most common deployment involves work cells with some amount of guarding. “That's typically the best compromise to limit the amount of footprint that's dedicated, but also maximize the amount of flow in and out of the cell,” he said.
For example, Yaskawa’s HC30PL depalletizing demonstration setup includes physical barriers on three sides. “That's still considered fenceless because it doesn't have a full interlock around it,” Caldwell added.
Limited barriers combined with fenceless zones allow for flow in and out of robotic work cells of both products and people.
“With some amounts of guarding, you can significantly reduce the overall footprint of the cell that you'd be implementing,” Caldwell said. “That way you can have high-volume traffic or mixed-use traffic.”
Caldwell said mixed traffic scenarios can include robot arms sharing space with humans, other pieces of equipment, or racking.
Easy-to-use pendants and programs
While some robotic systems require advanced coding knowledge to set up, Yaskawa offers user-friendly interfaces and programming software for its robot arms.
Sarah Andrzejewski, product manager at Yaskawa Motoman, said Yaskawa’s Smart Pendant is a tablet-style device with an easy-to-use touchscreen interface for industrial robot programming. Designed for shorter duration use, the smart pendant doesn’t require as much training thanks in part to built-in help and how-to guides.
“It’s really meant for people new to robotics, or they’re looking for simpler programming,” Andrzejewski said. “It’s a lot easier to use than the standard pendant.”
Yaskawa’s Smart Pendant is intended for material handling, pick-and-place, palletizing, machine tending, injection molding, and inspection applications. It is compatible with the company’s YRC1000 and YRC1000micro controllers.
In addition to programs created by technology partners, Yaskawa offers its own installation packages for the Smart Pendant, including Pallet Builder.
Andrzejewski said Pallet Builder is a free, easy-to-use application for configuring palletizing cells. It’s suitable for single case palletizing with support for up to eight total stations. Through Pallet Builder, users teach robots how to arrange boxes on a pallet, showing them where to put each box to form desired stacking patterns.
Another configuration option is Pallet Solver, an offline PC-based pattern generation and cell definition software with online control-based execution and optimization. Pallet Solver allows users to configure palletizing jobs without using a pendant.
“It's geared to make palletizing easier,” Andrzejewski said. “It's best if you have a high mix of products with a high mix of pallet patterns.”
Intuitive hand guided programming
One more teaching option is hand-guided programming. While A3’s definition technically states hand-guided cobots move in “automatic mode” only when steered by a human operator, Yaskawa uses that interaction to teach robot arms without direct programming.
Caldwell said while some robot arms can be manipulated by hand, users still need to program through a pendant or other interface. “We thought if you're hand guiding and trying to make things easy as you're manipulating the robot around, wouldn't it be great if all you had to do was interact with the robot arm?”
Three buttons on the flange of Yaskawa’s cobots allow hand-guided programming. One is held down while moving the robot through a series of points. Another is pressed to teach the robot where a specific point is. The third button’s function is customizable, but Caldwell said it is usually mapped to open and close gripper attachments.
“You can really create most of your robot job - all of the motion and most of the activities - without interacting at all with your teach pendant,” Caldwell said.
Power and force limiting safety features
Caldwell said Yaskawa considers A3’s cobot definitions when designing robots and control systems to create the safest robots possible. Power and force limiting (PFL) cobots are designed for constant human collaboration and equipped with intelligent collision sensors.
PFL is a form of functional safety that allows robots to react to external forces by stopping movement. It also includes limiting the amount of force robots use to begin with. PFL events can include unintentional contact with a human or the robot detecting that an object it tried to lift was heavier than it was supposed to be.
In a robot’s functional safety unit, the amount of force a robot would detect to trigger a PFL event can be defined. Yaskawa built in a pull-back function that follows a PFL event detection, which tells the robot to reverse a set distance so it is no longer pushing against the object it encountered.
Beyond pulling back, an “avoidance” function allows humans working alongside robots to gently push the robot out of the way if they are not ready for it to enter the area. Yaskawa enables its cobots to be programmed to enter a “time out” mode, waiting for a specified amount of time, and return to the work area at a defined speed.
“When you have a human and a robot interacting in the same space, humans are not always great at meeting the exact same cycle times,” Caldwell said.
Yaskawa also includes reset buttons on robot wrists that light up if a cobot stops specifically for a PFL event.
While Yaskawa’s default safety sensors are currently all touch-based, Caldwell said the logic circuitry allows for the addition of additional types, including vision sensors, area scanners, and light curtains.
Caldwell said Yaskawa will be bringing its Motoman Next AI-enabled robot platform to market over the next year. The new generation of Motoman Next models will feature integrated cameras that, although not safety-rated, allow Yaskawa’s cobots to expand their environmental awareness.
Want to learn more about cobot arms? This article was featured in the April 2024 Robotics 24/7 Special Focus Issue titled “Collaborating with robot arms, platforms.”
About the Author
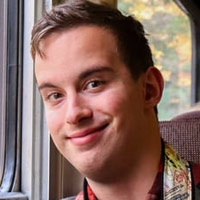
Follow Robotics 24/7 on Linkedin
Article topics
Email Sign Up
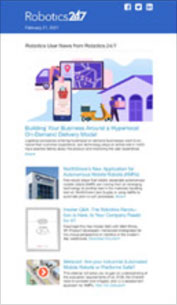
