Robots made exclusively of hard materials prove their worth every day in industrial applications, excelling at repetitive, physically demanding and dangerous tasks that human counterparts cannot take on. Some robotics providers, however, want to steer the design and construction of these machines in a new direction.
Driven by robotic use cases in healthcare and cooperative human assistance applications, designers have begun to develop less rigid, more mechanically compliant robots. This new class of machines is constructed of soft materials engineered to mimic properties of soft biological tissue, matching its compliance, elasticity and low density.
These properties allow soft robots to bend, stretch and conform to other objects, as well as make physical contact without imparting large forces. This class of robots can operate more safely around humans and better handle fragile objects, such as fruit, electronics and human organs.
New Materials Flex Their Muscles
The current generation of robots derives its “soft” qualities from newly developed materials and existing substances used in new ways. These include specialized polymers, gels and fluids.
“Use of functional polymers in soft robotics can impart functional flexibility and multifunctionality in addition to mechanical flexibility,” says Jessica Liu, graduate research assistant at North Carolina State University. “Soft robots can be designed to bend and twist with high curvatures, allowing them to navigate within confined spaces.”
Another advantage of soft materials is that they can be integrated into other material systems without altering natural mechanical properties. “Most soft materials can be cast in a 3D-printed mold or directly printed into 3D shapes using additive manufacturing,” says Carmel Majidi, associate professor of mechanical engineering at Carnegie Mellon University. “When combined with conductive fluids or elastomers, they can also be used to make soft, flexible and stretchable circuits, sensors and radio antennae.”
Morphing Materials
One approach to building soft robots is to use “shape-memory” materials, which change shape and stiffness in response to heat or electrical stimulation. Two popular types of shape-memory material include nickel-titanium alloy and liquid crystal elastomers. Liquid-crystal elastomers are soft polymers that can remember their shape after they have deformed, springing back to their natural rest configuration when stimulated (Fig. 1).
Over the past few years, the Soft Machines Lab at Carnegie Mellon University has been building soft robots using nickel-titanium alloy. These machines can perform a wide range of locomotion modes, including walking, crawling, rolling, jumping and swimming.
More recently, the group has developed a type of electrically conductive liquid crystal elastomer that can be stimulated with electrical current.
“This is accomplished by filling the elastomer with droplets of a metal alloy that is liquid at room temperature,” says Majidi. “These liquid metal droplets form a connected network within the elastomer that allows electrical current to flow through the material and induce the shape-memory effect through local heating. Applications of this composite include a robot ‘muscle’ and stretchable circuit wiring that can remain functional when punctured or torn (Fig. 2).”
Benefits of Soft Materials
Compliance has proven to be a main advantage offered by these machines. One of the most important advantages lies in the robots’ ability to dynamically adapt to changing environmental conditions better than conventional robots made of rigid materials. For example, soft materials and their built-in feedback mechanisms allow robots to alter their shape to accommodate new operating demands, such as squeezing through confined spaces.
“Soft robots adapt to dynamic or unpredictable environments better than hard robots, because when they come into contact with elements of the environment, they don’t need sensors to react to an unexpected stimulus,” says Philipp Rothemund, postdoctoral fellow in the Keplinger Research Group at the University of Colorado, Boulder. “They simply deform around the object.”
In addition to enabling greater adaptability, the robots’ compliance also offers designers several significant benefits. For example, the low elasticity, low density and versatile chemistry of these materials reduce weight, cut development costs and make it easier to reconfigure the machines, streamlining the design and implementation of custom units.
Self-Help Features
Along with the compliance that brings so many benefits to soft robots, the materials used to construct these machines also open the door for capabilities that can reduce design complexity. One of these is self-sensing.
Among soft robot materials, dielectric elastomers—an elastomer set between two electrodes— and other similar-acting components present self-sensing properties. The dielectric “sandwich” acts as a capacitor. When opposite charges are applied to the electrodes, they are attracted to each other, squeezing the dielectric and changing its thickness, which in turn changes its capacitance. With a known voltage input and capacitance readout, an engineer can derive the thickness of the dielectric, and from there tell if the material is fully actuated or has come into contact with something that is preventing its full actuation.
In addition to self-sensing capabilities, some soft robots also have self-healing features. The machines make structural repairs by applying specially engineered materials via chemical reactions, fluid flow and material phase change processes.
For example, chemical reactions based on reversible hydrogen bonding can be used to reattach torn or severed robot components.
Using a different method, robots can repair torn or severed thermoplastic components using a material phase change process in which the machine applies heat to fuse the damaged parts back into their original place.
Looking at another repair scenario, soft robots with damaged conductive pathways can use a fluid flow process to form new connections. Here, the robot applies electrically conductive materials that contain droplets of liquid metal, which form new pathways when the liquid metal flows into surround areas of the robot.
Material Challenges
Even with these benefits, robot designers also should be aware of the challenges yet to be overcome. One of the biggest obstacles currently encountered by engineers stems from the fact that the material science supporting soft robotics is still in the early stages of its development. As a result, a number of sticking points continue to hinder soft robotics evolution.
For example, the current collection of materials used by soft robot developers offers only limited functionality. Although elastomers and fluids have proven to be a good match for the mechanical properties of biological materials, they typically do not have adequate electrical, thermal or electromagnetic properties to replace the functions of motors and electronics.
This shortcoming, however, has not escaped the attention of leading developers of soft robots. In fact, much of the field’s work focuses on creating new types of soft multifunctional materials that can address these issues.
The process of developing an inventory of materials that can bring soft robotics to their full potential, however, has its own challenges. One of the greatest of these is that developers have yet to fully analyze the materials being used. Developers must attain a better understanding of the materials in use before optimizing for soft robot construction.
Another obstacle is the nonlinearity of soft materials.
“Because soft materials do not behave linearly to applied forces, unlike hard materials, new design and testing tools need to be developed to analyze soft materials,” says Rothemund. “In addition, soft robots require fewer sensors to respond to stimuli, and fewer sensors means fewer control systems. Whatever control systems a soft robot does need would have to handle nonlinearity, and therefore are more complicated to implement.”
Along with nonlinearity, designers must also contend with issues arising from soft materials’ irregular deformation.
“A challenge with using soft materials is that the deformation of the robot becomes unconstrained,” says Majidi. “Rather than just moving at a discrete number of joints or motors, a soft robot can deform at any location due to the natural compliance of its materials. This introduces challenges in control, state estimation and robot planning.”
Just Getting Started
Still a relatively new field, soft robotics still must define their place in a growing number of industries. This poses challenges, but it also provides opportunities for creative ideas.
To maintain growth and adoption, soft robot development teams must cultivate expertise in a broad spectrum of engineering disciplines.
“Realization of a soft robot that senses and responds to its environment requires expertise in materials, electrical and mechanical engineering,” says Joseph Tracy, professor of materials science and engineering at North Carolina State University. “In one application space, a soft or rigid robot would be able to conduct a wide range of tasks and perform them with a high level of control, mimicking human behavior. The challenge is how to select the design that will give the desired result.”
About the Author
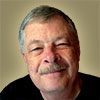
Follow Robotics 24/7 on Linkedin
Article topics
Email Sign Up
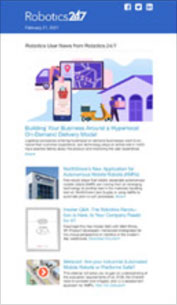
