PITTSBURGH—As warehouse operators increasingly turn to automation to solve some of their biggest supply chain challenges, what do they need to keep in mind as they scale up?
That was one of the central questions tackled during “The Supply Chain Revolution” panel at the Cascadia Connect Robotics, Automation, and Artificial Intelligence (RAAI) conference here this week.
Composed of executives and founders from some well-known U.S. robotics companies, panelists included Bernard Casse, founder and CEO of RIOS Intelligent Machines; Thomas Evans, robotics chief technology officer at Honeywell; Erik Nieves, co-founder and CEO of Plus One Robotics Inc.; Damion Shelton, co-founder and CEO of Agility Robotics; and Lance VandenBrook, CEO of IAM Robotics.
“We thought there were a lot of lessons that could be extracted from the experiences of the founders here, said moderator Firdaus Pohowalla, Cascadia Capital’s managing director for robotics, automation, and artificial intelligence.
Topics of discussions included the labor shortage, the e-commerce boom, system interoperability, ramping up robot production, robotics as a service (RaaS), and more.
Where should warehouses automate first?
Nieves said warehouse operations can generally be broken up into two types of workers: those who move stuff around and those who manipulate and do stuff with their hands.
He said there are technological advancements happening for both jobs, but noted that autonomous mobile robots (AMRs) are progressing faster than manipulation technology.
When installing robots in nascent markets, an unwritten rule is that operators want to be able to still be able to operate efficiently if the automaton was to be removed, Nieves explained.
“If you come to [warehouse operators] and say, ‘I understand workforce development and workforce shortages, and I’m here to bring in automation,’ The first thing that comes to their mind is, ‘If this doesn’t work, how do I get back to doing this manually?’”
Nieves said AMRs could work in that scenario since they can be eliminated easily if they aren’t found to be useful.
Manipulation tasks are more complicated because they involve more cooks in the kitchen.
“There are more noses associated with people doing this than driving a forklift,” Nieves said. “So that manipulation class, those tasks, likewise breakdown into categories, whether it’s pick and pack, pack-out operations, etc.”
People often ask which would be the best task to automate first. Nieves said it would be wiser to think about which one to automate last.
“Operations are either subtractive or additive,” he said. “I’m either breaking down a pallet, or I’m creating one. I’m either loading the truck, or I am unloading the truck. Well, guess which ones are easier? The subtractive ones are. The additive ones now bring additional constraints in volumetric planning and all other things that need to be done.”
Labor shortage still the biggest warehouse pain point
Casse said the two biggest challenges facing the industry are labor shortages and high labor turnover.
“That’s essentially what we and all robotics companies are solving,” he said.
Nieves agreed with Casse’s assessment.
“The demand is outstripping the ability of the supplier to keep up with labor availability,” he said.
Casse said there is “immense opportunity” for robotics companies to becoming a bigger part of the warehouse process.
In the early days, robotics companies worried about how workers would perceive or interact with the robots, he said.
“But what we found is that they are actually very happy that there are robots in house,” he said.
Workers who were once doing basic tasks are now being given the opportunity to earn certificates and become robot operators, he said.
Jumping off that point, Nieves claimed that “no robot ever deployed in any warehouse in America resulted in a pink slip.”
“It’s just reallocating the labor to higher-value tasks,” he added.
Educating the workforce
VandenBrook said there is an adjustment period for workers to understand their new roles when robots are brought on.
“There’s this element of stepping up and in terms of the type of work that you are going to be doing,” he said. “Rather than being a picker, you’re wrangling maybe 15 to 20 robots.”
“I think once you get them on the platform, they see very quickly the benefits of having a robotic platform in the warehouse,” said VandenBrook.
Shelton said with productivity demands increasing, automation is becoming more important. To help address sourcing and other issues, Agility Robotics started building its legged robots domestically, which has paid off, he said.
Interoperability needs to be key
Evans said customers are increasingly demanding software systems that integrate with their robotics hardware.
“All that has to be orchestrated in a very concise and precise way,” he said.
VandenBrook said interoperability is “critical” as companies such as Amazon and Shopify continue to invest billions to build up fulfillment centers.
“As an ecosystem, clients are going to demand the best point solution for their operation in order to give them a competitive advantage in the marketplace,” he said. “I don’t see that changing in the future.”
About the Author
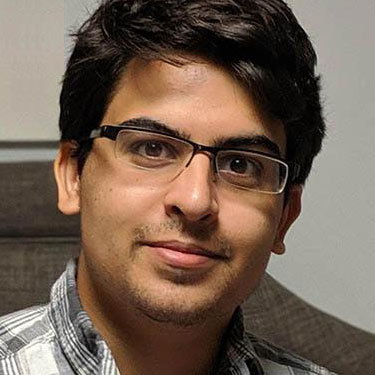
Follow Robotics 24/7 on Linkedin
Article topics
Email Sign Up
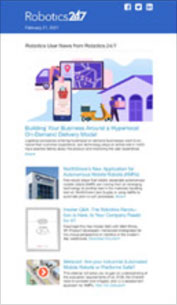
