Your next eyeglass order could be fulfilled faster and more accurately with robots. OSARO Inc. and Zenni Optical Inc. today announced that they have automated the “last meter” of Zenni's fulfillment center in Novato, Calif. Three OSARO Robotic Bagging Systems will prepare eyewear orders for shipment to U.S. customers.
The companies claimed that the deployment is the first time in the industry that a robot will work with an automated bagging machine to ensure that a customer’s unique eyeglass order is placed into the correct bag for shipment. OSARO said its vision and grasping technology enables robots to accurately and quickly pick items.
“We are focused on quality and innovation,” said Simon Goh, director of distribution and facilities at Zenni. “With a mountain of online orders and a persistent shortage of labor, we looked to OSARO to take us to the leading edge of technology to be sure our customers receive fast and accurate processing.”
Zenni said its mission since 2003 has been to make prescription eyewear affordable and accessible to everyone. The online retailer said its complete prescription pairs start at $6.95 and average just over $40. It has sold more than 45 million frames sold worldwide.
Robots help Zenni see e-commerce efficiency
“The stakes are high here: special-order, high-value items that must be bagged and labeled correctly to ensure they are sent to the right customer,” stated Derik Pridmore, CEO of OSARO. “Our extensive experience in other e-commerce production environments, coupled with our machine-learning capabilities, enables our robotic bagging system to meet customer production targets and to deploy workers onto more important tasks.”
OSARO said its systems can meet challenges including high SKU inventories, complex packaging, and fragile items. The San Francisco-based company said its machine vision and control software is designed for goods-to-robot (G2R) use cases in warehouses.
At Zenni's fulfillment center, OSARO's pick-and-place robot will process online orders. Zenni has a team of workers capable of handling 10 orders per minute, noted the companies.
In addition, the partners said that robots can mitigate the staff turnover and shortages that are plaguing the fast-growing e-commerce industry.
OSARO describes differentiators
Pridmore replied to the following questions from Robotics 24/7:
How did Zenni Optical find OSARO?
Pridmore: We first became aware of Zenni’s needs through one of our trusted automated bagging equipment suppliers, Pregis.
What differentiates OSARO from other vision-guided picking providers?
What differentiates OSARO is a combination of three things:
- Smarter automation and superior vision software
- Lower-risk business plans, with robotics as a service [RaaS]
- Comprehensive OSARO Hypercare support to guide customers through the complexities of assessment, integration, testing, and deployment
How much did your company have to customize its vision-based picking system for Zenni, and if so, how long did it take?
Pridmore: Our machine vision system generalizes well to a vast array of potential e-commerce items and handled the Zenni cases with ease. If a new or unique item is introduced to the system, the vision algorithms can be retrained to optimize performance in a matter of days.
How much training was necessary for picking, orienting, and reading each package?
Pridmore: The Zenni item set is unique in that the items are all uniform eyewear cases—size, shape, color, etc.—and, at the same time, uniformly difficult for traditional machine vision systems—identical, shiny, translucent packaging, and jumbled randomly in a bin.
OSARO's vision system performs well in such challenging scenarios and was able to work well for Zenni from the get-go.
Did the picking system have to make any accommodations for the fragile nature of eyeglasses?
Pridmore: Since our system uses suction cups and advanced perception pipelines to understand the size, shape, and weight of each item, our robots are able to handle delicate items like glasses gently and precisely at speed.
What's the throughput with the picking system compared with manual processing?
Pridmore: The OSARO Robotic Autobagging Solution was designed to meet or exceed human operator performance, not just in throughput, but in quality, accuracy, and uptime.
For “last-meter fulfillment,” is there a handoff from or to people at other stages? How much human supervision is necessary?
Pridmore: No, the OSARO Robotic Bagging System automatically picks, scans, and places the eyeglass cases into a polybag, which is labeled and sent downstream for shipping. The automated bagging machine is integrated with the robot for a complete solution.
Downstream cases of bags are handed off for delivery by a carrier.
Did Zenni buy the systems outright, or is it using a RaaS model?
Pridmore: Although OSARO offers multiple purchasing options, Zenni opted for OSARO’s low-risk RaaS model, which offers immediate ROI [return on investment] and guarantees performance without the upfront capital expenditure.
About the Author
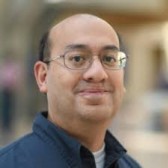
Follow Robotics 24/7 on Linkedin
Article topics
Email Sign Up
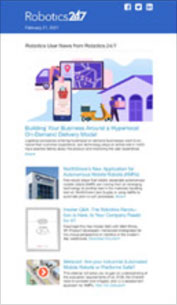
