Small to midsize distributors have begun to adopt automation. For instance, we featured NorthShore Care Supply's use of autonomous mobile robots last year. Now, robotic palletizing has sped up receiving operations, taken labor out of the process, and created a safer work environment.
In July of 2020, I toured NorthShore Care Supply's recently opened 173,000-square-foot distribution center (DC) north of Chicago. Adam Greenberg, a University of Chicago MBA grad, founded the company in 2002. He got the idea for incontinence supplies after some family members who were going through illnesses expressed their reluctance to purchase products like Depends at the grocery or drug store.
The idea of purchasing online for reasons of privacy and the convenience of home delivery seemed natural. Once Greenberg turned on the website, he learned of his customers’ frustrations with the performance of many of the products available in stores. Greenberg turned his focus to higher-quality products, a customer-service staff able to answer embarrassing questions, and fast and easy delivery. A leading business was born.
NorthShore Care Supply grows into automation
After operating for more than a decade from several smaller facilities, including an 86,000-sq.-ft. distribution center, NorthShore Care Supply moved about 10 miles to Green Oaks, Ill. The new DC doubled the square footage and provided room for a company that was experiencing 30% year-over-year annual growth.
The new facility—the company’s fifth since its founding—featured more than additional space. It also contained a high level of automation for a small to midsized company. The centerpiece was a robot-to-goods picking system designed by Numina Group that used autonomous mobile robots (AMRs) from Waypoint Robotics, which Locus Robotics acquired this year.
The ability of Waypoint Robotics' AMRs to carry up to 700 lb. was essential because NorthShore Care ships full cases to its customers. Those cases were delivered to a fairly automated packing, labeling, and shipping line.
Greenberg, the company's president, said he embraced automation for several reasons: First, it was now affordable for midmarket companies like NorthShore Care Supply.
Second, automation allowed Greenberg to build capacity into the system—he saw a 40% to 50% improvement in the speed of picking along with improvement in accuracy. And finally, automation allowed him to do more with less.
“This is not an area with a large blue-collar labor force,” Greenberg said. Amazon, Uline, and Medline operated large DCs nearby, competing for available warehouse labor, he added.
“We were struggling to find people looking for a permanent job, and temps wanted to jump from warehouse to warehouse,” he recalled. “That was a challenge for the five years before COVID-19.”
Robots grow with inventory
Fast forward to July 2021, when I toured the Green Oaks facility once again. The AMRs were still traveling through the aisles, associates were busy picking to the robots and moving product through the packing stations, and lift truck operators were moving pallets to replenish pick locations.
I saw two big differences: Significantly more inventory was in the warehouse than in July 2020, and at the receiving dock, two associates were unloading cartons onto a powered conveyor from inside a shipping container. Those cartons were then directed to a robotic palletizing cell designed by systems integrator Exact Automation.
There, empty pallets were automatically dispensed from a pallet dispenser. Cartons queued in one of two staging lanes, and a FANUC robot picked them up two at a time to build one of 20 distinct palletizing patterns.
Like the AMRs in picking, robotic palletizing brought a whole new level of efficiency to the receiving operation when it was desperately needed.
“It was taking us eight man-hours per container to unload and most of that was on overtime,” Greenberg said. “We’ve only had the palletizing cell operational for a few months, and we’re at 3 man-hours for about 80% of the containers we unload. With further optimization, we think we can get that down to 2.5 hours per container.”
In addition, the reduction in labor associated with receiving also reduced the potential for repetitive stress injuries from repeated lifting, creating a safer work environment.
What a difference a year makes
Like last month’s case study on Top Notch Distributors, NorthShore Care Supply goes deep in a niche Industry. Like many small to midsize distributors of specialty products, both companies must compete on price and customer service with retail and e-commerce giants, including Amazon.
They often distinguish themselves on selection and customer service. That includes representatives who are knowledgeable about their product lines, along with consistent and reliable order fulfillment and delivery. People need these products when they need them.
As the price of computing power and electronic components has come down, automation is enabling small companies to be competitive. To get the most from emerging technologies, Greenberg said he he looks for cutting-edge providers that may be looking for a beta site to test their systems.
Since my visit to NorthShore Care Supply, the business has continued to evolve. Meanwhile, Greenberg is experiencing the same labor shortages and supply chain disruptions as other manufacturers and distributors, regardless of size. So, what has happened?
First, the privately held company has continued growing, driven in part by the “general boom in e-commerce in all categories,” said Greenberg. “Before COVID, the biggest share of our marketing was to get people out of the stores and into the routine of buying online. Now, if they do go into a store, not everything is on the shelf, and in this category, a necessary specialty item, buying online is more reliable.”
Second, private-label NorthShore branded products are becoming more of a focal point of the business. “It has grown from 80% of the business a year ago to more than 90% today and will be more than 95% of our business by the end of this year,” Greenberg said.
The increase in private-label product increases NorthShore’s reliance on manufacturers in the U.S., Europe, and China, and it now ships to customers in Europe. As a result, the company is experiencing shutdowns, shortages, and unpredictable shipping.
“Our overseas suppliers are backlogged, and our domestic suppliers are shut down,” said Greenberg. “Lead times from Asia have grown from five weeks to 15 to 20 weeks, and we have to add an extra four to six weeks from Europe. And we’re paying extra.”
Because NorthShore Care’s customers rely on its products, it orders “just-in-case inventory, and then we add some,” he said, explaining the reason for the extra inventory in the facility compared with a year ago. As a result, “our receiving operation is experiencing twice the growth rate of our outbound operation,” Greenberg noted.
Meanwhile, containers arrive when they arrive. Some weeks NorthShore Care gets 10 to 15 that have to be unloaded and turned around promptly to avoid demurrage fees. On other weeks, the facility gets none. Add in labor challenges, the facility was ripe for an expansion of automation into receiving.
NorthShore Care Supply adds robots
The unpredictability of shipments meant NorthShore Care couldn’t really hire full-time staffers for occasional work. Temp labor was scattershot at best.
“One day, we had 12 temps lined up to unload containers,” Greenberg said. “Only five showed up, and only one stayed for the whole shift. It’s hard, manual labor, and other very large DCs in our area are paying big bonuses to attract help.”
He tried to rely on overtime, but eventually continual overtime burns out the existing workforce. “They’re worn down from manually unloading trailers, and it’s hard to replace them,” Greenberg said. “It became an absolute necessity to automate that part of the operation.”
NorthShore Care investigated robotic palletizing during the initial design of the distribution center, but it was more than the company thought it could handle at the time. “We decided to wait until we were at an optimized state with the other projects,” Greenberg said.
Research for the project began in the fall of 2020. Along with discussions with existing vendors, an important resource was the website for PackExpo’s 2020 virtual event. NorthShore Care sent out requests for proposals to six potential vendors. It received proposals from four, including three that provided detailed plans.
“We ended up adjusting the layout a number of times to shrink the overall footprint of the solution,” Greenberg recalled. “Initially, we thought we wanted more conveyor and space than we installed to handle more product and more SKUs at the same time. In the end, we decided that warehouse space could be a factor in the future, and to focus on one SKU at a time coming out of the containers. That way, we didn’t need a lot of room for queuing and staging.”
Those changes also allowed NorthShore Care to keep the cost of the project under $500,000. The projected return on investment was two years, with a goal of getting unloading and palletizing down to two manhours per container and to do it all without overtime. It chose Exact Automation as integrator for several reasons:
- Proximity: Exact Automation was located less than an hour away from NorthShore Care’s facility.
- Expertise: Robotic palletizing was a focus for the integrator.
- Availability: Exact was able to commit to doing the project right away, and it had vendor connections to source the equipment and components needed to complete the project in a timely manner.
The contract was signed in March, and the robotic cell was fully operational by the middle of July 2021.
Palletizing project proceeds
The palletizing project took advantage of reinforced concrete that had been poured when the facility was built and a mobile, extendable powered conveyor that NorthShore Care had purchased for the original go-live.
“We knew when we moved into the building that everything we could do ahead of time to make manual labor more efficient would be worth it,” Greenberg said. The conveyor was mounted on rails so it could slide between two receiving docks.
“We can only unload one trailer at a time because we only have one extendable conveyor,” explained Greenberg.
The operation is relatively simple: Two associates are assigned to a container, and most containers have one or two SKUs each. One of the associates scans a carton so the palletizer knows what to expect, and then the pair unloads cartons onto the powered conveyor.
Cartons are directed to one of two staging lanes. Once cartons are staged, the robot picks them two at a time to build a pallet according to stored patterns. Once a pallet is complete, it’s ejected to a pickup location where a lift truck operator will get it and take it to storage, or use it to replenish a picking location. NorthShore has reduced by nearly 60% the time required to unload a trailer, plus the eliminated overtime in the receiving process.
Company stays on automation path
Modifications include a bypass module for SKUs that are slow movers or infrequently received. It made more sense to palletize those by hand rather than create a pre-loaded stacking pattern.
“When the unloaders scan a bar code in the trailer, they skip the two pick lanes and are ejected to a manual palletizing lane,” said Jared Bell, who recently joined the company as the vice president of operations and business development.
NorthShore is not done automating. Future projects may include automatic lift trucks or pallet-handling AMRs for non-value-added travel, such as from receiving to a drop zone for putaway, according to warehouse manager Yutaka Takaki.
“As we’re moving more and more pallets, that could make sense,” he said, adding that the company has done preliminary work to bring more automation to packing. “The timing isn’t right, but we continue to talk to vendors,” Takaki said.
Greenberg said he believes that continued automation is critical to NorthShore Care’s success. “Getting orders out is so critical to us,” he said. “Automation makes it easier for us to be in control of our own destiny. If you can afford to make the right investments, you can deliver the customer experience you need to be successful.”
About the Author

Follow Robotics 24/7 on Linkedin
Article topics
Email Sign Up
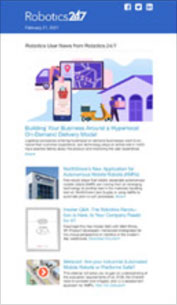
