With the rapid growth of e-commerce, warehouses and logistics chains are increasingly turning to automation.
An increasing number of warehouses are choosing to buy mobile robots to replace traditional fixed automation, according to IDTechEx.
Traditional automation solutions, such as retrieval AS/RS, automated storage shuttles, automated sorting, robotic palletizing, and conveyor systems, are mostly complex and fixed systems. But recently, AGVs, AMRs, and mobile picking robots are gaining traction in the market for their easy installation, value, flexibility, and scalability, the research firm found.
Based on the market research report “Mobile Robotics in Logistics, Warehousing and Delivery 2022-2042,” IDTechEx summarized four reasons why mobile robotics adoption is growing.
AMRs easy to install
Fixed automation systems may take months to install and involve building large racks and long conveyors. The installation is always labor intensive, costly, and sometimes is not done by the automation system providers themselves.
Even though some mobile robots are dependent on fixed navigation infrastructure, they require little additional installation. Set up typically only requires laser reflectors, magnetic tapes, inductive wires, and barcodes/QR codes. Software initialization can usually be completed remotely or on the cloud.
Hence, the installation time for AGV systems typically only takes 2-6 weeks, the research firm reported. For autonomous mobile robotic units, the installation can be shorter as robots only need to be shown around the facilities and no additional change to the environment is needed.
A smart return on investment
A large amount of up-front capital is required to implement fixed automation. But according to IDTechEx's report, the up-front cost for mobile robots could be merely about 1/3 of that of fixed automation.
And installation, maintenance, and powering of fixed automation also cost more than mobile robots.
Therefore, the ROI of mobile robots is about 1-2 years. For fixed automation, it can be 5-10 years.
Easy to adapt
Changing fixed automation systems can potentially cost more money and time than installation and can cause production delays.
Mobile robotic systems are much more flexible, the research firm said.
Even though AGVs need the support of infrastructure, changing fleet tasks only requires re-arranging markers like QR codes or magnetic tapes, which are much easier to change than re-installing fixed automation.
Not to mention that AMRs do not need any supporting infrastructure and are even more flexible, the market research firm said. Mobile robots are suitable for agile material handling or production lines. Mobile robotic systems occupies less or negligible space in warehouses, enabling a more complex and flexible material flow route.
Scalability is key
Once the fixed automation is installed, it is hard to scale up. But the fleet size of mobile robots can be easily scaled so that companies can cope with demand peaks. In addition, mobile robots help warehouses or factories keep lean operations, the market research firm found.
Although mobile robots can work all day with only a few breaks for charging, they are only able to carry a relatively limited load for each task; but fixed automation can continuously transport materials seamlessly, according to the market research firm. So, in large warehouses, mobile robots may not be as efficient as fixed automation for large material flows, the research firm found.
But certainly, mobile robots can always be used in concert with fixed automation, optimizing the processes in warehousing, it said.
Article topics
Email Sign Up
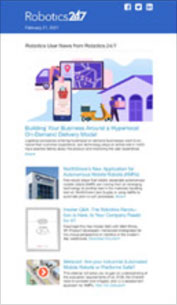
