The rise of automation in warehousing and distribution applications is often in contrast to the historically manual approaches in these environments. Manufacturing, on the other hand, has long been accustomed to automating to ensure productivity, efficiency and consistent product quality. However, in light of recent technological advances and falling price points for materials handling solutions, the manufacturing sector is uncovering significant opportunities for improvement.
“Through the 90s and well into the 2000s, manufacturing efficiencies were driven from 80% to 95% despite hardly any investment in manufacturing technologies after the 80s,” says Sudhi Bangalore, head of smart manufacturing for Wipro. “With modern technologies, they are now going after those last few percentages, which they never could have achieved even if they practiced lean Six Sigma for years.”
Lean manufacturing, nearshoring and workforce demographics are among the mega-trends driving the pursuit of modern manufacturing automation solutions, but the problem and solution are often surprisingly straightforward.
“Machinists and skilled assemblers are hard to find, and labor cost reductions are on the list of objectives, but surprisingly not always the top priority. Of the top 10 items, it’s toward the bottom,” says Tom Steininger, Dematic’s market development director for manufacturing. “Different things are important to each manufacturing segment, whether automotive, electronics or industrial components, but we found they all consider what they call ‘internal order accuracy’ to be the most important thing.”
Manufacturers are recognizing that the accuracy and efficiency of material movements between manufacturing cells and islands of automation is underdeveloped. For example, it’s common to see a lot of robots welding and assembling in a given manufacturing facility, which can give the impression of state-of-the-art capabilities. But Steininger says there is much less attention paid to how each automated cell is fed.
“Many are still prepping or performing lineside deliveries with manual processes while managing inventory on an old legacy system that isn’t very robust,” Steininger says. “There’s so much focus on producing the final product that the systems that feed the operation aren’t more automated, which limits their visibility and ability to keep those lines moving or optimized.”
By automating these materials handling processes or leveraging data collection technologies, manufacturers can create a holistic production process while enjoying more control, efficiency and predictability.
Assembling success
There is plenty of low-hanging fruit, but the process of introducing or more tightly integrating automation technologies can require substantial change management. If not already in place, a regular and thorough review of all processes is essential, says Miguel Fabra, CEO of Modula.
“Too many have thought that when they install an automated system, it would solve all their problems,” Fabra says. “They should realize they could need to reorganize the process and even the company. The whole way of managing is different.”
Successful combinations of robotics, mobile robots, shuttles and other automated storage and retrieval systems (AS/RS) have enabled manufacturers to flatten production and achieve efficiencies while preserving flexibility. Matt Wicks, vice president of product development for Intelligrated’s manufacturing systems division, describes an automotive manufacturer that replaced a manual cart system with an automated storage buffer. Previously, carts were wheeled to a marshaling area, and lineside deliveries involved people looking for the one cart with the right plate.
“Instead of utilizing a conveyor and sorter solution, they opted for a wireless mobile robot with automated storage buffer and shuttle,” Wicks says. “The work cell is small and the system is small, but because of the lower cost to invest in the technology and integration, they were able to justify the investment to replace a six-person operation.”
Another customer had order fulfillment challenges as it worked to get customized orders out the door. A suite of new automation includes an AS/RS where work in progress is staged, retrieved, updated and stored again. Some parts of the manufacturing process happen early, and product is stored in the AS/RS. When orders drop, components are sent out to the manufacturing system and then back to the order fulfillment system. Completed donors can be taken out of the AS/RS and delivered to a robotic depalletizing cell, which breaks pallets down to the case level and delivers them to a shuttle storage solution. From there, orders head to customization areas before being delivered to conventional palletizers.
“This is where there needs to be tight coupling between manufacturing and warehousing and distribution functions,” Wicks says. “They aren’t separate, and in fact order fulfillment is actually driving the manufacturing process. It’s a holistic look at manufacturing processes and inventory management.”
Robots and shuttles will not always outperform conveyor and sortation solutions, which have also been adapted to manufacturing environments in creative ways. Alex Kushner, sales and proposal manager of sortation and distribution for Beumer, has seen growth in applications using sorters for kitting.
“In general, they’re using the sorter as more of a transportation mechanism that interfaces with an AS/RS, where a shuttle provides product to the sorter system then feeds it back to the AS/RS,” Kushner explains. Components in a tote are staged and inducted directly to the sorter with no human intervention, creating a goods-to-person system rather than the conventional pick-and-pass manual approach.
“There’s a lot of flexibility with a sorter to adjust those kits dynamically, as opposed to a manual environment when there’s a changeover needed for different kits,” Kushner says. “When interfacing with an existing warehouse management system, the biggest obstacle to this kind of solution is the availability of data, including a well-populated item master, cube data and prioritization.”
A sense for coordination
Effectively managing and maintaining product data is an ongoing challenge given the rapid pace of change in manufacturing environments. Automated systems might enable efficient and flexible movement of parts and kits, but componentry sometimes struggles to adapt to the changing characteristics of those materials.
Packaging and product innovations are constant and can wreak havoc with scanners and image readers designed for more consistent production patterns. Food and beverage sees changes throughout the year, with different background colors and packaging materials. For electronics, available space on packaging is at a premium, so manufacturers look for ways to make codes and labels smaller. In automotive, the concept of lean manufacturing means continuous change in capabilities on the line, even from shift to shift.
Brian Boatner, director of ID product marketing for Cognex, says these challenges have prompted enhancements in the algorithms behind camera systems and hardware modularity. Changing applications might call for a greater or lesser standoff distance, different lighting to create contrast for image recognition, different lenses or optics mounts.
“Authentication is a growing trend, and manufacturers want to serialize, authenticate and trace products in the field, but most customers are not fully implementing traceability to their best benefit,” Boatner says. “Real-time monitoring systems (RTM) are the next step, and can enable predictive maintenance and monitoring of production issues. More customers are realizing the benefit of not just using ID readers as a single-point means of serialization, but as a tool to harness all the data readers generate to reveal trends like which lines are operating more efficiently than others.”
In addition to aggregating data from different machining cells to track read rates, assess process control methods or anticipate problems, Boatner says RTM systems can allow technicians to use phones and tablets to monitor, troubleshoot and deploy individual readers. Enabled by mobile applications, technicians can access exploded views of modular readers and remove or interchange components to adjust the reader’s ability to read, for example, shinier packaging of different-colored background material.
Business intelligence from manufacturing systems can enable rapid diagnoses for granular issues, so that data from a single photo eye on a divert can be transformed into actionable information.
“From a connectivity standpoint, the tools to adapt disparate systems have come such a long way in the last five years, and it’s not as daunting as it used to be,” Wicks says. “But the more data you get, the harder it can become to make meaningful conclusions, so the trick is to identify the quality of the information to make quality decisions.”
Successfully isolating the most important data points can provide some impressive results, Wicks says. He offers the example of a client whose senior vice president previously attended the company’s Monday roundtable with a lot of paperwork.
“Leadership would point out that there was a production issue last week during the New Jersey facility’s third shift, and he would have to flip through a giant stack of paper looking for relevant information,” Wicks recalls. “Now he brings a tablet, finds New Jersey, clicks, zooms and immediately sees that the temp agency was supposed to send 13 workers for that shift but only sent 10.”
Producing a plan
Wipro’s Bangalore emphasizes that the abundance of data from automated systems must be supported by people who understand how to create an ideal process and are empowered to turn a plan into action.
“Once you have the right pieces of data, then you have to ensure it doesn’t just stay just a proof of concept, but actually gets some legs,” Bangalore says. “If you look at what comments we’re seeing, everyone is wondering what is the mix of effort required between data and the value it brings, and how do you then leverage the data with the right processes. Then it’s about identifying the hard automation and mechanical infrastructure that will support these concepts, like batches of one.”
Even if a manufacturer achieves a synchronized process, changes are guaranteed. Modula’s Fabra says that automation and analysis can support business growth, but that scalability must be baked into the master plan.
“When you start to scale, all systems and procedures must be very clear, integrated and working well,” Fabra says. “We have seen many cases where a manufacturer has couple of automated storage units, grows five-fold and struggles. If you escalate without control, you can lose control.”
Going forward, the manufacturers with the greatest flexibility will be the most successful, Bangalore says.
“The Holy Grail of manufacturing is multi-modal lines, where one line can make just about anything and everything, as opposed to four different lines to make four products,” he adds. “This will be a dramatic transition in investment and thinking to arrive at a point where you can address every variety of your products in one line.”
Companies mentioned in this article
• Beumer
• Cognex
• Dematic
• Intelligrated
• Modula
• Wipro
About the Author
Follow Robotics 24/7 on Linkedin
Article topics
Email Sign Up
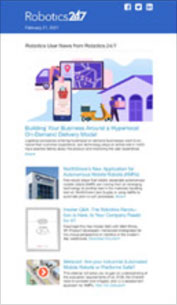