DETROIT—Robotics has come a long way since the introduction of Unimate in 1955. The first industrial robot was designed to perform tasks that were too dangerous or difficult for humans. At Automate 2023 this week, Kawasaki Robotics is displaying how human ingenuity and robots have made a difference in the past, present, and future.
With more than 50 years of experience in the automation industry, Kawasaki said it is a leading supplier of industrial automation and robots, with expertise in a wide range of applications and industries. The Tokyo-based company said it provides a set of standard features on all of its robot models for application flexibility, quality and performance, and customer support and after-sales service.
Kawasaki Robotics, whose U.S. offices are in Wixon, Mich., is exhibiting at Booth 4023 at the Huntington Place Convention Center from May 22 to 25.
Kawasaki Robotics offers a blast from the past
Attendees at Automate 2023 can see a Kawasaki Unimate and Kawasaki J-series robot in person and learn about what was then revolutionary technology and how it came to shape the robots in use today.
Kawasaki Heavy Industries was the first company to sign a technical licensing agreement to start manufacturing the Unimate robot to help address labor shortages—much like today, said Kawasaki.
Launched in 1989, The J-series was part of Kawasaki Robotics general-purpose lineup. This very robot ran for over 26 years, welding everything from the frame sides of a Kawasaki Vulcan 800 motorcycle to steering shafts for all-terrain vehicles (ATVs), the company noted.
The current state of the art is at Automate
Kawasaki Robotics said it has been perfecting its arc-welding lineup to perform accurate and consistent welds. Its systems include features such as touch sensing, advanced weaving, endless positioner rotation function and built in weld data base and standard AS language.
The company is showing its family of new K-positioners for North America, from single-axis and double-axis to multi-positioners. Kawasaki said its robots can now can easily manipulate the position of a workpiece, allowing the welding torch to be positioned at the correct angle and distance and ensuring that the welds are of highest quality and consistency.
The cell featured at Automate includes a Kawasaki BA006L robot that simulates arc welding on a Kawasaki Ninja EX650 mounted on a double-axis PST125-L2 K-positioner.
In addition, Kawasaki Robotics and its partner Capital Industries are demonstrating a valve-inspection system that meets the automotive industry's highest standards of quality, strict acceptance, and performance. The cell features two Kawasaki RS007N robots that will transfer valve bodies between two rotary dials where they will undergo two types of inspection, as well as the handling of accepted and rejected parts.
The first dial was hard-tooled to check the inner and outer diameter of the valves, and the second dial uses a Keyence laser system to detect surface defects on the valves, said Kawasaki.
R-Series and RoboTire offer peeks at the future
To meet the needs of the market, Kawasaki Robotics said it has “continued to optimize its general-purpose robots to to set the benchmark for small-to-medium payload robots” of 3 to 80 kg (6.6 to 176.3 lb.).
The latest addition the the R-Series line, the RS025N, will be on display with the recently released RS007N/L and the RS013N models.
In addition to increased speeds, the RS025N robot includes a new arm structure and compact design, drive system, motor location, and IP67 rating, making it suitable for a wide range of tasks, claimed Kawasaki.
Kawasaki is also partnering with RoboTire, which is bringing tire-changing robots into customer-facing automotive service centers. RoboTire engineers and deploys systems with built-in AI technology to enable faster and safer vehicle servicing than ever before, said the companies.
A technician can control the RoboTire system with the RoboTire mobile app, starting with scanning a vehicle identification number (VIN). RoboTire’s proprietary software pulls in OEM specifications data in near real-time related to the vehicle’s tire and lug nut size and alignment, as well as exact specs for lug nut torque.
All four tires can be changed in 20 minutes using one operator—“Faster for shops. Safer for humans. Safer for Cars,” said the partners.
Editor's note: For more about Automate 2023, visit Robotics 24/7's special coverage page.
Article topics
Email Sign Up
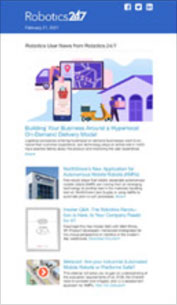
