International TechneGroup Limited (ITI), developers of the CADfixTM CAD geometry translation and repair software, announce a new partnership with Simufact Engineering, part of Hexagon’s Manufacturing Intelligence division, a global operating software company providing process simulation solutions and services to manufacturing industries. The new agreement extends the integration of the CADfix geometry processing technology within Simufact’s manufacturing simulation software.
The latest release of Simufact Additive 2020 sees the integration of CADfix extended to provide a new capability. A new Simufact Additive CAD export feature uses CADfix geometry morphing to adjust the original CAD model according to the distortions predicted by the manufacturing process simulation, and create a distortion compensated CAD model for use in downstream CAD modelling and simulation applications.
The simulation process loop from the original CAD model, through CAD import to the simulation and back to CAD, is frequently open with no capability to export simulation results. This discontinuity in the process chain is now closed with the CADfix geometry morphing and export in Simufact Additive 2020. The original model can now be compensated or distorted by Simufact Additive and then exported to a new CAD file that can be used for further CAM simulations or design work.
The advanced CADfix morphing process generates clean and accurate model geometry that can be exported back to CAD as a usable model, or to other CAE tools for re-meshing and further analysis. The process supports the import of deformation data from various sources and results in the export of a high-quality morphed version of the original CAD model that respects the accuracy, design intent and topological definition of the original design.
“The role of simulation in additive manufacturing is to uncover the most cost-effective way to create parts right-first-time with a design leveraging the full possibilities of the 3D printing process. Simulation allows this to happen outside of the 3D printing machine, saving material and machine time for production,” says Dr. Gabriel Mc Bain, Simufact Engineering, senior director Product Management. “The addition of the CADfix morphing technology in our 2020 release completes a critical link back to CAD and further secures Simufact’s position as the leader in fast and accurate simulation for metal additive manufacturing.”
“Having worked with Simufact for several years providing the CADfix geometry processing technology as part of their manufacturing simulation solutions, we are delighted to be extending our CADfix integration to Simufact Additive,” says Andy Chinn, managing director at ITI’s UK CADfix development office. “CADfix will automatically morph CAD geometry based on the Simufact Additive manufacturing simulation results to create a high-quality deformed CAD model that respects the original design intent, thereby providing a vital link back to CAD within an automated simulation process chain.”
Sources: Press materials received from the company and additional information gleaned from the company’s website.
About the Author
Press releases may be sent to them via [email protected]. Follow Robotics 24/7 on Facebook
Follow Robotics 24/7 on Linkedin
Article topics
Email Sign Up
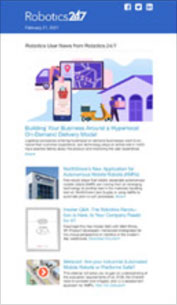
