Optimization and efficiency are key, especially in picking operations.
Dwell time, the time spent by an associate waiting for the next picking mission, is a major nemesis of warehouse management.
An uninterrupted picking workflow reduces downtime and removes bottlenecks that affect all players in a warehouse operation.
Advanced Pallet Station keeps the operation moving
Colorado-based Prime Robotics announced the release of its new Advanced Pallet Station (APS) at MODEX 2024. According to the company, APS represents an advancement in goods-to-person picking systems, utilizing robotics and automation to elevate warehouse productivity and picking accuracy.
“The hardest part is making sure you're keeping the picking station efficient and the picker never runs out of work,” said David Bell, VP of software at Prime Robotics. “Even if that means that the robot shows up right before the picker needs it, that's kind of the magic. We don't want to have robots sitting longer than they need to.”
Long before Prime Robotics started developing this “magic” in conjunction with APS, the company worked in picking automation and saw an opportunity to hone in on this movement, and palletizing with single and multi-SKU picks.
“It became clear that there were a lot more missions with single SKUs required and a lot of missed opportunities to reuse that drive up to the pick station,” said Joe Hunt, COO of Prime Robotics. “If you're picking multiple orders, you could now take that same SKU and apply it to multiple orders. And so that drove us to think, ‘Well, what if I have multiple on the target side as well?’ APS flowed out of customers finding more efficiency and ramping up their picking.”
Prime Robotics’ Legacy Pallet Station (rebranded after Advanced Pallet Station’s debut in early 2024) brought the company into picking optimization, and after identifying the bot queue style and adjusting potential optimization possibilities, APS was born.
“It just became really clear that there was an opportunity to move even faster and to take more advantage of the ability to pre stage work and move it quickly between the source and the targets,” Hunt said.
“It's really about that additional flexibility in picking,” Bell added. “A key part of the APS design is really understanding the customer's order profile. How many cases are they picking? How many items do they have in each order? Then you balance that with something like an APS.”
More customer data is better for optimized picking
When Prime Robotics works with its customers for APS, data is king. Data is key. As Bell put it, “the more data, the better.”
APS performs a WMS level integration with an organization, receiving customer orders from this system. Then, Prime’s WES - called Prime Execution System - utilizes this data and turns it into robot missions.
“What we struggled with initially in APS and we learned the right way to buffer and not over consume the robots,” Hunt said. “It's very easy to have 20 robots serving one station, but it requires a little bit of thought and planning to be able to use a smaller number of robots to keep locations busy.”
Seasonality, peak demand and staff data collected from a customer’s WMS also help Prime optimize the number of robots and picking operations for warehouse staff, allowing them to reduce the dreaded dwell time.
“We have a capability that we call ‘pallet defrag,’ where we look at the positioning of the SKUs within the warehouse and create zones that we try and drive based on how frequently used a SKU is,” Hunt added. “When we first introduced that capability, we were doing it once a day. We quickly found that when you're running 24/7, that's not really helpful. We had to introduce that capability PES so anytime something is leaving a station or being replanned, we take that into account, and we choose the optimal location to keep the SKUs so we can reduce the drive time as much as possible to the APS.”
Robot arm vs. human picker battle rages on
As part of APS, organizations can choose to integrate a robot arm into its picking operations. But, this isn’t always the fastest or most efficient decision.
“The more variability you have in your picking environment, the more difficult it is for the arm to handle,” Bell said. “And it can be very simple things like if you have a mix of arms and humans picking. If somebody puts a case on a source pallet at a weird angle, the human has no problem with it. That may slow the arm down.”
However, despite the enhancements in robot arms and automation, there are some instances where the picks-per-hour isn’t a statistically significant difference.
“Arms are sexy, and arms work really well for things that are hard for humans to do, whether it's an inhospitable environment, or you have to reach high, or you have to lift something heavy,” Hunt added. “But what we haven't seen is the arms completely destroying human pickers from a cases-per-hour perspective.”
Why is that the case? Simply put, the human brain.
“In fact, it depends a lot on the packaging,” Hunt said. “If you have really consistent packaging, the arms can usually outperform the person. But when you have heavy items or lots of variability in what you're picking, we actually often see in the APS that human pickers outperform arms, even though the robots are doing almost exactly the same thing.”
Voice prompts turn, move pallets for simplified picking
Voice prompts also play a major role in APS.
Standard wireless or Bluetooth microphones enable users to keep the picking process moving through standardized prompts such as:
- “Prime, done picking”
- “Prime, spin source”
- “Prime, spin target”
“The technologies for managing voice have advanced quite a bit, and it's a very useful way to create a more conversational interaction with our software that keeps the picker from needing to walk up to the computer or use a mouse or a touchscreen,” Hunt said. “We find it to be very helpful. It gives us probably a 10 to 15% saving just by having voice, because pickers don't have to walk over and press a button.”
Bell agreed.
“Voice is the icing on the cake,” he said. “It makes it easier for the picker… We had an earlier APS design where we actually had buttons that were at each stand so pickers could press a button and move pallets. We found there were more safety concerns with that. Any time you're moving pallets or you're moving goods, anything that’s going to be in that floor space is problematic. Voice is also kind of a safety feature for us.”
Want to learn more about robots picking, packing and packaging? This article was featured in the October 2024 Robotics 24/7 Special Focus Issue titled “Robots picking and packing with precision.”
About the Author
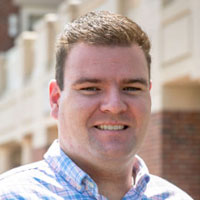
Follow Robotics 24/7 on Linkedin
Article topics
Email Sign Up
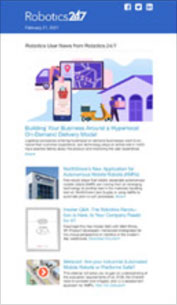