Just a few years ago, autonomous mobile robots (AMRs) were the new kid on the technology block. Only a few vendors were in this space, targeting large distribution centers focused on e-commerce, and one of these vendors (Kiva ) got bought up by the biggest e-commerce player of them all—Amazon.
Today, dozens of vendors offer AMR solutions, and others offer piece-picking robotic arms. There are different AMR approaches, too. Some solutions follow a “goods-to-person” principle in which robots bring mobile shelf units filled with items to a workstations, while other AMRs meet up with human pickers in the aisles to guide them through a set of picks within a relatively dense section of the warehouse. In either case, the goal is to vastly reduce the amount of walking or “travel” that takes up much a warehouse associate’s day.
Going forward, more projects may involve mobile robots bringing goods to collaborative picking arms, thus taking over the picker role to a larger degree. But in many AMR deployments to date, the robots work in combination with human pickers. Yes, AMRs do reduce the labor burden by reducing travel, but given the labor shortage many DCs are struggling with, the focus is centered on leveraging the robotic automation to do away with non-value-added travel, thus making human pickers more productive or available for other tasks.
Analysts see the AMR market as growing rapidly, even faster than the strong growth for fixed types of warehouse automation. According to a study by LogisticsIQ, the AMR market stood at about $650 million in revenue in 2018, but will grow nearly tenfold by 2025 to reach $6.8 billion in sales. That’s a compound annual growth rate (CAGR) of 37% through to 2025, driven largely by the need to bring greater efficiency, speed and accuracy to e-commerce fulfillment, according to Avi Gupta, an industry analyst with LogisticsIQ.
“The main driver of rapid growth for AMRs is e-commerce, which is growing very rapidly,” says Gupta. “With e-commerce today, there’s more focus on same-day delivery, as well as online ordering of groceries, which is going to further drive up the need for automation. Generally, companies are interested in using AMRs because they need to reduce the cost of order picking, and make order fulfillment more accurate to reduce the rate of consumer returns.”
Bots as helpers
For companies deploying AMRs in DCs, robotics is often seen as a way to make the human labor you can secure more productive, rather than try to run a fully automated DC. That makes mobile robots more like co-workers than gear that is going to “automate” associates out of jobs.
This has been the experience at Lockheed Martin Corporation, where its use of AMRs has forged a tight working relationship between the workers and the robots. The warehouse associates even have names for the bots, who they see as helpers rather than competition.
The monikers for the robots include Louie, Amy, Keoki and Little Joe. They draw on the names of key leaders who helped bring the robotics deployment about within Lockheed Martin’s Rotary and Mission Systems group, says Corey A. Cook, senior program manager and solution architect for Lockheed Martin.
The nicknames also highlight the level of bonding between the workers and the robots, who lead the warehouse associates through order picking tasks in a way that lessens their travel time and increases their productivity. Worker buy-in for the deployment was something the project aimed for from the start.
“It was very important to us that we had acceptance by our workforce for the robotics solution,” says Cook. “One of the main areas of feedback we’ve heard from them is that the robots take a lot of stress off their job tasks. We’ve been about a year into this deployment, and as part of our review of how things were going, we asked the workers, ‘what do you think?’ and to a person they said, ‘I cannot work without them [the robots]. They make my life so much easier.’”
Bethesda, Md.-based Lockheed Martin is a global security and aerospace company. Its Rotary and Mission Systems group provides consumables and spare parts to the U.S. Air Force under what is known as an Industrial Product-Support Vendor or “IPV” program. The AMR solution from 6 River Systems was deployed to support the fulfillment operations for this program, at a distribution center in Oklahoma City, Okla., that ships parts to various Air Force maintenance facilities.
The DC went live with eight mobile robots, replacing a process in which associates picked parts to a cart using a pick list generated by Lockheed Martin’s customized warehouse management system (WMS). While not a large-scale AMR deployment, since going live in early 2019, the solution has generated strong return on investment (ROI) metrics and attracted interest within Lockheed Martin for broader AMR use.
Perhaps most impressive, the AMR deployment is credited with up to a 381% increase in lines per hour (LPH) picked, and overall ROI for the system was achieved in nine months. According to Cook, the big jump in LPH comes from a combination of factors, including much less travel by warehouse associates, as well as on-screen directives from the robots. These instructions show the worker what to pick next and in what quantity. With close to 100,000 stock keeping units (SKU) in the Oklahoma City DC, the ability of the robots to accurately lead associates through efficient pick paths and present visual cues for order selection were keys to driving up LPH.
“The main benefits come from how the robotic platform and its software are able to lead the worker effortlessly to the correct location in the most efficient manner,” says Cook. “Then, the robots show where parts are on a shelf, the exact amount needed, and prompt the worker through the pick and verification process. All those things tied together have added a tremendous degree of efficiency.”
Integrated to WMS
AMR solutions are systems rather than commodity equipment. Many mobile bots may look similar, but they often vary in the workflow methodologies they support, in attachments and payloads they are designed to work with, as well as in software capabilities. With 6 River Systems’ solution, the robots, which are referred to as “Chucks” by the vendor, support a directed workflow approach in which the bots work alongside human pickers, leading them through the picks along an optimized path, giving them instructions, and transporting completed pick containers to the next point in the fulfillment process, eliminating long-range cart transport. Once a worker is done filling up one Chuck, another one shows up nearby with a fresh set of work to complete.
To make this process effective, the 6 River platform needed to integrate with Lockheed Martin’s WMS, which Cook says was relatively easy to set up using application programing interfaces. This integration allows the robotic software platform to dynamically decide on the best pick paths, and comply with Lockheed Martin’s inventory rules, which can be complex.
For example, says Cook, under the IPV program, some inventory is owned by the program, and some is owned by the Air Force, so the robotic solution needs to abide by these ownership rules while still coming up with efficient pick paths. With the integration in place, Cook adds, warehouse workers don’t have to worry about whether picks are happening at the correct location.
The full deployment took three months, including integration to the WMS and adjustment of some warehouse picking procedures and minor material flow details. Cook says the deployment team wanted to take the time to do things like reduce duplicative SKU locations and adjust a few material flow factors like some of the receiving points.
“We definitely wanted to leverage 6 River Systems’ expertise in terms of them suggesting some best-in-class ideas about material flow,” says Cook. “And, because the system is line-item driven, you need to be very in tune about having effective warehouse procedures. The deployment really forced us to look at those under a microscope and see what made sense.”
The Chucks support a directed workflow approach where the bots work alongside human pickers, leading them through the picks along an optimized path, giving them instructions, and transporting completed pick containers to the next point in the fulfillment process.
With warehouse procedures fine-tuned, and the WMS integrated with the Chucks, the directed workflow itself is fast and accurate, reports Cook. Duplicative locations for the same SKUs have been reduced, and workers can trust the robots to lead them through picks and verification steps with minimal movement. “The way the robotic solution is designed, it’s a fluid motion for the workers,” he says. “They’re able to see instructions, pick the part in the right quantity, verify the pick, and place the item or items in the right location in the container, using a light-up feature that shows them where to place it. The worker doesn’t have to pause to think through each step—and that’s the key to the speed and accuracy of this system.”
In terms of service levels, the faster, accurate picking has decreased warehouse cycle times from what could be as long as 70 hours for some orders to no orders taking longer than 20 hours from order placement to departure from the DC. That cycle time may seem long compared to some DCs focused on consumer goods, but given the many specialty piece parts and non-standard inventory ownership rules the Lockheed Martin DC deals with, the improvement in cycle time is significant. “We’ve seen a tremendous improvement in turnaround time and that has certainly made the customer happy,” Cook says.
Gaining worker buy-in
To ensure the warehouse workers would be on board with the robotics choice early on, the project leaders brought warehouse associates into the selection process. The frontline workers reviewed the AMR options the team had identified as having potential and agreed the 6 River Systems solution seemed to be a good choice.
They particularly liked the fact that it was a collaborative robotic or “co-bot” approach that centers on accelerating workflows for human workers. “The co-botting approach was clear to everyone,” says Cook. “We were able to show that the system was going to make them perform better.”
The mobile robots have integrated flat screens with a streamlined user interface to guide workers through picks and verification steps. Cook says it took about 10 minutes for him to learn the basics of interacting with the system. Full training for warehouse associates is a bit more involved, but still something that can be mastered in a few hours, as opposed to learning paper-based procedures or complicated navigation menus on wireless devices.
Another key benefit of the system is that it generates detailed analytics about warehouse picking processes and inventory levels and movements. The Oklahoma City DC uses this data for various purposes, from metrics visibility for supervisors, to fine-tuning inventory positions, and knowing which workers are performing above average. By comparison to largely manual order picking processes where data collection can be overlooked or very basic, a mobile robotics platform is constantly generating data about what the robots did, what orders or materials they helped pick or transport, pick paths and cycle times, and which warehouse associates were working alongside them.
In the case of the 6 River Systems robots in use at the Oklahoma City DC, the system-generated data supports “gamification” of picker performance, so that managers and front-line workers can see how they are doing against average performance rates. “It’s a way of highlighting who your best performers are,” says Cook. “The managers can see, ‘yes, this person is performing at a level well above par.’”
Long term, says Cook, his hope is that broad-based use of AMRs will help warehouse processes keep pace with the trend toward predictive maintenance in aviation. Within the latest aircraft, sophisticated sensors are permitting aircraft systems to predict when issues are about to arise and trigger orders for parts. If warehouses are stuck with only semi-automated or paper-based processes in this era of predictive maintenance, it’s going to be much harder to react quickly to requests compared with having an AMR platform that generates real-time data on fulfillment activity.
Call it Industry 4.0, or a digital loop between smart aircraft and smart spares fulfillment, but Cook sees robotics as being able to facilitate actions like instant stakeholder knowledge of when replacement parts have been picked, packed and shipped. “My vision is to meld the two worlds together—predictive maintenance and sensors in aviation, and sensor-based robotics processes in the warehouse,” says Cook. “I see that as being the future, not just for fulfillment centers in the aviation industry, but in almost any industry.”
The success of the AMR deployment in Oklahoma has Lockheed Martin considering broader use of AMRs, says Cook, but plans for further use haven’t been finalized. Other groups within the enterprise also are examining the success of the robots in this early test, and evaluating ways to use mobile robots for other logistics efficiencies.
To get the most out of AMRs, Cook believes it makes sense to work with the vendor to fine-tune warehouse procedures before the robotics goes live, thus maximizing the ability of the AMR platform to select optimal paths to match incoming orders. He also recommends that when evaluating AMRs, it’s worth the effort to obtain buy-in from some of the warehouse associates who will be working hands-on with the robots. “For us, it was good knowing from the very beginning that they were part of the program ownership process and it was their choice, too. They were the ones that would have to work with it 24/7, so it made sense to bring them into the process.”
About the Author
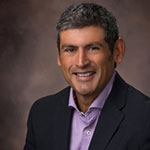
Follow Robotics 24/7 on Linkedin
About the Author
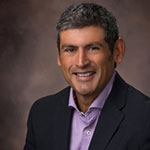
Follow Robotics 24/7 on Linkedin
Article topics
Email Sign Up
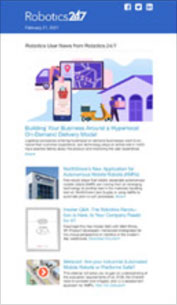
