Constructing and then launching large structures (like telescopes or space stations) into orbit is an expensive process. California-based Made In Space hopes to reduce the time and cost associated with building space structures by using 3D printers to assemble the objects in space instead of on Earth.
In August, the company announced that its 3D printer created multiple polymer-alloy objects over 24 days inside a thermal vacuum chamber (TVAC) at the NASA Ames Research Center in June. According to the company, this was the first time a 3D printer had built extended structures (the largest was a 33.5-in. beam) in space-like conditions.
“This is an important milestone, because it means that we can now adaptively and on demand manufacture things in space,” said Made In Space CEO Andrew Rush. “We have significantly de-risked that technology.”
The 3D printer is part of the company’s Archinaut solution, a robotic system that Made In Space is creating as part of a NASA contract. The complete system will include robotic arms that will assemble printed parts.
While the June test was conducted under Earth’s gravity, the company has demonstrated zero-gravity printing. Made In Space built two 3D printers that are now aboard the International Space Station.
By printing and assembling structures in space, it is conceivable that the solution could be used to build items that are currently too large to launch on a rocket. For example, NASA hopes to construct very large telescopes that are currently too big to efficiently launch using existing transports.
“We do believe that in-space robotic manufacturing and assembly is going to revolutionize the way we design and deploy and operate systems in space,” Steve Jurczyk, the head of NASA’s Space Technology Mission Directorate, said at a press conference announcing the tests.
According to Made In Space, the final Archinaut system could be operational by the mid 2020s.
Source: Scientific American
About the Author
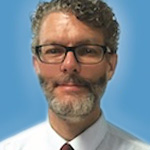
Follow Robotics 24/7 on Linkedin
Article topics
Email Sign Up
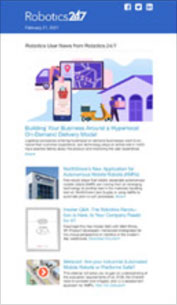
