Retail store fulfillment typically requires the shipment of full cases and pallets of like SKUs, but e-commerce orders are made up of an ever-changing combination of SKUs in small quantities and headed to different locations. This has driven up demand for labor, which has never been scarcer, according to InVia Robotics Inc. The company today announced that Fulfyld, a third-party logistics provider or 3PL, has chosen it to integrate robots and a full warehouse execution system into Fulfyld's facility in Harvest, Ala.
inVia plans to integrate its robotics-as-a-service (RaaS) suite into Fulfyld's existing warehouse to address the challenge of random access to inventory for e-commerce fulfillment. The Westlake Village, Calif.-based company said it will deploy autonomous mobile robots (AMRs) and software “without disruption to daily operations.”
“inVia’s RaaS model is ideal for e-commerce fulfillment 3PLs like ours, because it allows us to avoid large CapEx [capital expenditures], which ultimately helps Fulfyld deliver better pricing to customers,” stated AJ Khanijow, CEO of Fulfyld.
Fulfyld finds efficiencies
“We’ve specifically designed our system to increase productivity in e-commerce operations where more labor is required to ship directly to consumers,” said Lior Elazary, co-founder and CEO of inVia Robotics. “As consumer demands for next- or same-day delivery increase and labor supplies decrease, we’re able to help 3PLs keep up and meet their SLAs [service-level agreements].”
The system will include:
-
inVia PickerWall system including a fleet of inVia Picker AMRs
inVia Logic, the AI-powered warehouse execution system (WES) software
inVia’s Robotics Operation Center (ROC) for 24/7 monitoring and support
inVia said its Picker robots will do all of the nonstop traveling to retrieve each day’s ordered SKUs and deliver them to its dynamic put and pick wall where people pick individual items.
“It also extends our operations resources, not only by supplementing our workforce with robots, but also by finding greater efficiencies in our workflows so our teams can work smarter,” said Spencer Mundt, chief operating officer of Fulfyld. “We looked at all of the automation solutions on the market, and only inVia delivered the level of flexibility and productivity increases we needed for the level of service we’re committed to giving our customers.”
inVia explains deplopyment process
Elazary answered the following questions from Robotics 24/7:
Did Fulfyld test inVia’s products prior to rolling them out in its Harvest, Ala., warehouse?
Elazary: With all of our customer deployments, we first build a simulation of their facility and operations so we can test order fulfillment before we begin the physical deployment of the system. This allows us to confirm assumptions, or in some cases identify workflow modifications that ensure the system is delivering on the SLAs we’re aligned with and that orders will flow through the system unimpeded.
Operating it in this simulated environment accelerates the deployment process, because once we get to “go live,” it has already been tested to make sure it works.
How long do you expect the integration to take?
Elazary: We expect this particular integration to take about six to eight weeks. We expect Fulfyld to be using the system as part of their daily operations in June.
How will Fulfyld bring in inVia’s PickerWall, Logic, and ROC “without disruptions in daily operations”?
Elazary: It’s always been key for our customers to bring automation into their operations while ensuring their daily operations are kept intact. One of the reasons they’re adopting automation is that they’re barely able to keep up with e-commerce demand with their existing operations and workforce. So, the last thing we want to do is slow them down.
We’ve carefully built a deployment process that allows us to build the system in parallel to existing operations. On the physical side, we are able to build the inVia PickerWall without disturbing any of the existing picking zones. We also move inventory in discrete segments in order to minimize movements of goods that are currently being fulfilled.
On the software side, we integrate inVia Logic with the WMS [warehouse management system] and set up all of the new workflows in a staging environment where we test every element of the system before switching over to it for live production.
The ROC starts 24/7 monitoring and support throughout the testing phase and build-out process. So, once the system goes live our robotics experts already know the facility and workflows well.
What sort of e-commerce orders will be fulfilled – consumer packaged goods, pharmaceuticals, apparel, etc.?
Elazary: Fulfyld’s industries span baby products, books, CBD and supplements, clothing and apparel, health and beauty, home goods and improvement, outdoor equipment, and toys and games. They also fulfill subscription boxes within select industries.
Does inVia Logic replace or supplement existing Fulfyld WES?
Elazary: Fulfyld does not have an existing WES, so inVia Logic will integrate directly with their WMS and deliver immediate improvements. Logic is able to take the inventory management function of the WMS a couple of steps further. It optimizes the location of inventory specifically for e-commerce, which necessitates random access to a wide variety of SKUs.
Then it calculates the most efficient paths using inVia SmartPath to take to retrieve all of those SKUs that have to be placed in a way that they can be randomly accessed.
So, combining the functionality of their WMS with inVia’s WES delivers an integrated system optimized for Fulfyld's business. On average, inVia’s customers see a 4X to 5X increase in pick rates with optimal inventory placement, and people walking only inches between picks versus miles.
How many inVia Picker AMRs and staffers will be involved in this deployment?
Elazary: The initial deployment at Fulfyld will include 15 to 18 inVia Picker robots. They will be the backbone of a comprehensive automation system that delivers 150 actions per hour (APH).
The system will be used to both pick orders and replenish stock, so each action could be a movement of goods in or goods out.
Why did Fulfyld choose a RaaS model? Did it evaluate other automation or non-robotic alternatives?
Elazary: inVia’s RaaS model was most appealing for Fulfyld, as they operate through finite contracts with their customers. Using a RaaS model allows them the flexibility to integrate new automation solutions without high CapEx that can’t be justified over the short lifetime of their 3PL end-user contracts. Fulfyld was attracted to this model specifically because it allows them to keep their pricing competitive.
Fulfyld looked at all the automation options on the market. They found that many of the person-to-goods AMRs did not give them the needed productivity to deliver the ROI [return on investment] they needed in a 3PL business.
They found that ASRSes [automated storage and retrieval systems] delivered higher productivity than the person-to-goods AMRs, but the cost was too high. Given they’re operating under contracts of about three years’ duration with their end customers, they couldn’t justify amortizing the cost of a capital-intensive system over several years longer than that.
inVia hit the sweet spot for them—the highest productivity rates and at an affordable cost.
Does the company plan to add inVia robots, PickerWall, and software to other facilities?
Elazary: Fulfyld operates one facility today. There are have plans to expand into additional facilities given the growth of their sales, and those expansion plans include replicating the inVia automation model given productivity metrics are met in the Harvest facility.
About the Author
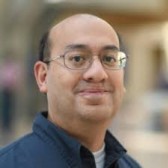
Follow Robotics 24/7 on Linkedin
Article topics
Email Sign Up
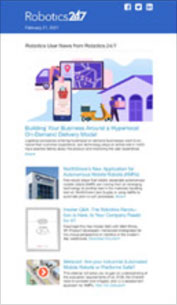
