MSC Simufact introduces Forming Version 16, a simulation and analysis software suite for modeling complex manufacturing machines and forming processes. Rewritten throughout for increased efficiency and ease of use, Forming Version 16 also offers various new features and enhancements for building robust simulation models.
The new geometry data check feature allows users to identify simulation error as well as check their position within the geometry. This new model data can be sent back to the CAD model, allowing retracing of corrections. The user then reimports the optimized tool geometry and continues setting up the model.
3D features have been updated to allow symmetry properties to extend model visualization up to 360 degrees, using mirror and axial symmetry features regardless of their position in space. MSC Simufact says this extended visualization provides a comprehensive understanding of results, enabling a deeper review of processes. Related to this is the extended scope of post particles, location markers that act as virtual sensors to deliver measurements of deformable dies and 2D simulations.
Forming Version 16 uses practice-oriented 3D visualization, which produces a view of processes and properties in a fast and effective fashion while reducing calculation time. This feature is based on the calculation of selected workpiece segments and leveraging their symmetry properties. Workpiece segments are adjustable at every forming stage.
Forming Version 16 offers a Best-Fit method to compare the simulation and reference models. Simufact describes this as a one-click method that evaluates if tolerances will be met. The software automatically determines the position with the highest deviation and highlights it for review. MSC Simufact incorporated 3DReshaper technology from its parent company Hexagon to create this new feature. Additionally, this update offers cut outline functionality to directly compare simulated geometry with target geometry, which can be exported into CAD.
Version 16 offers one-click import of model data from Simufact Welding and Simufact Additive. For example, users can import two previously welded components from Simufact Welding into Forming and continue modeling a forming process. The company says this method offers minimal effort to achieve a consistent process chain simulation. Users can exchange or transfer data between different Simufact Forming processes. Users can import selected processes with all process properties intact, and use them for subsequent calculations.
Version 16 also provides enhanced flexibility, allowing ability to share results with any CAE product. Exported simulation results can be used in other products, such as software for fatigue simulation. When importing data, Simufact Forming Version 16 interprets the different variants of UNV files, unless they conform to the UNV standard or contain custom result types. Users can also export results adapted to the target software.
MSC Simufact says this update to Forming enhances data management performance by implementing an archive manager. This allows users to reduce the data from large projects, reducing archiving costs. The resulting steps can be used in forming stage transitions, which can also be retained and archived.
MSC Simufact Forming is the centerpiece of a suite of related modules that include add-on modules for specific processes including various cold forming, rolling and other production methods. There are also services in the suite for importing dies and pre-form geometries from CAD files, material data sets and for parallelization of simulation for increased solver speed.
For more information on MSC Simufact Forming Version 16, click here.
Here are some short videos highlighting features of Forming Version 16.
See why DE’s Editors selected MSC Simufact Forming Version 16 as their Pick of the Week.
Sources: Press materials received from the company and additional information gleaned from the company’s website.
About the Author
Press releases may be sent to them via [email protected]. Follow Robotics 24/7 on Facebook
Follow Robotics 24/7 on Linkedin
Article topics
Email Sign Up
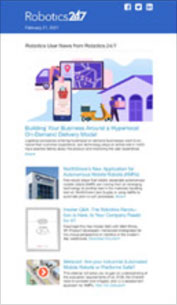
