Self-driving yard trucks must be able to reverse into trailers to fully automate operations, according to ASI Logistics. It and SICK Inc. yesterday announced that they have solved the problem of reversing into trailers autonomously.
A few technical details must be known for autonomous trucks to correctly reverse into trailers, said Autonomous Solutions Inc. (ASI). A self-driving truck must know the position and height of the trailer’s “kingpin” it is reversing into, it explained.
The kingpin is the mechanism under the trailer that connects to the truck’s fifth wheel and locks the trailer to the truck, ASI added. The truck must be able to detect the kingpin connection so it can reverse autonomously into trailers, said the Shanghai, China-based company.
ASI said it serves clients around the world in logistics, mining, agriculture, automotive, government, and manufacturing industries. The company provides remote control, teleoperation, and fully automated industrial vehicles and tests them at its 100-acre proving ground in northern Utah.
ASI Logistics uses lidar, VAK to back up trucks
ASI Logistics said it used its “robust” and “state-of-the-art” Vehicle Automation Kit (VAK) and SICK’s lidar sensors to overcome this challenge.
Inside the VAK is the truck’s Vehicle Control Unit (VCU). The VCU commands all the truck’s functions when the truck is in autonomous mode. The VCU relies on quality data transmitted from sensors to autonomously reverse into trailers, said ASI.
The company used two SICK lidars—the LMS1000 for kingpin position, and the TiM551 for kingpin height.
As a truck reverses, the two lidars detect the trailer’s kingpin and relay its location to the truck’s VCU. The VCU then commands the throttle, brakes, steering, and fifth wheel to continue to reverse safely into the trailer until a secure and safe connection to the kingpin is made.
Sensors indicate whether the truck has a secure connection and if it is ready for the robotic arm to attach the necessary glad-hands and continue with the rest of the move.
ASI said its Mobius software is necessary to completing the process. It claimed that Mobius is “the most advanced command and control software for autonomous vehicles in the world and is backed with over 20 years of industry experience and has millions of data testing hours behind it.”
The company said Mobius can show real-time vehicle movement, vehicle state, kingpin alerts, and robotic arm control to users who can be on-site or anywhere in the world. “Mobius, combined with SICK’s lidars, offer huge potential to continuously deliver the most advanced autonomous yard truck solutions in the world,” said ASI.
SICK senses for safety
“SICK recognizes that better autonomous vehicles are only possible with better sensing technologies,” said Aaron Rothmeyer, a product manager at SICK. “As such, SICK is continually innovating its product portfolio to take advantage of the latest tools and ideas.”
“Their substantial experience with optical devices shows up in well-designed sensors all the way down to the component level,” he noted. “In addition, SICK is also heavily involved in the creation and updating of global safety standards, which is a critical step to ensuring autonomous vehicles’ continued success.”
Founded in 1946, SICK said it is a leading manufacturer of sensors, safety systems, machine vision, emissions monitoring systems, flow measurement, encoders, and automatic identification products for industrial applications. The company supports logistics, automotive, packaging, electronics, food and beverage, material handling, and process automation markets.
SICK said its sensors “create the perfect basis for controlling processes securely and efficiently, protecting individuals from accidents, and preventing damage to the environment.” The company added that they deliver quality data even when conditions aren't ideal.
Lidar (light detection and ranging) sensors target objects with a laser and measure the time that passes until the reflected light returns to the receiver. SICK said these lidars can generate a 3D or 2D image with spatial and depth data for detecting, measuring, localizing, and tracking objects.
Sensors from SICK are installed in robot arms, manned forklifts, and yard trucks to simplify and optimize handling, transport, loading and unloading, and material storage.
SICK added that it has more than 3,500 patents and diverse products for every phase of production. The Waldkirck, Germany-based company has operations or representation in 65 countries, including U.S. offices in Minneapolis.
Article topics
Email Sign Up
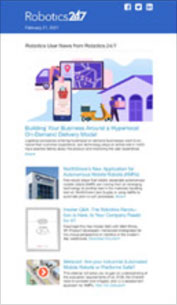
