The manufacture of cutting tools requires precision and repeatability, ideal qualities for robotics. ANCA Inc. is offering modular workcells and a recipe-based approach to address industry demand and augment the skills of scarce workers.
Founded in 1974, ANCA is a leading manufacturer of CNC grinding machines. The Melbourne, Australia-based company said its CNC grinders are used in making precision cutting tools and components across industries, including automotive, aerospace, electronics, and medical.
“The founders are still working with the company,” noted Jan Irzyk, product manager at ANCA. “We've grown to an international business, with offices in the U.S., the U.K., Germany, Thailand, China, India, Japan, and Brazil.”
ANCA addresses industry pain points
The ANCA Integrated Manufacturing System (AIMS) is designed to connect sequential processses in tool manufacturing. The company noted that over 70% of its customers are seeking machines with robotic functionality.
“In the past few years, we recognized the need in the market for automating manufacture of these tools,” Irzyk told Robotics 24/7. “It starts with recognizing customer pain points and trends in the market early.”
“First and foremost are labor pressures—wages are accelerating upward in Europe, competition is increasing, and access to skilled operators is limited,” he noted. “While manufacturers need a three-shift schedule, retention is a challenge. They also want hard data to maintain consistency and high quality in competitive markets.”
AIMS offers modular manufacturing
“We started AIMS two years ago with the idea of materials transfer, and then it grew to include more processes beyond grinding,” said Irzyk. “AIMS addresses the ecosystem with the same volume of production and less reliance on skilled labor.”
AIMS offers functionality that can be adapted to each factory’s needs—from smaller-scale, data-based options to a full setup across a series of machines, said ANCA. The system enables the transfer of tools between operations with the AutoFetch autonomous mobile robot (AMR), handles blanks in and out of CNC machines with AutoLine, and automates tool measurement and process compensation using AutoComp.
“There's a safety aspect with AMRs,” Irzyk added. “With less interaction with moving parts and fewer heavy loads, AutoFetch can reduce fatigue from lifting, which is good for both employers and employees. We want to make the modern factory the employer of choice—it's all in the perception of the business.”
“Because AIMS is flexible, modular, and scalable, we can start with a single workcell and go up to multi-machine deployments,” Irzyk claimed. “Most ANCA equipment is AIMS-ready, such as the RoboMate 2.0 with the MX and AutoLine Advanced.”
Around IMTS last year, ANCA launched its MX7 ULTRA machine, which featured 1 nm axis resolution and 0.002 mm line-form accuracy, which the company claimed was the highest accuracy on the market.
“With a loader plus grinding machine, it's ready for a fully automatic environment,” said Irzyk. “We integrate certain processes such as tool grinding step by step, adding things like blank and edge preparation and tool washing. We also encourage integration with third-party processes and machines.”
Tools to enable data-driven decisions
AIMS also includes the AutoSet hub for managing data and providing it to operators, Irzyk explained. In addition, the AIMS Server manages data flows between the elements of the AIMS system and enterprise IT platforms.
“AIMS ensures quality and maximizes uptime with quicker response to market,” said Irzyk. “This enables better data-driven decisions.”
“At the end of bench grinding, we get information on tolerances on individual tools and whole batches,” he added. “This is important for the customers of our customers, like in aerospace, which requires detailed reporting on the tools they receive.”
ANCA is working on tools for overall equipment effectiveness (OEE) measurement, and it is interested in using machine learning for smart insights and dynamic allocation of jobs, Irzyk said. How does AIMS handle complexity in multi-process cells?
“Part of the AIMS Server creates a recipe for each SKU or tool type and a sequence of processes to be executed by the cell,” Irzyk said. “The process definition resides in every piece of equipment, and the server orchestrates them in order of execution.”
Holistic approach a differentiator
How does ANCA AIMS compare with other automation?
“This is much more holistic,” Irzyk replied. “While the automation of material transfer is commonly seen in our industry, we are one of the pioneers in integrated system to the market. We're one of the companies that introduced the modem to CNC machines, and we have extreme innovation experience in our DNA.”
“What's different in ANCA's case is our ability to integrate with local MES [manufacturing execution systems] and ERP [enterprise resource planning] systems,” he added. “It's important to be able to automatically measure and compensate individual tools while grinding—it's a unique value proposition.”
“We're driven by recipe, server, and AutoComp to reduce manual interventions,” said Irzyk. “Operators are still needed to set up and oversee the cells and manage errors or reset machines. The average ratio of machines to operators is 3:5, and with AIMS, the ratio becomes nine to 12 machines per operator. They don't need to be present 24/7, as the factory mostly operates itself.”
ANCA to offer open house
ANCA has an innovation hub in Melbourne, and it is building centers around the world for large and small customers to see how to grind their own tools.
During its Technology Days on May 9 and 10, ANCA plans to offer visitors an opportunity to visit its facility in Wixon, Mich. They will be able to see its nanometer grinding technology and live demonstrations of its other systems for cutting tool production.
“It's important for engineers to touch the tools,” Irzyk said. “The time for automation is not in the future—it's here and now. We're excited to bring that to market.”
About the Author
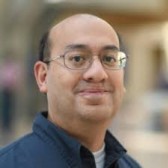
Follow Robotics 24/7 on Linkedin
Article topics
Email Sign Up
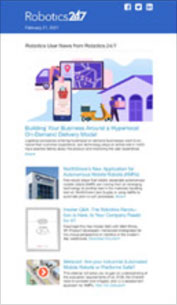
