America Makes announces that Gold-level member, Rapid Prototype + Manufacturing LLC. (rp+m), has delivered a comprehensive ULTEM 9085 Type I Database for Fused Deposition Modeling (FDM) Additive Manufacturing (AM) to America Makes and its membership community to further the use of the Type I certified material for aircraft interior components.
“The qualification of the ULTEM 9085 material and the establishment of the material properties database by the rp+m-led team are huge steps forward for AM, particularly within the aerospace and defense industries,” says America Makes Executive Director Rob Gorham. “On behalf of all of us at America Makes, I want to commend rp+m and its team for enabling the broad dissemination of the collective knowledge of ULTEM 9085 for the innovation of future part design. The ability to use AM to produce parts with repeatable characteristics and consistent quality for certifiable manufacturing is a key factor to the increased adoption of AM within the multi-billion dollar aircraft interior parts segment.”
The ULTEM 9085 Database features mechanical and physical properties, as well as processing parameters, in a compatible and accessible form available to the membership community via America Makes Digital Storefront. It was a deliverable from an America Makes applied research and development (R&D) project, ‘High-Performance Additive Manufactured Thermoplastics,’ led by rp+m, a founding member of America Makes, in conjunction with Stratasys Inc., Wichita State University — National Institute for Aviation Research (NIAR) and the National Center for Advanced Material Performance (NCAMP), and Lockheed Martin Missile and Fire Control, with NIAR research funding from the Federal Aviation Administration (FAA).
“The significance of this project for the aerospace industry is tremendous,” says Tracy L. Albers, Ph.D., president and CTO, rp+m. “Our open collaboration with the FAA-funded effort to develop a framework for advanced polymer-based additively manufactured materials, in this case, ULTEM 9085, into the NCAMP process was incredibly successful. The project examined an extensive and comprehensive set of machine process controls to understand and measure variability. It yielded the creation of the first, public database of its kind to enable the widespread use of additive technologies in the production of aircraft interiors. Now, aerospace engineers have a baseline understanding of how to design for AM and specify AM as an actual manufacturing tool, as well as the assurance that the first AM part and the last AM part are indistinguishable.”
Additionally, ULTEM 9085 resin is said to be the first additively manufactured material tested under the National Center for Advanced Material Performance (NCAMP) process, according to America Makes. It is pending official approval from the NCAMP.
The foundation for this project was a focused effort by Stratasys to answer manufacturing customer needs for low variability and documented process control. The resulting hardware and software enhancements to the Fortus 900mc printer, Stratasys Certification Grade Filament and validated process control documentation enable users to produce high-performance, low-variability printed parts. This level of control was required for a polymer AM system to reach the level of maturity necessary to execute an NCAMP qualification process successfully. The configuration leveraged to generate the ULTEM 9085 database is now offered commercially by Stratasys as the F900 Aircraft Interior Solution (AIS).
Now that a process exists for NCAMP that can approve any non-metallic AM material, the CMH-17 organization recently announced that it would be creating a new volume of its Composites Material Handbook, often referred to by the industry as CMH-17. The new volume will specifically focus on non-metallic AM and cover material data, as well as guidelines on how to generate and use the data based on best practices and proven methods. The B-basis allowables for ULTEM 9085 developed from this project will be the first data set to be submitted for publication consideration.
In addition, due to the interest in the ULTEM 9085 resin, SAE International has created a non-metallic AM committee. The first two specifications will be the material and process specifications for ULTEM 9085 resin based on the NCAMP process developed by this project.
ULTEM 9085 resin is a polyetherimide high-performance thermoplastic material with a high strength-to-weight ratio and flame, smoke, and toxicity (FST) rating. This material is often used in aerospace, automotive, and other industrial applications where a high-strength thermoplastic material is needed. As ULTEM 9085 resin is one of the only high-performance thermoplastic materials available for FDM, it was important to establish a complete database of material properties to further enable use in various commercial and government applications.
About the Author
Press releases may be sent to them via [email protected]. Follow Robotics 24/7 on Facebook
Follow Robotics 24/7 on Linkedin
Article topics
Email Sign Up
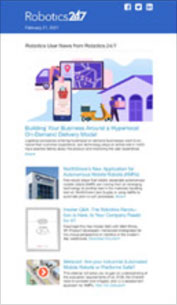