Last week in Long Beach, California, aerospace and defense manufacturers, suppliers, and consultants marched into the downtown convention center for the annual AeroDef Conference, produced by the Society of Manufacturing Engineers (SME).
“I'm a competitor. I look out in the audience and I see my competitors, suppliers, and customers,” said Kevin Smith, sector VP of Global Operations, Northrop Grumman Aerospace Systems, as he began his keynote talk.
“But there are a couple of things I won't compete on .. [ That's ] any type of safety products. [If there's] something I can do to help my industry friends be successful in the area of safety, I don't want to compete in that area. I'd share my capability and collaborate with you,” he added.
Collaboration in the era of shifting political alliances
A global defense technology supplier with U.S. $30 billion in revenues, Northrop Grumman is a powerhouse in the aerodef industry. Exhibitors would do whatever it could to get a meeting with Smith or one of his colleagues, to be on Northrop Grumman's short list for the next purchasing season.
“Our footprint was at one time primarily domestic. But now, it's across the globe,” Smith said. For him, one of the challenges is the ever-shifting international governmental alliances. “One day, a government is our ally. The next day, it may not be. So our risk proposition changes everyday,” he noted. “When that happens, it puts a significant strain on us because we need to collaborate with other countries to develop new products.”
The multi-tier structure in aerodef manufacturing also creates concerns for tier 1 firms such as Northrop Grumman. “As we go down the lower tiers, there's less and less visibility,” Smith said. “So it creates a risk for us. What are they putting in my product? Do they have traceability for the materials? Do they know where that transistor came from? Did it come from a source authorized for the U.S.?”
Safety, security, and digital twins
In a featured panel discussion, experts tackled the issue of cyberphysical security in additive manufacturing (AM). “Someone can affect the quality of a part just by changing the material properties or the power supply [to the AM system],” noted Mark Yampolskiy, assistant professor, School of Computing, University of South Alabama.
The recent crash that grounded the Boeing 737 Max casted shadows over the convention center's deck and hallways. Attendees and panelists referred to it directly and indirectly, often as a prelude to talks about cost savings vs. safety.
“That whole [Boeing 737 Max] fleet is now grounded, costing Boeing millions of dollars, whereas a few thousands of dollars could have prevented this,” remarked Nick Bullen, technical fellow for Advanced Automation and Global Manufacturing, Northrop Grumman Corporation, as he moderated the panel on cyberphysical security.
According to a JPMorgan Chase analyst cited by Forbes, “For each month the Max is idled, Boeing faces estimated losses of $1.5 billion to $2.7 billion” (”Boeing Races Ahead With 737 Max Output as Financial Risk Deepens,” April 2019).
Bridging eBOM and mBOM
During the Q&A, one attendee wondered if creating a digital twin of a product and opening it up for public testing might have helped uncover the 737 Max's fatal flaws—crowd-sourced testing, if you will.
But such a model with all the characteristics of the physical counterpart will be a treasure trove for IP thefts. Some may argue a publicly accessible digital twin is in itself a security risk, as a thorough analysis of the digital twin exposes all of the vulnerabilities of the physical product, be it a plane or a factory.
“It's a game changer when you merge AI and digital twins,” said Chris Lennon, chief technologist & industry lead for aerospace and defense, DXC Technology. “The biggest hurdle is data, in my opinion. In aerospace and automotive, you've got many versions of the truth—different variations of the design. How do you get to the one version you need to analyze?
Lennon believes establishing a link between the eBOM (engineering bill of materials) and mBOM (manufacturing bill of materials) is critical to the digital twin success. “The way the data is stored in the product lifecycle management (PLM) system is very different from the way it is in the manufacturing execution system (MES). So passing the data is difficult,” he pointed out.
Many exhibitors at the show, such as Siemens and JR Automation, are offering digital twin solutions and strategies.
For more, watch the DE Video News roundup from the show below:
About the Author
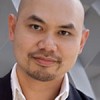
Follow Robotics 24/7 on Linkedin
Article topics
Email Sign Up
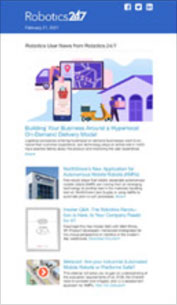
