Additive manufacturing is widely considered an intrinsic part of the factory of the future. The technology has developed alongside progress in robotics, with interest in manufacturing innovation leading to new methods of production. Metaphorically, it is the bloom of a new machine.
Additive manufacturing, or AM, represents only 1% of manufacturing so far, according to research conducted by SmarTech Publishing. To grow, the technology must overcome several challenges. They include the complexity of multiple fabrication steps, the high cost of scaling production, and a shortage of a skilled workforce to help control quality in the absence of industry standards.
Robots can help address the challenges in 3D printing process. Industrial automation and AM are becoming the ying and the yang of disruptive innovation. For example, robots and AM are currently most complementary in construction, precision manufacturing of wind turbine blades, and creating parts for both prototyping and production.
Complementary construction
Chattanooga, Tenn.-based Branch Technology uses a proprietary cellular fabrication (C-Fab) process that's blazing new trails with its behemoth KUKA robots to make large free-standing structures without dimensional restrictions or structural supports. The process uses pellets instead of filament or liquid, thereby reducing the amount of material required as well as waste.
Inspired by organic forms such as trees and human beings, the company employed the concept of a cellular structure with robots and 3D printing to create in a single pass large-scale facades, walls, pavilions, sculptures, and other architectural components and polymer structures.
Specifically, Branch Techology uses 12-ft.-tall, six-axis, customized industrial robots from KUKA. They can print parts up to 8 ft. by 8 ft. by 35 ft. in a single print. The robots move along tracks with multiple axes of freedom.
The robotic system uses a pelletized proprietary polymer conveyed through a complex network of hoppers, hoses, and drying mechanisms. The pellets are melted then extruded in a crisscrossed open matrix.
The robots play roles in additive as well as subtractive manufacturing. Branch manages a fleet of 17 additive robots and two subtractive, with more on back order. The company, which raised $11 million in December 2020, said it hopes to build a fleet of 40 robots to automate the entire process using AM. It added that its fast fabrication can help finish a structure in less time than traditional means.
Large-scale part production
San Jose, Calif.-based Orbital Composites collaborated with Oak Ridge National Laboratory in Knoxville, Tenn., and the University of Maine to pioneer the fabrication of wind turbines with using large-scale continuous fiber additive manufacturing. Part of the production process employed 3D-printing robots for the blade manufacture.
The production uses the University of Maine's monster 120-ft.-long 3D printer. Orbital Composites introduced its Mobile Robotic Additive Manufacturing with Continuous Fiber platform to the fabrication process. The platform uses a 12-axis robot arm that assists in the additive manufacture of unique surfaces.
Orbital Composites and its partners drew on their experience of utilizing AM with thermoplastic and thermoset (non-malleable) material reinforced carbon and glass fibers. In this case, they took the platform to a large scale. With multiple robot collaboration and a mix of suitable materials, they were able to fabricate wind blades over 100 m (328 ft.) long.
That's a lot of innovation and technology, demonstrating that 3D printing isn't just for widgets and plastic parts anymore. It can entail complex materials, large-scale fabrication, and be used with robotics to produce things that were previously unthinkable. In this case, a wind turbine blade just shy short of a football field in length.
The bloom of new ecosystems?
The combination of AM and robotics exemplifies the new bloom of ecosystems that are budding from industrial landscapes. When one disruptive technology combines with another, they can result in entirely new developments and once-impossible constructs.
And it’s not just the possibilities that such an ecosystem creates; it’s also efficiency. Fabrication and assembly are now possible with less labor, less waste, and less time. With smart collaboration, these reductions result in more—larger structures, better parts, and both at higher rates of production.
Despite the challenges of the global COVID-19 pandemic, innovation and smart technologies can combine for the greater good, according to a Deloitte insight on “Accelerating Smart Manufacturing.” Additive manufacturing and robotics represent one such combination.
“Essentially, an ecosystem is formed when different entities come together in meaningful ways to solve shared challenges and meet shared objectives,” said Deloitte analysts. “Effective ecosystems enable a cumulative 'network' effect for participants and create value greater than the sum of parts, driving higher performance and creating exponential results. Underlying all of this is the concept of collaborating and co-evolving.”
Based on solid research and survey results from manufacturers, Deloitte posited that smart manufacturing, and technologies that enable it, are on the rise. The pandemic has forced all industries to find smart solutions fast, in a world where resources suddenly became constrained or were outright unavailable. More than ever before, factory operators seek defenses against disruption.
“Why is the current environment ripe for acceleration? In many ways, the uncertainty of today’s fluid environment necessitates smart manufacturing capabilities for greater agility and speed,” said Deloitte's report. “As one executive said about the changes COVID-19 has brought, 'Capacity moves on a dime ... we don’t know what’s going to sell or who’s going to be able to come to work, so we’re being forced to move quicker [with smart manufacturing initiatives].'”
From the production of new large-scale structures to large wind-turbine blades, the chemistry created when AM and robotics combine is the result of of the new thinking regarding such ecosystems. Robotics and additive manufacturing can foster smart factories and lead to new efficiencies and products that could benefit us all.
About the Author
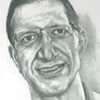
Follow Robotics 24/7 on Linkedin
Article topics
Email Sign Up
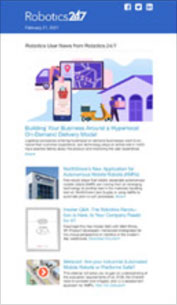
