Last month, robotics supplier ABAGY and Weld.com conducted a joint experiment in which a welder was able to operate a robot without special training within one day. ABAGY also surveyed the welding community to learn about worker attitudes toward robotic welding.
“Every single day, we hear from manufacturers that they can't find people,” said Dmitry Golitsyn, co-founder and chief technology officer of ABAGY. “According to American Welding Society research, more than 40% of welders are over 45 years old. To address this welder shortage, we can help people who are already in the industry become more productive with new technology.”
While robots are commonly seen as being useful only for the mass production of thousands or millions of identical items, such as automotive parts or electronics, ABAGY Ltd. said it is applying industrial robotics to non-serial production.
The Limassol, Cyprus-based company claimed that its software enables manufacturers to use robots for custom projects or even one-of-a-kind parts. No robot programming is required, it said.
ABAGY Robotic Systems Inc., the company's U.S. subsidiary, is based in Houston. It recently launched a welding robot demonstration workcell in California.
Welder puts robot to work without special training
Weld.com is a community platform where members can seek advice and network with industry experts. The welder community has developed a mobile app and is also present on social media. Its YouTube channel has more than 800,000 subscribers.
Austin Hargett, a.k.a. “Dr. Weldz,” is a welder with 14 years of experience and a member of Weld.com. He tested the ABAGY robot control system. Hargett defined welding parameters and put the robot to work without any special knowledge in robotics.
“Welding machines are changing. Technology is changing. My job is a constant evolution. As a welder, I believe that I need to learn something new every day,” he said. “And I agree with ABAGY that robots can be a new effective tool for welders. I'm really impressed with how simple and easy it was to get the robot up and running.”
Survey finds positive attitude toward automation
A poll of more than 2,900 people in the welding community found that 42% believe that robotics presents an opportunity to improve efficiency.
“There’s a prevailing preconception that robots will replace people. This is exactly what hinders the development of robotics,” noted Kate Degai, chief marketing officer at ABAGY.
“It is impossible to install robots if there are no people inside the factory who are ready to work with them and feel that this helps them to increase their own efficiency,” she said. “Therefore, we are open to a dialogue with the welding community.”
ABAGY discusses manufacturing and robotics trends
Degai also answered the following questions from Robotics 24/7 about ABAGY's perspectives on robotics adoption:
What do you think were the biggest trends in robotics in 2022?
Degai: These are adaptive, autonomous robots that do not require programming and, as a result, are applicable to high-mix, low-volume production. We see significant changes this year.
Previously, it was difficult for us to explain to robot manufacturers what this technology even is because they have never seen the promise of working with it. But the environment is changing.
Robot manufacturers have estimated that the high-mix, low-volume market is significantly larger than the automotive industry. And more importantly, manufacturers in other industries believed in it.
What accomplishments of ABAGY are you most proud of?
Degai: 2022 was a real launch year for us in the U.S. market. And we see a lot of interest from companies.
After Fabtech, we’ve been in negotiations with several hundred companies.
What were some of the biggest challenges facing your customers and the industry this past year?
Degai: Acute labor shortage. This issue has been talked about for a long time, but it has not been resolved yet. We hear about this from manufacturers every single day.
There is something called the “industrial robot paradox.” While robots increase manufacturing effectiveness by five to 10 times, which has been proven for many years by car manufacturers, robots are still used only in 1% to 2% of cases.
In order to overcome this paradox, powerful motivation is required. The rapidly growing labor shortage forces manufacturers into robotization. This seems to be a watershed moment for industrial robotics.
Software to improve robot efficiency in 2023
What are some promising technological developments?
Degai: Our software is compatible with various equipment—the main brands of robots, welding sources, and machine vision devices. We see the rapid development of technical vision devices, as well as the emergence of new functions for robots and welding sources.
Hardware is getting smarter. As a result, our algorithms become more advanced.
Looking ahead, how will companies manage economic uncertainty in 2023?
Degai: At such moments, two strategies are possible: save or, on the contrary, invest in more effective tools in order to successfully get through these times and get ahead of short-sighted competitors. Despite the difficult economic situation, it looks like there will be more of the latter.
What areas of robotics and AI still need work?
Degai: AI is a very powerful tool, but it is extremely dependent on the amount and quality of the data for the algorithms to learn. And there is a lack of good data sets, so it will take time to collect them.
What are you looking forward to the most this year?
Degai: We are very optimistic about the next year and expect an increase in the number of installations in the U.S.
We have two product formats. We either offer a turnkey solution that includes our software and robotic equipment, or a robotic cell retrofit.
Interestingly, there are even more customers who want to upgrade their inefficient robots with our software.
About the Author
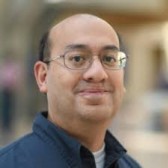
Follow Robotics 24/7 on Linkedin
Article topics
Email Sign Up
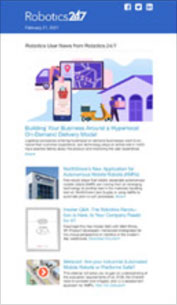
