Waltham, Mass.-based 6 River Systems (6RS), a provider of collaborative warehouse solutions and subsidiary of multi-channel commerce platform Shopify, said today that it has rolled out various enhancements to Chuck, its collaborative mobile robot.
6RS officials explained that the company’s solution is able to manage the entire fulfillment workflow, ranging from putaway to picking, sorting, and packing. And they added that the new improvements to its order allocation algorithm and organizations to batch, zone, and other picking methodologies focus on cutting down on associate walking in the warehouse, coupled with new modular and larger multi-level workspaces, help to make Chuck “the most flexible collaborative mobile robot in the industry.”
The enhancements 6RS has made to Chuck include:
- Increased capacity: up to 6 levels for a total of 43.5 ft2 / 4.0 m2 of workspace, over three times more than the other providers, handles a broad range of SKUs and a payload of up to 200 lbs / 90.7 kg;
- Expanded compliance: patent-pending safety system meets international safety standards, including CE and UL1740; and
- Improved usability: globally recognized lighting, images, and prompts accelerates training and directs associates through their tasks
6RS Vice President of Marketing Fergal Glynn said in an interview that these enhancements have been a long time coming.
“6 River Systems has been gathering feedback and examining customer data over the last two years,” he said. “These enhancements were implemented following the response from our customers that they would benefit from larger robots in order to carry more and larger items. We’re excited to now offer increased capacity and improved usability, allowing operators to maximize their equipment utilization.”
When asked what the biggest benefits of these enhancements to Chuck are for 6RS customers, Glynn explained that one of the biggest benefits of these enhancements is the ergonomic design.
“Frequently used buttons and the scanner are placed strategically on the robot to minimize ergonomic strain, and additional lights, images and prompts can direct tasks more precisely,” he said. “With this design, the system is easy to master and can be used by a broad range of workers after minimal training. Also, because the Chucks are larger, warehouses don’t need to utilize as many, freeing up space throughout the aisles. Having fewer robots is particularly helpful during peak seasons when staff presence and customer pressures increase and efficiencies need to be at an all-time high.”
In terms of how these new enhancements to Chuck provide competitive advantages and benefits for 6RS, Glynn stated that Chuck is the most productive and configurable collaborative mobile robot in the industry.
“Its competitive enhancements include increased configurability and capacity, expanded compliance and improved usability,” he said. “Chuck now has 3X more workspace than any other provider, with up to 6 levels for a total of 43.5 ft2 / 4.0 m2 of workspace. It can handle a broad range of SKUs and a payload of up to 200 lbs / 90.7 kg. Chuck is CE compliant and has received UL and CSA certifications, meeting standards for customers across the world. Chuck’s features also include globally-recognized lighting, images, and prompts that accelerate training and direct associates through their tasks.”
What’s more, in addition to these updates, Flynn said that 6RS has worked to add a new auto-load/unload capability, which will be on display at the MODEX show in Atlanta next month.
“This will allow warehouses to move the indirect labor associated with putting and taking off totes to other parts of their operation,” he said. “These new features, in conjunction with new software capabilities including case replenishment, singles batch, our Mobile Sort wall, packing, putaway, and dynamic zone, further expand our wall-to-wall capability and accelerate time to benefit, setting us apart from other providers.”
Glenn Sutton SVP Americas, Ingram Micro Commerce & Lifecycle Services, said in a statement that Chuck is essential in helping fulfillment operators need to scale quickly and cost-effectively to meet the growing demand for split-case and e-commerce volume, despite labor availability constraints.
“Operational efficiency is critical to providing an accurate and fast delivery experience, and the demand for this continues to grow,” he said. “Our solution from 6 River Systems enables us to increase our throughput and get more orders out the door and into customers’ hands. We are excited about their commitment to continually improving and developing their product.”
About the Author
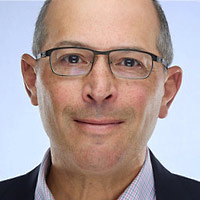
Follow Robotics 24/7 on Linkedin
About the Author
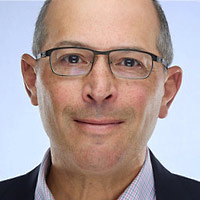
Follow Robotics 24/7 on Linkedin
Article topics
Email Sign Up
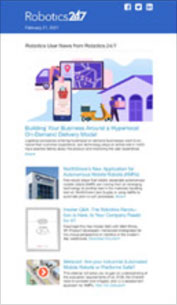
