As the world’s largest chemical company, BASF’s operations span 80 countries, six integrated production sites, and 390 other production facilities in Europe, Asia Pacific, Australia, Africa, and the Americas.
Domestically headquartered in Florham Park, N.J., the company faces some unique challenges when it comes to keeping its supply chain managers and employees around the globe well informed and up to speed with the latest knowledge and information.
“As the company has expanded, that proposition has become exponentially more difficult,” says Dirk Hopmann, BASF’s vice president of supply chain strategy.
Establishing common supply chain nomenclature across BASF’s operations, for example, and particularly in light of the firm’s many recent acquisitions of other entities, has been especially challenging.
To address that situation, the global manufacturer puts its new and existing employees through APICS’ certification process, starting with BASF’s supply chain managers.
“We know that management is the key driver of supply chain knowledge and skill sets, so motivating everyone from the supply chain manager all the way up to our senior leadership to get certified is very important.” says Hopmann. “We push the APICS courses out as pre-requisites for development in our supply chain division.” In addition, he says supply chain sales professionals also use the course as a “key ingredient”” of their training programs.
Going a step further, Hopmann says BASF has also used the certification courses with its business partners, particularly for orchestrating sales and operation planning processes. “Our goal is to help everyone understand the broad, end-to-end process that we’re handling here,” says Hopmann, “and all of the nomenclature and definitions associating with marketing, sales, and supply chain.”
To work toward that goal, BASF reinforces its training by recognizing and celebrating employees that achieve certification. “A senior leader usually hands over the certificates to the students, who, in turn, feel very positive about the experience,” says Hopmann.
In addition to the nomenclature knowledge gaps that it’s trying to fill, Hopmann says BASF also wrestles with the notion that not everyone understands why they are doing what they’re doing. “We want to make sure everyone is on the same page when we talk about order to cash, demand planning, and S&OP,” says Hopmann, “whether the employees are working here in the U.S., in Brazil, or in India.” And because getting face-to-face with remote employees isn’t always feasible, he says offers for APICS’ online coursework help.
“We like the first, basic training to happen live, but then continuous training takes place mostly online,” says Hopmann, whose team utilizes video-conferencing and Webex-type platforms to administer the training. The setup has proven especially beneficial over the last five years as BASF has expanded globally. “We have global processes, regulations, and supply to manage around the world now. Having a single source of knowledge and certification at our avail ensures that everyone is speaking to one another in the same supply chain language.”
Tackling Supply Chain-Specific Challenges
As companies like BASF have come to realize, gaps in the supply chain talent pool are both prevalent and pervasive. Whether they are keeping current workers up to speed, introducing new supply chain professionals to the mix, or a little bit of both, today’s organizations are taking the steps necessary to make sure there are no critical gaps in those workers’ supply chain knowledge.
Panos Kouvelis, professor of operations and manufacturing management at Washington University in St. Louis’ Olin Business School, says supply chain knowledge gaps present key challenges for many companies. The fact that the discipline itself is “fairly new” contributes to the challenge. “Companies have always had inventory analytics and material procurement professionals,” Kouvelis points out. “And while a lot of people moved up through organizations via these positions, most of them don’t have the required skills for supply chain management.”
So what’s So Different about Supply Chain Management?
According to Kouvelis, it’s a discipline that requires the individual to have cross-functional perspectives on operations, marketing, sales, and finance, among other components. “A supply chain manager has to be able to assess the entire organizational system,” says Kouvelis, “and then effectively interact with suppliers, distributors, and end users to figure out how to best integrate information, materials, and finance.” Here are five different ways that organizations are tackling that challenge and filling in the open gaps that exist within their supply chain talent pools:
1. Executive Supply Chain Education
It takes on different forms, all of them aimed at a similar goal: to bring existing employees and/or new graduates up to speed on the fine points of managing today’s complex supply chain. According to Kouvelis, executive education is targeted mainly at younger candidates that already have graduate degrees in other fields (business, economics, engineering, or math, for example). “Most have strong analytical backgrounds and are now interested in studying supply chains,” says Kouvelis, “and developing the skills needed to plan and manage such systems.”
Executive education generally requires a 12- to 24 month time commitment, depending on the school and the course format. Portland State University in Portland, Ore., for example, offers a 2-year, parttime online Masters of Science in Global Supply Chain degree. Cliff Allen, the program’s academic director, says the program covers all of the steps in the sourcing and logistics process – “from the product’s initial concept to its end-of-life.”
2. Supply Chain Certifications
Through the professional certification process, individuals gain knowledge, experience, and skills to perform a specific job. When the coursework is completed the student must earn a passing grade on an exam that is accredited by an association or organization that oversees and upholds the standards for the industry in question. Course length varies according to the offering organization and in most cases the instruction is either self directed or instructor-facilitated. Abe Eshkenazi, CEO at Chicago-based APICS, says certification helps companies fill in some of the newer gaps that are surfacing in supply chain knowledge, such as big data and analytics.
He says companies want real-world experience in such areas, yet the typical college education doesn’t necessarily address these newer points. “In many cases, a certification program can help differentiate the individual in the marketplace,” says Eshkenazi. Tom Derry, CEO of the Institute for Supply Management (ISM) in Tempe, Ariz., says certification helps address a broad range of supply chain skillset gaps for everyone from entry-level employees to department heads. “Through the certification process, companies can effectively identify the skills that are lacking and then hone their training around closing those gaps,” says Derry, who sees general business acumen and analytics as two areas that companies want to see their supply chain managers handle better. “Employees need a broader understanding of their businesses beyond just the mastery of technical foundations,” says Derry, “and then relate their individual value to the company’s overall strategy and success.”
3. Peer-to-Peer Mentoring and Cross-Generational Collaboration
In some cases, enhancing supply chain knowledge is a task that can be handled within the organization, where a goldmine of knowledge and hands-on experience lies within the existing workforce. “With the Baby Boomers heading into retirement, and with a high number of supply chain job positions to fill, we definitely need to be mentoring younger folks and driving leadership within supply chain positions,” says Lisa Angell, department chair and instructor of supply chain management at Fox Valley Technical College in Appleton, Wis.
Angell says mentoring and cross-generational collaborations can help new employees gain the knowledge and skillsets they need to succeed in their positions while also assisting older workers with concepts and technology that they may not be familiar with. “Put Baby Boomers, Generation Xers, and Millennials together and not only will they understand one another better,” says Angell, “but the process will also open everyone’s eyes to new ways of doing things.”
4. Cross Training and Job Rotation
Sometimes all of the education and certifications in the world can’t replace the hands-on experience that supply chain professionals gain from cross training on different jobs. “It gives individuals different perspectives on the supply chain,” says Eshkenazi. “If you truly expect someone to grasp all aspects of the supply chain and your organization, then you must give them job rotation activities to participate in.” A warehouse manager, for example, would benefit greatly from understanding how the procurement, production, and marketing departments operate, what are those departments’ core goals, and what strategies they use to achieve those goals. “Go beyond finance and supply chain,” says Eshkenazi, “and introduce your supply chain employees to all aspects of the organization.”
5. Partnering with Universities and Colleges
When developing coursework for its supply chain programs, Portland State University reaches out to area organizations to find out what skills and knowledge would help them operate more efficiently in today’s business world. “We’ve built out our curriculum around those needs,” says Allen, who advises shippers to use a similar approach to partnering with their own local universities and/or colleges. By working with a business school, for example, companies can help establish programs that fill real-world needs. “Today’s higher-ed world is very competitive,” says Allen, “and we’re all looking for ways to better engage our local communities and organizations.”
Download the full article including a list of:
- Universities and Educational Institutions
- Professional Associations
- Private Firms
Related: Job Description & Salary: Supply Chain Management
About the Author
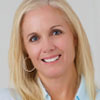
Follow Robotics 24/7 on Linkedin
Article topics
Email Sign Up
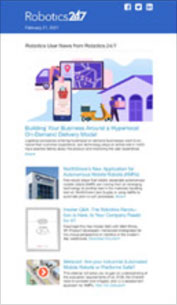
