One of the many laudable essential workers of the COVID-19 era is proving to be 3D printing technology, which is being harnessed in force to churn out face masks and face shields, all of which have been in short supply for the duration of the global pandemic.
Across the world, 3D printing technology providers and service bureaus are teaming up with government agencies, hospitals, and corporate enterprises in myriad public-private partnerships to coordinate and build open-source medical supplies in response to COVID-19. For its part, the Food and Drug Administration (FDA) is facilitating public use of 3D printing technologies to meet demand for medical equipment with a series of FAQs, recommendations, and guidelines. In addition, the FDA, in concert with the Veterans Health Administration (VA), and the National Institutes of Health (NIH) have committed to share data and coordinate on open-source medical products for the COVID-19 response via the NIH 3D Print Exchange, a collection of 3D design models for masks and other medical parts. America Makes’ role is to serve as a connector of sorts via an online repository that tracks the capabilities and capacity of 3D printing companies, manufacturing service providers, and designers willing to share 3D print designs, matching them to healthcare organizations that have specific needs during the COVID outbreak.
“When COVID-19 hit, everyone needed PPE, but traditional sources were quickly out of stock and their production lines couldn't catch up to the demand quickly enough,” notes Christina Perla, founder and CEO of Makelab, a 3D printing services company. “The 3D printing community jumped into action, creating open-sourced designs that were approved by health organizations. One of 3D printing's best advantages is that it offers an agile and lean supply chain, so it was a great stop-gap solution that could mobilize quickly and hold the demand while traditional manufacturers caught up.”
In April, Makelab made a decision to pivot from its traditional work to manufacture protective face shields for essential and frontline workers. At the time, demand for raw material was high so the firm had to get creative to effectively build out a supply chain. After some brainstorming, the team landed on a common clear plastic binder from Avery as the base for the mask. For rest of the face shields, the team is using FDM 3D printing technology. “It works like an advanced glue gun, melting down hard plastic and re-extruding it in a pattern, laying down layer by layer,” Perla says. “It is quick and we were able to stack prints to maximize our machines during off hours.” More recently, Makelab introduced a custom mask through a partnership with Bellus3D, which employs an app that uses iPhone's FaceID camera technology to 3D scan a person’s face. From there, a model is generated to produce a custom mask fitter using SLA technology that helps to improve the seal of surgical masks.
Companies in the 3D printing sector are also stepping up. Essentium, a provider of 3D printing technology, is making 3D printed face masks that meet ASTM Level 2 filtration media guidelines for Sulzer, a company providing critical services to the power, water, and process industries, which was designated an essential business. “The global shortage of masks could have made it challenging for us to remain open,” said Darayus Pardivala, president of Sulzer’s rotating equipment services division, Americas. “Essentium’s ability to produce a quality solution at scale and to our timeline solves the issue.”
RIZE, a manufacturer of 3D printers and materials, is doing its part to keep the PPE mask pipeline full. The company has created RIZE Shields, face shields that take advantage of RIZIUM One to offer a safer, lighter weight, and more comfortable product than traditional shield offerings. RIZIUM One is a USP Class VI certified material, which is the industry’s highest level for biocompatibility, ensuring that wearing for long hours won’t have adverse impact on human skin. In addition, the material is resilient and able to withstand copious use of sanitizing agents, which isn’t the case with many of the more common thermoplastic polymers used in 3D printing such as ABS.
RIZE Shields can also be personalized with essential frontline workers names as well as messages thanks to the RIZE Augmented Polymer Deposition (ADP) hybrid 3D printing technology, which allows text and full-color images to be printed within the shield. “The ability to personalize RIZE Shields helps COVID-19 heroes to be recognized not just as faceless people behind a mask, but as brave individuals who are placing themselves at risk to aid their communities,” said Andy Kalambi, CEO and president of RIZE, in a press release.
Watch this video to see how RIZE produces its RIZE shields.
About the Author
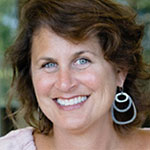
Follow Robotics 24/7 on Linkedin
Article topics
Email Sign Up
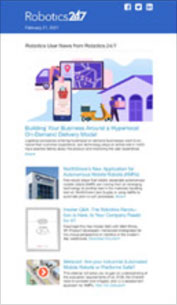
