Editors’ Picks
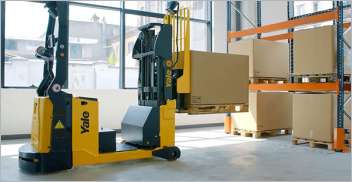
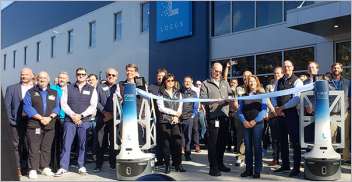
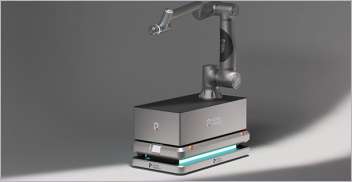
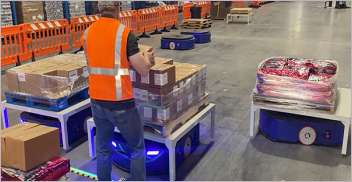
Found in Robotics News & Content, with a score of 12.08
…more than 10 years for applications such as mapping, navigation, and autonomous decision-making. Working with the Robot Operating System (ROS), the cloud-based Nimbus includes a library of pre-configured algorithms and enables developers to collaborate and to monitor robot performance in real time, said the company. Israel Innovation Authority looks to improve HRI Most of today’s robots are built for single-mission tasks, but they are increasingly engaging with humans, said Cogniteam. Robots will need to assess social situations and communicate verbally and non-verbally with the people around them. For example, a mobile robot could ask for human assistance after diagnosing that…
Found in Robotics News & Content, with a score of 7.46
…Even though some mobile robots are dependent on fixed navigation infrastructure, they require little additional installation. Set up typically only requires laser reflectors, magnetic tapes, inductive wires, and barcodes/QR codes. Software initialization can usually be completed remotely or on the cloud. Hence, the installation time for AGV systems typically only takes 2-6 weeks, the research firm reported. For autonomous mobile robotic units, the installation can be shorter as robots only need to be shown around the facilities and no additional change to the environment is needed. Source: IDTechEx A smart return on investment A large amount of up-front capital is…
Found in Robotics White Papers & Archives, with a score of 31.55
With the AGV market expected to grow at a 50% compound annual growth rate (CAGR) for the next four years, (from an already expanding value of USD $3.66 billion in 20181), it’s easy to forget that these vehicles have grown from a niche market to one of the fastest growing segments in the service robotics industry. Indeed, only a decade ago, just two main applications were common for automated guided vehicles: moving pallets in warehouses (intralogistics), and in manufacturing (primarily the production of cars). However, a number of factors, from the rising demands of e-commerce, to the potential productivity, flexibility…
Found in Robotics News & Content, with a score of 6.95
…Aurora Driver Beta 2.0. Features in the update include: Advanced highway and suburban capabilities, including more complex construction zone navigation, key for hauling freight across the country. Upgraded cameras with higher resolution, allowing for obstacle detection at 2x the distance. New commercial route between Fort Worth and El Paso supported by daily map updates.
Found in Robotics News & Content, with a score of 18.82
…you to add extra functionality (on top of autonomous navigation), such as a conveyor belt or robotic arm. Keep in mind that not all hardware can be automated smoothly. Some manually-driven vehicles may not readily accept automation; for example, drive technology and control systems may need to be replaced with new versions that are easier to automate. Tip: Define what features your automated vehicle system will need, and which of its existing components are not automation-ready. This will help you assess whether you can add automated guidance easily, or whether it would be better to start from scratch. 2. What…
Found in Robotics News & Content, with a score of 9.55
…operations, while only guiding the operator. The system enables navigation with greater precision and predictability, helping to reduce costs, fuel consumption, and emissions, said the companies. It includes fusion of digital marine sensors, embedded electronic charts, AI algorithms, and broad-area computer vision, according to Sea Machines and Rolls-Royce. mtu NautIQ CoOperate is an optionally autonomous ship navigation command system which enables off-boat remote command, including all payloads on board. The system can take over routine and monotonous vessel tasks, and it allows crews to focus on more important aspects of their missions, the companies said. The tug Nellie Bly used…
Found in Robotics News & Content, with a score of 12.06
…for a wide range of load capacities, lift heights, navigation methods, temperature ratings, and software applications, the company said. Murata partners with AGVE in North America From its headquarters in Charlotte, N.C., Murata Machinery will take over and lead all North American operations in partnership with the AGVE Group, directing day-to-day North American sales, installation, service, and marketing operations. AGVE is a part of the Murata Machinery Group. Since 1985, the company has deployed more than 4,000 general vehicles and 160 custom-made ones. “Combining our AGV sales and service operations in North America into a single-unified front enables us to…
Found in Robotics News & Content, with a score of 6.53
…all driverless forklifts, not just those driven by BlueBotics navigation technology). However, that’s just 0.3% of the one million forklifts and lift trucks of all types which were deployed in that year. But that number is predicted to grow dramatically. The predicted growth of automated forklift systems Automated forklift system sales are predicted to grow by as much as 64.5% every year until 2028, according to market research firm Interact Analysis. This is a massive increase on the previous predicted growth rate of 20-25%. In fact, as soon as 2023, as much as 5% of the entire United States’ forklift…
Found in Robotics News & Content, with a score of 23.50
…Oceaneering International announced that BlueBotics SA will provide the navigation technology for its line of industrial mobile robots. Founded in 1964, Oceaneering International said it has deployed more than 1,700 autonomous mobile robots (AMRs) worldwide, with over 30 million miles accumulated. The Houston-based company has offices in Asia, Africa, Europe, and the Middle East. Its products include the MaxMover CB D 2000, the Compact Mover FOL U 1200, the MontoMover Dual O 2000, the MontoMover Quad O 1200, the MontoMover U 400, the UniMover U 1500, the UniMover 0 600 and the UniMover D 100. More than 3,000 vehicles using…
Found in Robotics News & Content, with a score of 13.65
…MaxMover CB D 2000 is designed as a true replacement of conventional counterbalance forklifts. Oceaneering selected BlueBotics to provide navigation technology for its industrial autonomous mobile robots. “Our goal is to unlock the full potential of mobile robotics and enable widespread adoption in all industries,” said Henny Bouwmeester, VP and GM. “BlueBotics, with its proven technology that requires little to no additional infrastructure, will be an integral part of our solution stack.”
Found in Robotics News & Content, with a score of 13.67
…The Palion Lift AMR brings together Seegrid’s 3D vision-based navigation technology with situational awareness capabilities. The company added that the Seegrid IQ autonomy technology fuses data from cameras, lidar, and machine learning models to enable its autonomous forklift to move material safely, accurately, and reliably in complex and dynamic environments. “Our highly-reliable and proven 3D vision-based navigation system is now augmented with additional sensing modalities to create the latest generation of Seegrid IQ,” said Todd Graves, chief technology officer at Seegrid. “This advances our perception, localization, planning, and safety systems—increasing the human-like situational awareness and agility of our AMRs, a…
Found in Robotics News & Content, with a score of 6.21
…fulfillment productivity coupled with agile maneuverability, incorporating the latest navigation and vision system technologies, said Locus. It works collaboratively with associates in dynamic warehouse environments. Locus Vector—The industrial-strength AMR has flexibility for a wide range of roles, from fulfillment to transport to putaway, according to the company. Locus Vector features omnidirectional mobility, compact design, and robust payload capacity for use in any environment. Locus Vector will ship to customers starting this summer. Locus Max—This heavy-duty robot is designed to transport a wide variety of heavy materials, cartons, or pallets across facilities. Locus Max is intended for industrial and material handling…