Just-in-time manufacturing depends on supply chains operating at the highest-levels of precision possible.
Materials arrive on-site just before manufacturing commences, enabling production operations to stay lean and squeeze maximum output out of available space, but leaving little slack time or margin for error.
This paradigm pressures each piece of the supply chain to hold up its end of the bargain, from shipping vessels to materials handling equipment.
The COVID-19 pandemic presented unique challenges to global supply chains, with lockdowns and public health effects wreaking havoc and causing delays for finely tuned manufacturing operations.
But that was just the beginning – semiconductor and other commodity shortages in the automotive industry led to temporary plant closings and a shift to a more proactive approach to component sourcing, rather than the purely lean methods that have guided manufacturers for decades.
Unique global events and related supply issues are spurring change in manufacturing. What was once a laser focus on the just-in-time paradigm is now tempered by a level of just-in-case planning, pressuring material handling operations to support evolving methods of doing business.
Doing so requires a partner with the broad range of experience, both in manufacturing and elsewhere in the supply chain, to apply new ideas and technologies that uphold the standard of efficiency that modern just-in-time manufacturing requires.
Article topics
Email Sign Up
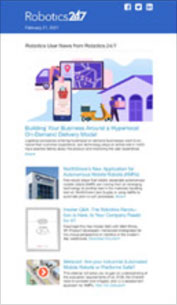
