The pandemic meant warehouses had to cope with social distancing and staff absences. It also caused a massive e-commerce boost and has led to a protracted labor shortage.
All this has forced warehouse managers to take a deeper look at the possibilities offered by warehouse automation and to accelerate any existing plans they had to automate. The goal is not only to improve the efficiency of their businesses in a newly competitive landscape, but also to boost staff retention by improving working lives. At the same time, the pandemic has highlighted that nothing is certain and that industries can be turned upside down overnight. Flexibility for operations and not being tied to major infrastructure for too long is of much greater importance.
On top of COVID-related challenges, other major changes in the market are afoot too. These include so-called ‘masscustomization’ which, for warehouses, means that the product lines they have to store and deliver are liable to change size and shape at short notice. As well as demands for ever more rapid delivery.
An AMR solution usually presents several major benefits compared to fixed automation: it is more cost-effective, it is faster to deploy, it is more flexible, and it is easier to scale. New mobile robot solutions are enabling robots to select individual totes and bring them to pickers, instead of bringing whole racks, resulting in major efficiency improvements. Meanwhile, combining sophisticated software management systems with the wide variety of AMR platforms now available gives the option of knitting different robot types together into a single solution.
Ultimately, this presents the possibility of a wholesale replacement of fixed automation solutions with mobile ones. To put it bluntly: if a team of well managed mobile robots can pick and carry any item to any location in a warehouse, why would anybody ever install a fixed conveyor belt ever again?
Fill out the information below to download the resource.

Article topics
Email Sign Up
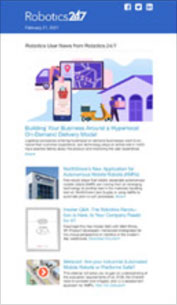
