Warehouses and distribution centers, or DCs, can make or break a supply chain. Within these facilities, efficient order-fulfillment operations can meet demand, satisfy customers, and adapt to anything ahead. On the other hand, inefficiencies lead to order delays, costly errors, and even bigger problems when unexpected disruptions arise.
With so much on the line, it’s no surprise that nearly every company is looking for ways to make their warehouses and DCs run better and faster. But what may come as a surprise is the relatively low adoption rates for one of the best solutions out there: automation.
Warehouse automation benefits and barriers
Forward-thinking companies have introduced automation to optimize the flow of goods moving into, within, and out from their facilities. Robotic solutions can take on everything from goods receiving, to storage and retrieval, to order picking, packing, and shipping. And they do it all with maximum speed, efficiency, and accuracy.
Despite these benefits, the adoption rate for robotics and automation only stands at an estimated 28%. What’s keeping more companies from making the investment? For one thing, we still see many misconceptions surrounding automation. All the confusion leaves companies questioning whether automation is the right fit for their warehouse, or even a feasible option.
In this article, we’ll look at four common myths that hold companies back from automating—and shed some light on the reality of each concern.
Myth 1: Robots are detrimental to the workforce
One common misconception is that automation takes or eliminates jobs from human employees. But In reality, automation can create better, safer job opportunities.
For years, companies have struggled to hire and retain enough warehouse workers to keep operations running smoothly. Hiring and retention challenges are largely due to shifting workforce demographics.
Members of the older generation are gradually retiring or leaving the industry in favor of less physically demanding jobs. Younger job seekers aren’t lining up to fill their shoes, preferring careers focused on technology rather than traditional warehouse work. The resulting labor shortages put massive strain on warehouses, where existing employees are left struggling to keep up with demand.
This is where automation comes in. Warehouses can automate repetitive, labor-intensive order fulfillment tasks, reducing stress on human staff.
Employees can shift to entirely new roles created by automation, such as operating, supervising, and maintaining robotics systems; analyzing data to continuously improve operations; or handling products with special requirements.
These career options are safer and more engaging for existing employees, and they may also attract the younger generations who are eager to work with technology.
Myth 2: Automation isn’t suitable for perishable products
Certain product types have particularly complex handling requirements. Companies that distribute these products tend to believe that their operations are not compatible with automation, so they stick to the same old inefficient manual processes.
However, advancements in technology are now making it possible to automate product handling for nearly any type of goods. One great example comes from the grocery industry.
In the past, grocery retailers have typically focused their automation investments on shelf-stable goods. Fresh and perishable food distribution, on the other hand, has remained mostly manual. Why? When handling perishable products like fresh produce, dairy foods, and baked goods, time is of the essence.
These products need to move through the distribution process as quickly and efficiently as possible to maintain quality and freshness. Otherwise, they could spoil prematurely, creating excess waste, food safety issues, and unhappy customers.
Previous generations of robotic systems weren’t built to meet this need for speed. They were set up to manage product storage and picking as two separate functions, which slows the overall order fulfillment process.
Modern automation technology can solve the speed challenge. Solutions are now available that combine buffer storage and order picking into one fast, seamless operation.
Fresh and perishable foods can enter the system as soon as they arrive at the facility, get picked immediately, then reach store shelves faster than ever before. With this new breed of automation, some grocery retailers are delivering fresh food from farm to store in just 24 hours.
Myth 3: Automating means high costs and new construction
Costs are often cited as barriers to automation adoption. Budgets are tight, interest rates are high, and business leaders see automating as a massive investment with uncertain return on investment (ROI).
This perception comes from the misconception that automation projects always require high costs, lengthy implementation timelines, and the construction of an entirely new facility.
Fortunately, companies can break down cost barriers by getting creative with their automation strategy.
Investing in modular automation is a great way to keep costs down and speed implementation for rapid ROI. Best of all, companies can retrofit their existing facilities with modular systems—no new construction required.
Modular systems are made up of individual, standardized cells of automation. These modules are like building blocks.
They can be arranged to fit any facility, even older buildings with low ceilings. Warehouses can initially install automation modules in areas where they will make the biggest impact. Then, modules can be easily added over time to expand the system’s capacity and meet new business needs.
Plus, modular systems can further reduce costs through a gantry design and high-density floor-based storage.
In this setup, products are stored in plastic crates, stacked directly on the warehouse floor. Gantry robots can access any SKU, at any time, from overhead, eliminating the need for expensive racking or shelving systems.
Myth 4: Automated systems are difficult to learn and maintain
With any automation project, it’s true that warehouse managers and staff need to prepare for change. This includes learning how to operate, maintain, and supervise their automation system. The good news is that upskilling efforts don’t need to be a big challenge.
Companies should select an automation provider that not only supplies technology, but also acts as a dedicated partner long after the system handoff is done.
A thorough partner will offer custom training programs to upskill its client’s warehouse staff. Training starts very early in the project, which ensures everyone is well-versed on optimal system usage and maintenance by the time installation is complete.
After that initial training, automation providers can also offer long term support to maximize system uptime. They can do repairs, replacements, and preventive maintenance, as well as suggest upgrades and modernizations over the system’s lifetime.
As technology advances, automation providers are even introducing new ways to provide better, faster support. One great example is anytime/anywhere support through assisted reality (AR) glasses. AR glasses can connect warehouse staff to their partner’s support team through a live video feed.
The support team can troubleshoot problems, guide warehouse staff through solving the issue, and get the automated system back up and running in no time.
Getting ahead of the game
While the warehouse automation adoption rate is relatively low today, it won’t stay that way for long. Some research reports predict the rate will grow to nearly 80% over the next five years.
Companies will need to automate to stay competitive, and now is the perfect time to get started. With the right technology, partner, and perspective, taking on an automation project will be easier than most think.

About the author
Adam Gurgra, is sales manager at Cimcorp North America. The Alpharetta, Ga.-based company said it has partnered with customers on warehouse, distribution center, and tire manufacturing facility projects to produce strategic, streamlined systems.
Article topics
Email Sign Up
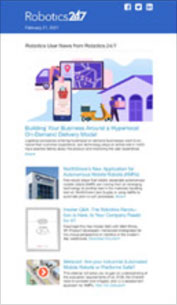
