3D printing has expanded from primarily being used to make quick physical prototypes to a solution for short-run manufacturing, bespoke offerings and complex parts that just can’t be economically made via traditional methods.
“By 2030, the number of production-ready additive manufacturing platforms that ship each year will increase more than tenfold (more than US$325 billion in hardware and related systems revenue),” according to ABI Research’s white paper: The Industrial Revolution, the Top Trends and Takeaways from Hannover Messe 2019. “These systems will produce more than US$360 billion worth of parts and end products each year (up from US$6.8 billion today) and nearly US$2 trillion in sum by the end of the next decade.”
That amazing growth would be thanks to the real benefits additive manufacturing provides, allowing engineers to create new designs that mix materials or vary materials throughout a part to achieve specific structural characteristics. Other processes allow for a wholesale redesign where multiple parts are melded into a single, more efficient unit. Engineers are also developing and incorporating intricate lattice structures into designs as a way of lightweighting components. To take full advantage of these benefits, however, design engineers need to adopt a design-for-additive manufacturing (DfAM) approach to consider 3D printing’s strengths and weaknesses early in the design, ensure the optimal use of polymer and metal materials, minimize failed prints or even avoid damaging expensive additive manufacturing machinery.
Four DfAM factors to consider, especially when working with metal materials are:
- residual stress from heating and cooling as each new layer is created can lead to distortion;
- how orientation affects build time, part strength and surface finish;
- placement of support structures and how they affect warping and post-processing; and
- topological optimization, including internal lattice structures.
New and updated software tools are emerging to meet these needs by exploiting the latest professional workstations and the visualization muscle of graphics processing units (GPUs). They make it possible to efficiently incorporate topology optimization and generative design, as well as simulation of part placement and layer-by-layer printing into a DfAM workflow.
Additive Manufacturing with GPUs
One new company looking to speed product development with graphics processing units (GPUs) is Dyndrite, a Seattle startup that says its “hybrid” technology kernel is capable of representing all current geometry types, including higher order geometries such as splines (NURBs), surface tessellations, volumetric data, tetrahedra and voxels. Additionally, the company says users can seamlessly move between geometric representations without destroying the original underlying data format.
The first application for the new geometry kernel is the Dyndrite Additive Toolkit, which is designed to improve 3D printing workflows. The toolkit directly imports CAD design files, maintains original spline data and uses the data to drive additive manufacturing processes. The fully native GPU Kernel handles additive-specific computations such as lattice, support and slice generation, in some cases reducing compute times from hours or days to minutes or seconds, according to the company. For heavy use cases, the Dyndrite kernel is naturally scalable with access to additional GPU nodes, whether locally or in the cloud.
Workstations can be equipped with multiple GPUs to handle a variety of DfAM tasks. For example, the Dell Precision 3000, 5000 and 7000 series of fixed workstations and mobile workstations can all be configured with NVIDIA GPUs. They are also certified for use with popular design engineering software packages.
“Dyndrite's geometry kernel is purpose-built to use every bit, flop, register and clock cycle of the latest NVIDIA GPU,” said Shawn Hopwood, Dyndrite’s chief marketing officer. Thank's to NVIDIA's GPGPU programming paradigm, CUDA, Dyndrite can run all the computations of its kernel on the GPU. Though Dyndrite minimally needs a Maxwell architecture to run, the latest Turing line computes 5-15x faster over the Maxwell line for Dyndrite's CAD to Print workflows.
Another additive manufacturing startup is Atlas 3D. Its thermal circuit network simulation process can work with either GPUs or CPUs. The product—Sunata—simulates the build process to find the optimal orientation for printing and automatically generates support structures. Chad Barden, CEO of Atlas 3D, says the CPU-based Sunata can calculate 100 orientations using thermal distortion faster than most competing solutions can simulate distortion on one orientation. The new GPU version, Barden tells DE, is “20 times faster than the CPU version.”
First-Time-Right
“What we see is that in order to industrialize and use the (additive manufacturing) technology in higher volume production scenarios, we need to do a few things to get it right,” Ravi Shankar, director of global simulation product marketing for Siemens PLM Software, tells DE. “One critical area is to do what we call first-time-right print. Typically, companies attempt to print a part multiple times at a high cost before they actually achieve an acceptable result. That is delaying the transition of what is a very exciting technology into real production scenarios.”
That affects what is traditionally thought of as a strength of 3D printing, as opposed to traditional manufacturing: material waste. However, 3D printing still has a higher amount of scrap than traditional manufacturing. In addition to material cost, additive manufacturing systems energy costs and the labor required to load, monitor and maintain them all add up.
“A number of factors complicate minimizing the cost of additive manufacturing, including build orientation, envelope utilization, build time, energy consumption, product design, and labor,” according to NIST’s Costs and Cost Effectiveness ofAdditive Manufacturing. “The simple orientation of the part in the build chamber can result in as much as 160% increase in the energy consumed. Additionally, fully utilizing the build chamber reduces the per-unit cost significantly.”
Being able to visualize the additive manufacturing process and optimize its many variables via DfAM software and techniques will further increase the rate of adoption in additive manufacturing.
About the Author
Press releases may be sent to them via [email protected]. Follow Robotics 24/7 on Facebook
Follow Robotics 24/7 on Linkedin
Article topics
Email Sign Up
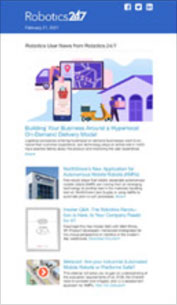
