Many of the robots displayed at Pack Expo in Las Vegas this week included vision systems designed to eliminate or at least greatly reduce the need for human oversight in various packaging operations. The more that such oversight can be eliminated, the more efficient the robots and the quicker they can provide a positive return on investment, said the vendors.
The global vision-guided robotics market was valued at $5.97 billion (U.S.) in 2018 and could reach $12.03 billion by 2026, according to Research and Markets. It projected a compound annual growth rate (CAGR) of 9.8% to 2029.
“The increasing need for automation and safety, high labor costs, a shortage of qualified workforce, and increased investment in research and development activities are driving the vision-guided robotics market,” said Research and Markets. “Machine vision is utilized in a variety of industrial operations, including material inspection, object recognition, electronic component analysis, signature recognition, optical character recognition, and currencies.”
“A vision-guided robot (VGR) system is a robot having one or more cameras used to supply the robot controller with a second feedback signal, to move more accurately to a variable destination,” said the analyst firm.
The following companies showed robots guided by machine vision at Pack Expo:
BluePrint Automation
BluePrint Automation’s robotic carton-loading system uses its delta robot with vision to pick random, unoriented products. This eliminates the need to correctly orient the package before it goes on the conveyor belt, said the company, which has offices in Virginia, Colorado, and the Netherlands.
The vision system also detects packaging problems such double wraps or bad product size. The carton loader can pick and place any product count or configuration.
FANUC
At Pack Expo, FANUC featured a few different vision-enhanced robots. The CRX-10iA/L collaborative robot used its iRVision 3DV/200 vision sensor to locate a box, pick it up from one pallet, and place it on another pallet. The CRX cobot supports several of FANUC’s advanced features, including the company’s iRVision technology.
The same technology was part of FANUC’s DR-3iB/8L food-grade delta robot, which also used Fanuc’s iRPickTool line tracking software in a Pack Expo demonstration to pick randomly oriented pieces of chicken from a continuous infeed conveyor. Equipped with a Soft Robotics gripper, the robot picked chicken breasts and reoriented them onto an outfeed conveyor.
The DR-3iB/8L has a four-axis design to handle payloads up to 8 kg (17.6 lb.), a reach of up to 1,600 mm (62.9 in.), and 500 mm (19.6 in.) height. It works with the company’s latest R-30iB Plus controller with integrated intelligent functions such as FANUC Force Sensing, Robot Link, Collision Guard, and Zero Down Time (ZDT).
Rated IP69K, the robot meets strict food-handling regulations and includes corrosion-resistant materials, an unpainted finish, and a fully enclosed body to tolerate high pressure/temperature and sanitizer wash-down environments.
The FANUC M-10iD/12 robot created random orders by picking from four homogenous totes, each with a 3DV/400 vision sensor mounted overhead. Each of the four sensors was designed to provide “best pick” locations from the homogenous totes, and then the robot picked parts to fill a customer order, said the company.
Upon completion of the order, the tote moved to an LR Mate 200iD robot station also equipped with a fixed 3DV/400 to remove the parts from the bin for further processing.
The 3DV/400 vision sensor can be used as a fixed or robot-mounted 3D vision camera. It features single-snap 3D image acquisition for faster bin picking and line tracking capability.
Honeywell
Honeywell’s Smart Flexible Depalletizer, first unveiled the week before Pack Expo, includes a robotic arm guided by advanced vision and perception technologies, enabling cases to be picked from a single- or mixed-SKU pallet on a fixed or mobile location.
The computer vision technology identifies the exact location of every case on the pallet, while perception software automatically recognizes a wide variety of packaging to allow for seamless handling of a continuous flow of pallets in any sequence without requiring any pre-programming or operator intervention.
The advanced machine learning and motion planning optimizes the movements of the robotic arm to ensure maximum picking speed and efficiency. The control logic also senses the weight of each item as the robot lifts it and automatically updates its gripping response to transfer each product securely and effectively. The more the system picks, the more it learns and continues to improve in quickly and efficiently unloading pallets.
The depalletizer can work with autonomous mobile robots (AMRs) to enable continuous operation while providing the flexibility to stage pallets and empty stacks virtually anywhere the robot is capable of traveling, said Honeywell.
Mujin
Mujin Inc.’s robotic palletizing with autonomous mobile robot pallet transport includes a gripper capable of handling cases, slip sheets, and pallets to build multiple pallets into a single stack, after which AMRs deliver the full pallet to the pallet break down area. AMRs will also bring empty pallets and slip sheets to the work cell, said the Japanese company.
The robot arm is equipped with 3D vision on the gripper to find the position of the pallets and slip sheets for the robot to pick, using the company’s proprietary perception and motion planning capabilities.
Omron
Omron Automation showcased a “mini-factory,” a combination of robotics, vision, motion control, and safety technologies. The mini-factory included an Omron TM14M robot manipulator arm mounted on a LD-250 autonomous mobile robot using the company’s FH3D bin-picking vision technology.
A workcell with Omron parallel robots moving between product positions allows for integration with the programmable logic controller (PLC). It can monitor different states and states and allow for user interaction with the machine.
Each robot included Omron Sentech Machine Vision sensors to generate input to Omron’s ACE PackManager programming.
To ensure quality, the company said its mini-factory used a vision inspection system with three high-speed Omron vision cameras.
About the Author
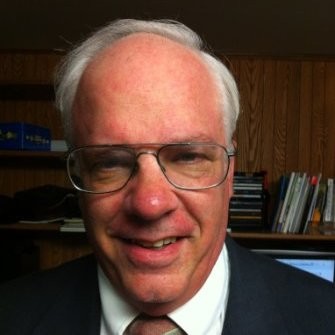
Follow Robotics 24/7 on Linkedin
Article topics
Email Sign Up
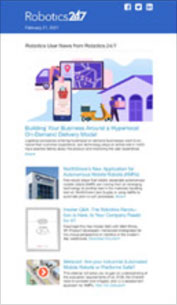
