Collaborative robot arms have been reaching into new applications as they gain capabilities. The new UR20 cobot from Universal Robots A/S will be on display at FABTECH, which is billed as “North America’s biggest metal forming, fabricating, welding and finishing event.”
The new robot has an additional 18 in. of reach radius, or a 36-in. diameter increase, greatly broadening the range of weldments that will be achievable in a given fixture setup, said Josh Pawley, co-founder of Vectis Automation, a Universal Robots partner.
“Vectis Automation is ecstatic to offer the long-reach UR20 arm onto our integrated cobot welding and cutting tools,” he stated in a release. “This cobot will have a huge impact on the market, improving on UR’s already robust and high-performance cobot products.”
Pawley noted that the next-generation cobot's design enhancements include 50% fewer parts in the axis drivetrains. In Universal Robots' FABTECH Booth B17063, Vectis Automation will show its UR20 Cobot Welder integrated into a rigid 48 x 48-in. XL Cart with a heavy-duty, water-cooled package.
UR partners Hirebotics and Melton Machine & Control Co. will also show the UR20 in addition to a press-brake tending application from Cincinnati Inc.
Coordinated motion promises to increase productivity
Will Healy, global segment manager for welding at Universal Robots, said he looks forward to the UR20’s welding and bending debut at FABTECH, which is from Sept. 11 to 14 in Chicago.
“We redefined the cobot, completely re-engineering it from the ground up,” he said.
Healy added that UR will launch a new coordinated motion feature through partners as part of its PolyScope software. With coordinated motion, the cobot and external axis – such as a rotary positioner or a linear rail – can move in sync.
“Coordinated motion enables fabricators to weld larger or more complex parts without having to manually reposition the work piece or welding robot,” explained Healy. “This means UR cobots can weld more parts per run for increased efficiency and are capable of welding bigger and more complex parts.”
Universal Robots will demonstrate the new coordinated motion feature at FABTECH, as will partners THG Automation and Vention in their booths.
AI generates welding, cutting parameters
Since its first cobot-powered welder premiered in North America at FABTECH 2017, numerous OEM partners have standardized their welding systems on the UR platform, constantly innovating their offerings, noted Universal Robots.
At this year’s show, Hirebotics said it will launch Beacon Recommendations, a new feature that uses artificial intelligence to recommend welding and cutting parameters when setting up a part. This will help manufacturers save time and improve the quality of their welds and cuts, it claimed.
Hirebotics is also launching the Cobot Cutter, its first UR cobot-powered system for plasma cutting.
Partner launches first cobot for grinding
After a weld process is completed, fabricators often have to perform the hazardous chore of manual grinding and finishing, said Universal Robots. Equipped with the precision of a UR10e cobot and FerRobotics’ ACF-K end-of-arm grinding tool, the new GRIT system from UR partner Kane Robotics is intended to free workers from this tedious task.
GRIT can grind welds at twice the speed of human technicians while improving material removal productivity by as much as 50% to 80%, asserted Kane Robotics.
New chip mitigation system for cleaning jaws
Partner VersaBuilt is launching another material removal update at UR’s FABTECH booth. It will show its cobot-powered Mill Automation System with VersaWash.
VersaWash is designed to increase reliability and efficiency by deep-cleaning jaws and parts to clear chips while a CNC machine is running. The Mill Automation System now also features MultiGrip Pallets for applications where customers prefer to fixture a single or multiple parts to a pallet and process multiple pallets automatically.
Kit optimizes CNC machine feeding
Manufacturers visiting UR’s booth looking to optimize parts feeding can see UR partner PBC Linear's demonstration of its Applied Cobotics Cobot Feeder.
It is a CNC machine-feeding application kit that delivers and stages parts to be placed into welding and fabricating equipment, as well as CNCs, grinders, vertical mills, and other machine tools and processes.
The Cobot Feeder demonstration will combine a UR10e cobot and the Flexxbotics FlexxCNC to control the process of loading and unloading trays into a pneumatic vise.
The modular and easily re-taskable Cobot Feeder empowers one machinist to do the work of up to eight machinists while increasing the amount of raw materials available to cobot machines tending work cells, said the companies.
About Universal Robots
Founded in 2005, Universal Robots said it is a leading provider of collaborative robots used across a wide range of industries and in education. The Odense, Denmark-based company introduced what it said was the world’s first commercially viable cobot in 2008.
Since then, Universal Robots has developed a product portfolio reflecting a range of reaches and payloads and has sold more than 75,000 cobots worldwide. The company said an extensive ecosystem has grown around its cobot technology offering innovation and choice for customers, as well as a wide range of components, kits, and solutions for various applications.
The Teradyne company has over 20 offices globally, with North American headquarters in Novi, Mich.
Editor's note: For more about FABTECH, visit Robotics 24/7's special coverage page.
Article topics
Email Sign Up
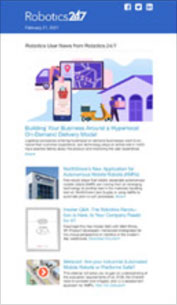
