Automation for unstructured picking and placing of parts into machines typically relies on computer vision, which often requires additional programming, according to Universal Robots ApS. This is necessary to bridge the gap from “pick” to “place” – especially if the “place” is not just dropping items into a box but accurately inserting parts into fixtures for further processing, said the company.
ActiNav combines real-time autonomous motion control, collaborative robots, vision, and sensor systems in one Application Kit to solve the random bin-picking challenge, claimed Universal Robots. To help manufacturers integrate ActiNav into machining cells, the Odense, Denmark-based cobot maker yesterday said it has vetted and chosen a limited group of systems integrators across the U.S.
“Our selection process focused on integrators with expertise in both vision and robotics, delivering superior value, and on-time/on-budget projects for customers,” stated Bryan Bird, regional sales director for Universal Robots’ North America division.
UR supplies ActiNav integrators
Universal Robots said it has provided its chosen systems integrators with in-house demonstration units, enabling them to quickly develop proofs of concepts for customers in their regions.
“Integrating ActiNav into a machining cell is where the expertise of the right systems integrator really shines,” said Bird. “Our integrators will be able to quickly handle all peripheral requirements such as integration with safety sensors, machine interfaces, end-of-arm tooling, and other components that all need to work together.”
Universal Robots named the following systems integrators:
- Eckhart Inc. in Warren, Mich
- Integro Technologies Corp. in Salisbury, N.C.
- Southwestern Production Technology Solutions in Coppell, Texas
- Cross Company in Greensboro, N.C.
Universal Robots said it expects to approve more integrators as ActiNav Solutions Providers in the U.S. and Canada by the end of the second quarter.
Eckhart was the first company to become an ActiNav Solutions Provider. “We look forward to delivering increased machine uptime, quality, and efficiency to manufacturers in our region,” said Sheldon Coney, director of robotics at Eckhart. “In many ways, ActiNav will set a new level of operational expectations regarding the future of intelligent systems.”
Machine tending case study
First launched in April 2020, numerous manufacturers seeking a simple solution to a complex problem have deployed ActiNav across North America, said Universal Robots. One of them was Flywheel Supply in Craig, Iowa. Flywheel Supply is a family-owned machine shop that produces about 29,000 unique metal parts for antique machinery, steam and boiler controls, valves, and gauges, for both industrial and government applications. The company moves a single UR5 cobot between an ActiNav automated bin picking application for machine tending and TIG welding applications to drive productivity and help the company compete nationally and globally.
“The only way that made sense for us to put a robot on a machine-tending application was to be able to do randomized bin picking,” explained Zach Northway, co-owner and lead project engineer at Flywheel Supply. “The cycle times on the machine are so short that if an operator has to stand there and line parts up in an organized fashion for a robot to pick them in a traditional sense, it would defeat the entire purpose of using the robot to begin with, because your operator is still standing there.”
In Flywheel’s ActiNav application, a UR5 cobot picks parts from a deep bin and places them in the jaws of a machine that indexes to multiple stations to perform tasks such as drilling, chamfering, and internal and external threading. Ultimately, the ActiNav system will process as many as 1,500 different part numbers, so it must be quickly programmable to pick parts of different shapes, sizes, and weights.
“The biggest advantage to ActiNav is that it can take randomization of parts being dumped in a bin, and as the bin gets low, a person can just come by and dump some more into the bin, and it will keep picking parts,” says Northway. “It doesn’t have to be reset, recalibrated—anything. It notices the bin amount changed, and it keeps on going.”
About Universal Robots
Universal Robots was founded in 2005 to make robotics more accessible. It said it developed small, user-friendly, reasonably priced, flexible collaborative robots that are safe for humans to work with. Since the first cobot was launched in 2008, the company has experienced considerable growth. It was acquired by Boston-based Teradyne Inc. in 2015. Universal Robots has regional offices in 19 countries, and in 2020, it had revenue of $219 million (U.S.).
Article topics
Email Sign Up
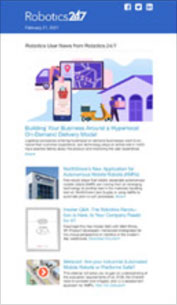
