Toposens GmbH last week said it has worked with Infineon Technologies AG to provide safety-critical 3D obstacle detection and collision avoidance in systems such as automated guided vehicles, or AGVs, using Toposens' proprietary 3D ultrasound technology.
“Making use of Infineon’s MEMS microphone, we were able to realize our new ultrasonic 3D sensor with a high overall sensitivity in the ultrasonic frequency spectrum, giving us the best range and widest opening angle,” said Tobias Bahnemann, co-founder and CEO of Toposens. “This enables our AGVs, robots, or other applications to avoid collisions with all kinds of obstacles, even in the harshest environments, as proven by the IP57 protection rating.”
Founded in 2015, Toposens employs experts in embedded systems, hardware development, 3D sensing, digital signal processing, and machine vision. The Munich, Germany-based company claimed that it has developed the world's first 3D ultrasonic sensor based on “bionic” principles, mimicking the echolocation techniques of a bat to deliver robust, low-cost, and precise near-range 3D data points.
Toposens, which has an office in Sunnyvale, Calif., said its clients include some of the world’s leading robotics and automotive companies.
Toposens promises reliable 3D sensing
Existing sensor technologies can be adversely affected by light conditions, reflections, and weather conditions. However, Toposens said its sensors rely on echolocation to generate real-time 3D point clouds. This can guide autonomous systems such as AGVs in even the most challenging conditions and allows consumer electronics to recognize their surroundings, it said.
Toposens' ultrasonic echolocation sensor enables 3D multi-object detection, which is critical for collision avoidance, according to the company. It is designed to be easy to integrate, with low calibration effort and high reliability, according to the company.
In addition, ultrasonic sensing reduces the high number of false positives and false negatives that can occur when using optical sensors and decrease the efficiency of the system. With data mapping and object-recognition software, Toposens said its sensor can provide precision and safety.
ECHO ONE DK incorporates Infineon microphone
Toponsens said its ECHO ONE DK sensor uses sound, machine vision, and advanced algorithms for accurate time-of-flight vision for applications such as robotics, autonomous driving, and consumer electronics. The ultrasonic sensor is based on Infineon's XENSIV MEMS (micro-electromechanical system) microphone IM73A135V01. Toposens is a member of Infineon’s partner ecosystem.
“Our XENSIV MEMS microphones enable the detection of sound pulses, so they are a critical component for 3D object localization via ultrasound,” said Dr. Roland Helm, vice president and head of the sensor product line at Infineon. “They offer a combination of exceptionally low noise and the highest SNR [signal-to-noise ratio] in the industry, resulting in improved reliability of the 3D data. This allows the detection of even the faintest ultrasonic echoes from distant, complex, and small objects.”
The next-generation reference product allows customers to reduce their development efforts and time-to-market. In addition, it is low-cost and energy-efficient compared with existing industrial 3D sensors and can improve AGV performance, said the companies.
Toposens said the new ECHO ONE DK platform a more flexible sensor for robot makers to evaluate for use in their products. For easy integration, the company offers CAN as a standard communication interface, and it can provide upon request.
Three software packages are available: a C++ library, Robot Operating System (ROS) support, and a cross-platform 3D data visualizer. In addition, a separate interface adapter is available for firmware updates.
Article topics
Email Sign Up
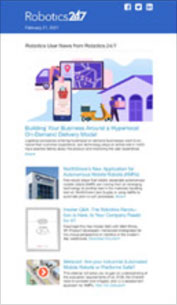
