Despite the hype surrounding smart glasses and augmented reality (AR), “vision” is not the holy grail of order picking in the distribution center.
Like other technologies that came before – RF, pick to light, voice picking – the value of this new technology will depend on how well it is applied to hands-on tasks in the DC.
In the end, smart engineers and processes will determine the extent to which smart glasses and AR can transform picking and other warehouse activities.
When Google released the first version of Google Glass in 2013, Lucas developers loaded our voice picking application and created a “vision picking” demo. Our conclusion was that the technology was not ready for prime time, and Google eventually shelved the original version of glass. Since then, smart glasses have roared back to life with new, more capable hardware from Google and other vendors (Vuzix, Recon, etc.) who are targeting industrial applications in manufacturing, supply chain and field service.
Today, there is little question that “vision” is the next big thing in manual picking technology, despite some obstacles to widespread adoption. Beyond hardware issues, there is also work to be done to fully integrate augmented reality within an optimized user workflow alongside scanning, voice and other technologies.
These are manageable challenges. But anyone expecting vision alone to transform labor productivity and accuracy will be disappointed. As with any new user technology, the real driver for operational improvement from vision will come from better process and workflow design – that is, process changes “beyond the pick face.”
To understand the connection between process design and technology benefits, consider how voice picking has impacted the DC over the past 20 years. Thousands of DCs use voice-directed picking today, but our experience shows that different facilities realize vastly different productivity (and accuracy) gains with the technology. Among Lucas customers using voice picking, the average productivity gain from voice is 36%, and the range is from the low double digits to greater than 100%.
The disparate productivity results are a direct byproduct of the approach or strategy a given DC follows when implementing the technology. We categorize three main approaches to adopting any new user technology: technology enablement; workflow improvement; and process optimization. Each approach delivers a different scale of benefit.
Technology Enablement
In this approach, a DC implements a new technology (voice, vision, etc.) as a direct substitute for older technologies within an existing workflow. For example, you can substitute a heads-up display for a device display in a traditional WMS-directed RF process, and replace manual barcode scans and key entry on a handheld or wearable RF device with speech input and barcode captured by the user’s smart glasses.
Productivity gains resulting from eliminating the time spent stopping to read device screens, pausing to handle a scanner, or slowing down to key-enter data or press function keys. This strategy mostly impacts the efficiency of activities performed at the pick-face, saving seconds per pick.
Workflow Improvement
To achieve additional productivity gains, DCs can make other changes to their current workflow to eliminate wasted time and unproductive steps in the process. In addition to substituting smart glasses and vision recognition for device screens and key taps, you can condense or combine process steps and change other aspects of the process flow, streamline exception processes (which are extraordinarily time-consuming), and reduce the time workers spend doing tasks ancillary to the main workflow.
These changes can save additional seconds per pick, eliminate unproductive minutes at the start or end of picking assignments, and make the end-to-end process easier and more accurate. When combined with the benefits of technology enablement, this strategy typically results in gains in the range of 20%.
Process Optimization
To get more dramatic levels of efficiency, DCs will often redesign and optimize their processes as they implement a new user technology. Common examples include zone picking, batch picking, two-stage picking (especially for slower-moving items), task interleaving, and bucket-brigade picking.
Going a step further, many DCs are applying advanced optimization algorithms to increase pick density and reduce travel in new or existing batch picking operations. Many of these types of optimizations are independent of the technology being introduced to users, but for many DCs the introduction of a new technology represents a catalyst for these types of process changes.
As a final point, many DCs find that they are unable to implement workflow improvements in their current process due to the inflexibility of their back-end systems, putting their entire technology ROI in jeopardy. In such cases, it is worth considering how a discrete picking or work execution system can offer greater process flexibility without requiring a wholesale replacement of larger, critical systems.
To net it all out, vision picking is great, but the value of the technology to any operation is limited unless you are able to leverage it as part of a wider process improvement activity. So by all means, look to vision, smart glasses and other wearable technologies to make work easier, faster and better for your workers. But recognize that smart engineers and process design is more important than any technology.
Related Lucas Systems Resources
Article topics
Email Sign Up
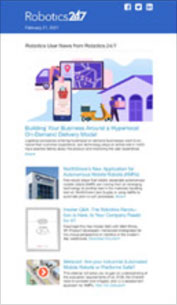
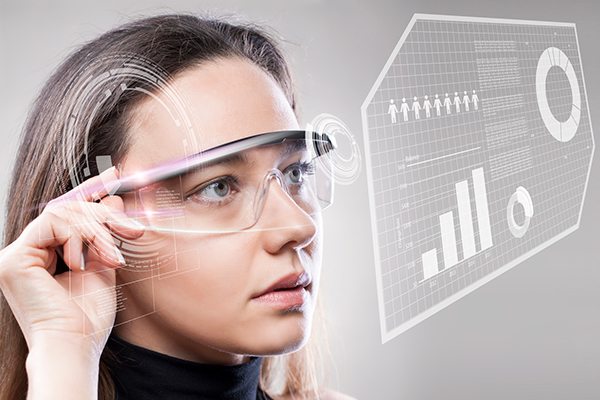