The system integration landscape has completely transformed in the last decade, and the pace of innovation will only increase. Heightened demands from consumers and business partners alike have driven rapid adoption of automation and software in the materials handling and logistics space as companies strive to overcome the limitations of legacy systems and methods. The complexity of the modern fulfillment system and broader supply chain pose significant challenges to end-users and solution providers, both of which can no longer afford to remain complacent in their processes and performance.
Aside from constant change, it’s uncertain what the future holds. As a result, the art and science of system integration have set their sights on what is next for each facility, rather than reviewing after-the-fact reports of what went wrong and why. By definition, the push for predictive analytics must include some predictions about enabling technologies that might come along to augment—or disrupt— each system.
Modern talked to four experts who together represent a global perspective on current and future trends in system integration: Mike Khodl, vice president of solution development at Dematic; Kevin Roach, executive vice president and general manager at Intelligrated Software; Bill Leber, director of business development for Swisslog; and Joe Hutter, senior vice president of business development for Wynright. Over the next few pages, they offer their insights into trends in system integration and share practical advice for how end-users can ensure a successful outcome before, during and after an implementation.
Modern: What trends are driving your customers to automate? What is keeping them up at night?
Khodl: The complexity of system integration has gone up significantly, and it doesn’t have to be highly automated to be complex. Three major trends are driving innovation: increasing productivity, reliable labor availability, and reliability of peak-to-average performance. Some are preparing well for peaks, some are not. For most, their core competency is not distribution, it’s making a widget everyone wants. This is more volatile in the e-commerce space when you launch a product and immediately get 250,000 orders. In the general merchandising and e-commerce world, lighter, smaller envelopes and parcels drive a big impact to the mechatronic layer. From a development and advancement perspective, there’s a lot going on there.
Our perspective on design solutions for e-commerce and omni-channel is that they should be flexible to meet business needs, scalable to enable growth, and modular so we’re not reinventing the wheel. A lot of people are asking how to convert and modernize and optimize.
Hutter: The main drivers for automation involve the online portion of omnichannel capabilities. The characteristics of those orders have a more pronounced impact because more orders are going through the system. These are not new elements, new forces or drivers, but they are becoming more pronounced.
Another element is the significant variation in order profiles from season to season or day to day. Whether single- or multi-line orders, each type has dramatically different work content and the percent share of each can vary. You can’t do one or the other; you need to address both. Another key driver is that peak volumes are more pronounced, and we’ve seen peak-to-average ratios of 20 to 1 or more.
Leber: SKU proliferation is a huge driver, and every single business is going through this. But the No. 1 thing driving automation is continued mass customization, and if you don’t deliver what the customer wants, they will go somewhere else.
The scope of integration has become more broad-based and is much more interactive. Customers are asking us for condition monitoring and expect us to be there 24/7 so systems are up and running all the time. The support aspect is a big topic with everything these days, and pushes us to anticipate problems and handle changes. According to Gartner’s hype cycle, predictive analytics went from the “plateau of productivity” to off the chart, and is now just a normal thing to talk about.
Customers have to take a different look at how they invest in their systems. Current conditions require a leap of faith and the willingness to look out five years. The supplier community struggles, too, since historically we had to have such an intense focus on the subsystems. That sometimes blocks your ability to see the bigger picture. Because systems take such a long time to implement—30- to 50-week schedules—you can be sure the business snapshot has changed in that time. Suppliers and customers can get so fixated on delivering what was promised, they don’t necessarily consider if that goal is still applicable.
Modern: What is changing about the automated systems being designed today? And what are end users trying to accomplish that is different from what they tried to accomplish five years ago?
Hutter: Whether a retrofit or greenfield facility, it’s important to look at the big blocks of work performed in e-commerce: receiving, storage, picking and finalization. Especially in a brownfield environment, finalization is a good target for automation. There are lots of opportunities there, such as the final sort to order level, buffering, value-added services (VAS), packing, print and apply, and shipping.
System designs are very data-driven to give an accurate and detailed description of how order flow gets executed and what the streams of work are as the system processes orders throughout the day. There are then tools to emulate, simulate and validate those designs. This includes defining the places where the system could “break” in response to peaks or other variables.
Analytics, robotics, connected supply chains and enabled workers are changing the landscape of system design. Analytics are helping users understand how to make more accurate operational decisions. Robotics are supplementing and driving new technology initiatives within organizations. Users are requiring the supply chain to provide a fully connected experience from the mobile application to the store and to the warehouse, enabling users to have full visibility into their orders.
Leber: We recently had a meeting with a Fortune 50 company and 30 of their engineers. They were challenged to come up with a comprehensive system, and while 40% of the discussion involved machinery and controls, 60% centered on software. They have major enterprise resource planning (ERP) systems, but the subsystems are highly optimized. When they move to a next-gen platform, they have to deal with all those subsystems. Once they do, they will find they are more efficient and responsive.
Look at the navigation function on a smart phone. It can you show where traffic is backed up 100 miles ahead and allow you to plan a detour. It’s tapping the GPS of all those other drivers to see which ones are slow. We’re doing the same thing for material flow. For complex systems handling thousands of orders per hour, predicting and preventing bottlenecks adds a lot of value.
Modern: What is the importance of software in today’s distribution center and factory? And what kinds of data are customers asking for that they didn’t ask for in the past?
Roach: Mark Andreessen wrote Mosaic, the first graphical browser for the Internet before co-founding Netscape. He was quoted a few years ago as saying “software is eating the world.” Software is transforming the world industry by industry and changing the entire shape, view and capability of each. Travel agencies, books, movies, advertising, real estate, taxis, recruiting, have all been eaten by software. It’s now clear that software is also going to “eat” the materials handling world.
The materials handling, supply chain and logistics space is frankly behind other industries by 10 or 20 years. This space used to be filled with very customized, one-off software solutions. You used to buy a factory, commission it, and it stayed the same forever. Now companies want to stay current, benefit from suppliers’ ongoing research and development, and consume software updates in a low-risk, non-invasive fashion so they can continue to make operations smarter every day.
All industries evolve from point solutions. They build applications to solve a problem, then they have to tie it all together. As a result, about 40% of system integration costs is IT to unite disparate components. Users are attempting to capture real-time system data to enable proactive actions versus reactive measures and are expecting their equipment and software to become a singular entity that enables them to visualize their data. The days of excel spreadsheet exports and crunching system data is approaching an end. Going forward, suites of integrated, modular and scalable solutions for receiving, picking, routing, replenishment, slotting or pick modules will serve small businesses and multi-national enterprises.
Khodl: It’s all about the software play in a retrofit. You might use 15-year-old hardware, but change the warehouse control system (WCS) or warehouse execution system (WES) and you get more productivity. Of course this is much less expensive than building a new building. It’s possible to increase productivity by 25% with the same physical assets, and you can reduce the need to flex the workforce if you can scale.
Software can inform facility layout, replacing the old-school view of an execution system in one place and something else managing orders. Today software is order management for all of it, including orders, planning, execution and optimization layers. The line of demarcation between warehouse management systems (WMS), ERP and WCS is blurring.
Software is essential for optimizing labor, equipment and peak performance, and can improve productivity by 25% when added to legacy hardware.
Software also blends materials handling equipment and operational data, mixing automation with humans for optimal results. Today, we track labor productivity at a pick module, say, 180 picks per hour per person, so if we need X picks we need Y people. What if half of that work was done with robots? It will need to be managed differently. Then there’s the connectivity element that allows you to know the exact location of a robot, which is not necessarily the case with human workers.
Hutter: It’s not a new sentiment, but WCS and WES are essential to provide overarching information systems to manage automated materials handling systems. Ultimately, the goal is predictive analytics.
Mobility and visibility allow operators on the floor to see the current workload and determine, for instance, if they will be able to maintain wave integrity to meet truck loadout times. If you are projected to miss a truck loadout, you can drill down to the wave and zone that’s lagging, which will direct workers to help complete the wave.
Modern: Robotics. Internet of Things (IoT). Mobility. Wearable. Digital distribution. Which of these buzzwords, if any, are your customers asking about? Which do you think will have the most impact on warehouse, distribution and materials handling in the plant in the next five years?
Hutter: I would almost rank these in order: robotics, Internet of Things, mobility, wearable, digital distribution. Robotics are not new, but in materials handling, it’s the new frontier. With the available technology, perception capabilities and falling price point, it’s almost a bonanza.
The new things we’re looking at are robotics-related, including perception technology like robotic truck loading and unloading. As those become a reality, we’re taking that and applying to other areas like a mobile full case order fulfillment robot, something that scans and realizes what objects are so it can effectively handle them. It’s the idea of getting the robot to the work instead of the other way around.
Khodl: It’s all about the blending of automation and connectivity, whether robots, intelligent control modules, Bluetooth, IoT, wearable or smart devices. How do we blend these into the operation and blend them with human capabilities? How that comes together is unclear right now, but there are big opportunities.
Leber: Robotics combined with IoT, and robot/human collaboration are hot topics. These get into safety and beyond technology challenges into legality issues. But flexible mobile robots and vision technology will get us to a place in a couple of years where a robot with vision can do 80% of picking and packing, then collaborate with a human for the last 20%. That’s the hot future.
Companies Mentioned in this article:
Dematic
Intelligrated Software
Swisslog
Wynright Corporation
About the Author
Follow Robotics 24/7 on Linkedin
About the Author
Follow Robotics 24/7 on Linkedin
Article topics
Email Sign Up
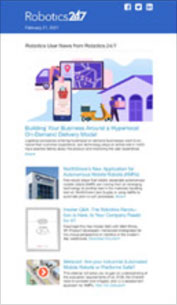