The German Aerospace Centre (Das Deutsche Zentrum für Luft- und Raumfahrt e.V.) is using Stratasys FDM 3D printing for the production of a fully-working prototype of ‘TransRoPorter’ (TRP).

TransRoPorter, built at the Institute for Robotics and Mechatronics (Institut für Robotik und Mechatronik), is an exploration robot designed for unmanned flights to Mars and set for launch in four to five years. To successfully explore Mars with a robot, design and functionality are key factors to meeting the objectives of the mission. Using a Stratasys Fortus 900mc Production 3D Printer, the research team 3D printed a working prototype, significantly reducing production times compared to traditional methods, according to a press release. This enables the team to test the design and functionality of the robot under simulated extreme conditions ahead of time.
Dr. Kaj Fuehrer, Head of System Building Technology South (Leiter Systemhaus Technik Süd), is developing and testing the 3D printed robot prototype together with his colleagues Dr. Stefano Seriani und Dr. Armin Wedler. The TransRoPorter is made from two components: the moveable TRP Rover-Unit, made to navigate in unstructured terrain, and the Payload-Module (PM), which carries spare parts, communication technology and scientific tools. To ensure functionality and practicality of the 3D printed prototype, rigorous testing is required.
Fast Production
In developing the TransRoPorter prototype, it is essential for the part to fit the design, be customized to exact specifications and have specific material properties. “For us it was clear, a prototype made out of metal was too expensive and complex in production,” explained Dr. Fuehrer in the press release. Therefore the team decided on a 3D printed prototype, which is not only produced faster than the alternative out of metal, but also with less associated costs. The metal alternative also needs to be finished post-production – more work with additional costs.“In the planning of this project, we always preferred 3D printing technology,” he said. “It became evident to us that using 3D printing for the production of the TransRoPorter was truly the least expensive, fastest and most elegant solution. Everyone involved in the project is delighted with the outcome.”
Optimizing Functionality with 3D Printing
In addition to the time and cost savings, the functionality of the prototype was critical to Dr. Fuehrer and his team. “Our prototypes are often very complex and typically push the boundaries of what is possible,” said Dr. Fuehrer. “Therefore, it is important to choose the appropriate production method and material, so that we can achieve the desired functionality without any limitations.”Using the Stratasys Fortus900mc Production 3D Printer, the research team are 3D printing large parts in FDM thermoplastic materials. According to Dr. Fuehrer, the ASA material was suited for testing the TransRoPorter prototype, enabling the team to produce a strong enough Box to contain all the technology safely within.
“It was extremely important that the fit was right, that the box could be mounted to the tracks and the docking port worked,” he said. “Utilizing Stratasys FDM 3D printing technology, we found that the material basically has no distortion. The decision for ASA material was consciously made, as it is ideal for our purposes and handling.”
Seriani added: “The stability of the ASA material also played a large role for us. We needed a fully functional prototype that could perform in all tests and withstand the strain of the design. The tough and rigid properties of the Stratasys material were therefore an ideal fit to test the TransRoPorter’s functionality for its journey to Mars.”
According to Dr. Fuehrer, 3D printing also supports other strategic goals. “A new technology leads to new thought processes. Over the past few years, many colleagues are already thinking in 3D and are involving additive manufacturing into plans for other projects they are starting with,” he said. “This new knowledge has opened them up to a new set of possibilities within product development.”
For more information, visit Stratasys Ltd.
Source: Press release provided by the company.
Article topics
Email Sign Up
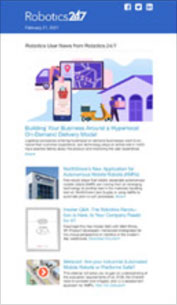
