In some industries, like commercial aviation, remote monitoring has been around for years.
Every time you get on a Boeing aircraft, there’s a good chance that Boeing is keeping tabs on what’s happening during that flight, while GE Aviation monitors the engines and a third-party maintenance provider collects performance data used to schedule repairs.
It’s become a commonplace, mature technology.
Stand-Alone Automated Equipment
Muller LCS, a manufacturer of stretch wrap equipment, recently added a remote monitoring offering to its line of high-speed, high-volume Octopus rotary ring stretch wrap machines. The service, says Neil Weisensel, brand and marketing director, grew from the company’s desire to provide more information to customers on a daily or hourly basis - an expansion of on-site quarterly or monthly equipment audits conducted by Muller technicians.
“On-site audits include checking the film pre-stretch level to determine that the film cost per load meets the standard operating parameters set by the customer,” he explains. “However, the audit only provides a snapshot of that moment, whereas remote monitoring collects multiple data points continuously and in real time.”
The service (and the Octopus stretch wrapper) targets operations with two to 20 production lines, each served by a machine unitizing 20 or more loads per hour for eight or more hours a day. It monitors pre-stretch settings, the number of wrap revolutions per load, film breaks and downtime.
“Repeated film breaks in a high-speed food and beverage operation, for example, causes downtime that equates to more than $100 lost per minute,” he says. “Adding predictive maintenance to the monitoring allows us to proactively schedule repairs in advance.”
Further, notes Weisensel, a dip in film pre-stretch level wouldn’t be obvious visually. “You won’t know the film is underperforming until the product ships and is damaged in transit; remote monitoring allows us to alert an operation of such a condition.”
OPEX Material Handling’s engineering team has always monitored its Perfect Pick robotic goods-to-person picking technology installations remotely as part of its service and support, says Jeff Hedges, president. The company is currently developing a remote monitoring tool for customer use as well.
“Remote monitoring services are a natural extension of our company’s all-inclusive service and support contracts, which have been designed to eliminate surprises ranging from unplanned downtime to unexpected costs,” says Hedges. “We expect that in the future some customers will elect to ‘self-maintain’ their systems, which will be much easier for them with access to our remote monitoring service option.”
For companies that prefer to hire technicians on-site, OPEX will train them on how to maintain and service the equipment. But given the current challenges faced by the industry in finding enough qualified service technicians, it’s typically more economical to sign a service contract, Hedges adds.
“Whether an operation has an internal service team or not, management still wants to be able to rely on their original equipment manufacturer for support,” adds Tim Buhr, director of field service who oversees OPEX’s service and support network. “Having access to that real-time information helps us evolve preventive maintenance tasks to a more of predictive maintenance task.”
Article topics
Email Sign Up
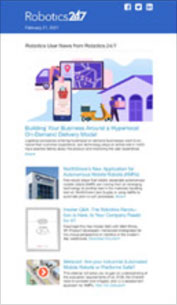
