There are pros and cons for each of the warehouse picking methodologies chosen for fulfillment operations. Zone picking is ideal for very large operations where pickers must travel long distances to complete an order or for smaller sites with very high order volume where congestion is an issue.
A common challenge associated with zone picking is predicting where your associates will need to be based on inventory slotting and the order pool for the day.
Incorrectly predicting zones results in overworking some associates while others wait around with nothing to do.
Armed with knowledge of this challenge, we tackled the question: what if you could reap the benefits of zone picking without the challenge of analyzing inventory slotting, consumer demand and labor availability? Our solution: dynamic zoning.
First, let’s understand the methodology we consider behind using static zones within a warehouse.
Why are zones used?
In order to meet SLAs and maintain profitability, there is a constant pressure to keep a fulfillment operation running efficiently. Enabling associates to spend more time picking products and less time walking from one place to another is an area ripe for optimization.
Although collaborative mobile robots eliminate long, unnecessary walks to deliver and receive work, they do not remove walking between picks. One technique to alleviate unnecessary walking is to break the picking area into zones and assign associates to stay within them. This can be especially effective if there are sparse picks over a large area.
What are the challenges of using zones?
There are two interrelated problems that often cause zones to be less effective than operators hope: defining zone areas and labor balancing.
Zone areas are set with the intent to evenly distribute work and ideally put common clusters of work in one area. The problem is that it is extraordinarily difficult to predict commonly clustered SKUs. Order profiles are constantly changing over time – from season to season and even over the course of the day. We often see warehouses that have been broken into zones based on physical size and then never adjusted again.
The second related problem is labor balancing. Over the course of a shift, an operator wants their associates to spend as much time as possible actively picking rather than traveling from one pick to the next or, even worse, idle. So, when utilizing a zone picking method, it’s best when the orders are evenly distributed across all zones so each associate is engaged.
Unfortunately, this rarely happens – there are often drastically different work loads across zones. To mitigate this, managers need to constantly monitor order volumes and make adjustments to zone assignments on the fly. Although we have some operations that want to use zones, most of our operations decided that there were too many inefficiencies and overhead managing them to make them beneficial.
The Solution: Dynamic Zones
Analyzing our customers’ needs, we have devised an innovative solution that reaps all of the benefits of traditional zones with none of the drawbacks. We call this dynamic zoning; here’s how it works:
When an associate completes a pick and is preparing to travel to the next, 6 River Systems’ intelligent allocation system calculates how much time it will take for the associate to get to the new pick.
It also calculates how long it will take the current associate to meet another robot and a new associate to meet the current robot. If it ever takes less time to do this handoff, it is performed and time is saved. It has exactly the same benefit as if a perfect zone was created for this batch of orders.
Figuring out ideal zone boundaries is no longer a problem; there are no fixed zone boundaries! The 6RS software effectively determines the perfect zone for each robot without any operator intervention.
There is no need for labor balancing – we do that automatically. With dynamic zones, there are never associates waiting for work. As soon as an associate completes work with a robot, it leaves for the new “zone” and the associate can meet the next waiting robot. We have already determined there is one that is available for them.
Summary
Traditional static zones can be an effective technique to increase productivity and it is a methodology that 6 River Systems has supported for years. However, it does have its shortcomings so we designed a superior solution: dynamic zoning, which is just one of many innovations that we offer to our customers.
Related Resource
The Current State of Labor in Supply Chain and Logistics
New research highlights the labor strategies warehouse and distribution center operators can utilize to achieve fulfillment excellence. Download Now!
Article topics
Email Sign Up
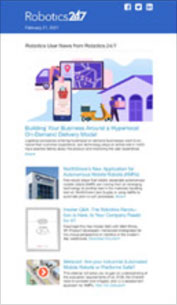
