Despite advances, the architecture, engineering, and construction industries still face the challenge of slow and costly manufacture of large components, according to SAEKI Robotics AG. The Lupfig, Switzerland-based company yesterday launched from stealth with $2.3 million in seed funding. It said it plans to create automated plants using industrial robots and 3D printing to build everything from aircraft wings to construction site installations.
ETH Zurich researchers Andrea Perissinotto, Oliver Harley, and Matthias Leschok applied their expertise in robotics, engineering, and fabrication to found SAEKI in 2021. During their studies and industry collaborations, the trio said they identified the need to scale up additive manufacturing (AM) processes for large-scale applications such as bespoke concrete formwork.
“Currently, to develop a lightweight carbon-fiber element or to build a topologically optimized concrete floor slab, buyers would have to wait months and spend vast sums of money to receive a first sample and only then build a prototype, let alone consider reiterating for any flaws,” said SAEKI's founders in a release.
“With SAEKI, this bottleneck is removed, enabling buyers to rapidly innovate and grow their services and offerings in ways they have not been able to before,” they said. “Indeed, for large-scale items, this has not been previously possible.”
3D printing complex formwork with large robots
Perissinotto, Harley, and Leschok said they have worked closely with architectural design, engineering design, and construction services customers to understand their challenges and tailor “microfactories” to their specific needs. Their stated goal is to turn complex designs into reality, save concrete, and reduce carbon dioxide emissions.
SAEKI explained that by combining 3D printing and milling with large industrial robots, it can print formwork up to many meters in length efficiently.
“When it comes to design complexity, the opportunity is unlimited,” the company claimed.
SAEKI combines AM with CNC methods to finish products without time- and cost-intensive post-processing, such as surface treatment. It has developed a large-scale automated digital fabrication, or “dfab,” cell of more than 4 cubic meters (141.2 cubic feet).
The dfab cell includes an industrial robot, tool-changing equipment, and software for a “user-friendly design-to-product workflow,” said SAEKI.
Venture Kick helped launch startup
SAEKI won Venture Kick Stage 2 in 2022.
“We joined the program as engineers and left as entrepreneurs; Venture Kick made the leap possible,” said Perissinotto, co-founder and CEO of SAEKI. “Their guidance, workshops, and mentorship were invaluable, helping us take SAEKI from vision to reality.”
Wingman Ventures led the company's seed funding round, with participation from Vento Ventures, Getty Capital, and angel investors.
SAEKI builds first production hub
SAEKI said its first production hub will be the blueprint for further expansion. The company asserted that it will solve manufacturing problems and enable progress “in an industry bottlenecked by manual processes.”
The production hub will offer industrial robots built by SAEKI that combine digital manufacturing methods such as AM, milling, and inspection to create an “all-in-one, low-waste production process and recyclable materials.” The company said its robotic microfactories will be self-contained units able to do all the steps of manufacturing and easily deployable for localized production.
In addition, SAEKI said it plans to offer a quoting platform tailored to the customers' business needs to eliminate the “complex opaque approach currently in the market.” It will offer production in a robotics-as-a-service (RaaS) model.
“SAEKI is building a platform that will allow its customers to transcend the limits of traditional manufacturing, where size, complexity, and efficiency are no longer obstacles but catalysts for progress,” wrote Rita Longobardi, communications manager at Venturelab. “In doing so, SAEKI envisions a network of decentralized, robot-operated production hubs around the world.”
Article topics
Email Sign Up
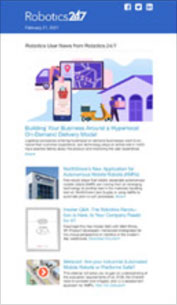
