Almost 100 years ago, the word “robot” and the concept of machines working for people was introduced in the play “Rossum’s Universal Robots.” While the play doesn’t end well for people because the robots rise up and wipe out the human race, some say it set the stage for modern robotic solutions.
Today, robots are certainly changing the way we move materials. “When we look at how product moves, we see that robots can play a part in helping the flow of product through the entire supply chain,” says Tim DeRosett, director of marketing for the Motoman Robotics division of Yaskawa America.
Robotic solutions embody a variety of components, configurations and capabilities. And, they can be programmed to perform predictably, accurately and rapidly. “A robot is something that can perform a task without human intervention,” explains Mark Longacre, marketing manager for JBT Corp. “And if maintained and applied properly, a robot of any design can run around the clock.”
Since people cannot easily run around the clock, the need for efficiency is driving companies to look toward automation, says Ken Ruehrdanz, warehousing and distribution market manager for Dematic. And, since labor has a dramatic impact on an operation’s bottom line, automating certain tasks is one way to reduce cost while keeping an operation running efficiently.
The push toward efficiency is reflected, in part, by the increase in robotic applications in the materials handling sector. According to the Robotic Industries Association (RIA), robotic applications in the materials handling sector grew 28% in 2011. This increase included a combination of autonomous mobile robotic solutions and fixed robots used for loading and unloading product.
Here’s a look at how autonomous, piece picking, and palletizing robotic solutions are picking up the pace for end users inside the four walls.
Autonomous mobile robotic solutions
Autonomous mobile robotic solutions are enhancing lean manufacturing processes by shuttling work-in-process and finished goods between locations. “Robots have played a major role in leaning manufacturing processes in production facilities, feeding product to the lines,” says John Dulchinos, president and CEO at Adept Technology and chair of the RIA’s Statistics Committee.
While these autonomous mobile robotic solutions have taken extra steps out the manufacturing process, the newest intelligent autonomous mobile robotic solutions are able to move goods independently, randomly and dynamically, and are starting to play a bigger role in warehouses and DCs.
Compared to mobile solutions that are guided by wires or follow magnetic tape paths, the newest incarnation of autonomous mobile robots move independently, making decisions on the fly. “It’s like the city bus versus the taxi cab. The bus moves around using a predefined route and doesn’t deviate from the path. The taxi, however, figures out on its own the best way to reach the final destination. You tell the robot where to go and it will go there because it knows the lay of the land,” says Dulchinos.
It knows the lay of the land because the information about the work area is gained by walking the robot around and mapping the facility or by programming the information into its computer system. Odometers, lasers and other technology allow it to know where it is at all times and avoid impact with people and pallet rack.
Each robot is connected to the operation’s network, so like the dispatcher, the system knows where every robot is, what it’s doing and where product is at all times. This information provides the flexibility to reallocate a unit at any time.
Robotic piece picking
While mobile robotic solutions deliver product in a goods-to-person operation, stationary robots are able to receive product for piece picking operations.
In one example of a “goods-to-robot” solution, a spider style robot can perform extremely rapid pick and place function, sometimes as fast as 2,400 pieces per hour. According to Ross Halket, Schaefer Systems’ director of automated systems, this technology has been around for years, but the difference now is the advanced software that controls the sequencing and the vision technology that enables accuracy in the pick.
“The first critical part of the process is to drive the SKU in the right speed and the right sequence to the robot cell so it has what it needs when it needs it,” says Halket. “The second critical step is for the robot to see that it’s picking the right SKU.”
In this case, product is delivered to the robotic picking system in totes from an automated storage system. A laser identifier recognizes the product, its position in the tray, and the optimal center of gravity for picking. Then, the vision technology confirms and processes the information, then makes a picking decision. The robot’s end effector lifts the product from the tray and drops into an order tote or picking buffer.
This is a good e-commerce solution, says Halket, especially for retailers that faced challenges getting into that end of the business because their original systems weren’t designed for small orders. For these robots, shapes and sizes don’t matter; it’s the weight that determines what’s pickable. If an end user is handling products at both ends of the scale, another picking cell can be added to lift heavier items with a different end effector.
In a different approach to picking, an articulated arm robot, which is programmed to know the cubic characteristics of each item, directs its robotic arm to grip the selected product, lift it and strategically place it into the order container or shipping carton. These types of robots are able to perform about 450 picks and defined placements in an hour.
In this application, product is “smartly” placed into the shipping container so it doesn’t have to be manually adjusted further down in the picking process, explains Bill Ostermeyer, vice president of sales for viastore. Because the system is programmed with sizes and dimensions of product and containers, the robot can strategically place an item into a container, making the best use of the available space.
While these spider and articulated arm robotic picking solutions vary in application and speed, they have common features. Both robots are fully automated solutions that are integrated with automated storage systems that provide a constant supply of product. Additionally, both approaches can support a multi-order process, which means they can pick different orders from one container.
Another common denominator is end-of-arm tooling, also known as end effectors. These devices have sensors that enable the robot to locate products—and hardware like vacuums or gripping clamps to lift it.
Like a power drill with changeable bits, similarly you can take off one end effector type and attach another, says Dematic’s Ruehrdanz, depending on the product being handled and the gripping strength needed. For example, cartons of lightweight, fragile light bulbs require a different gripping strength than books. Or, end effectors that handle rigid cartons would be different than those handling products packaged in bags.
Robotic palletizing
Once orders are filled and product is packed into shipping containers, they have to be palletized for shipping out to customers—and robots can also have a hand in the palletizing process.
Simply building a pallet isn’t enough. “The basis of everything is building a pallet as close to store ready as possible,” says Brian Duncan, executive account manager at Schaefer Systems.
The challenge in building store-ready pallets is that robot solutions have to recognize the various sizes and dimensions of multiple SKUs and understand the various customer stacking rules, says Brian Keiger, logistics account manager for Kuka Systems.
One way to build a store-ready pallet that addresses the customer’s staking rules is with a pack pattern generator software tool that builds a virtual pallet before the robot touches or moves anything. The system plans the sequencing of product upfront using a number of regulators like weight and crushability, for example. When the optimal pallet is planned, then product is sequenced to the robotic palletizer.
Gantry robots are one type of solution being used in the warehouse for palletizing. A gantry robot is a bridge-like structure that moves horizontally on overhead tracks that can span large areas. The gantry’s end effector lifts and transports product to its target conveyor for palletizing.
Overall, robotic case and layer picking applications are gaining traction across many industries, says Derek Rickard, distribution systems manager at RMT Robotics. “It doesn’t matter to the equipment what the SKU is, what matters is the size, weight and shape of the product. Pallet building is all about geometry. The commonality of packages lets you build pallets, and the combination of clamping tools and vacuum technology lets us pick up virtually anything.”
In addition to picking up and palletizing all types of items, robotic palletizers can do it faster and more efficiently than people. Not only can robots build about 700 pallets per hour, they build them 35% denser than manually built pallets, which packs out trucks better, saves on freight and results in less damage, loss and worker injury.
Robots down the road
Once operations had a choice between people and fixed materials handling solutions to move product; today, new robotic technology is giving end users more flexible options.
“People are good at working through problems, but not as good at highly repetitive tasks; robotics are good at repetitive tasks, but not as good at solving problems,” says Motoman’s DeRosett.
As a result, he envisions a future in which people and robots work side by side. “It’s exciting to look at a robot as an assistant to a person. We’re not there yet, but given enough time and resources we’ll get there—as long as we have real problems that need to be solved.”
The robots are coming
Robotic materials handling technology is changing the way we move products in the plant and the distribution center.
About the Author

Follow Robotics 24/7 on Linkedin
About the Author

Follow Robotics 24/7 on Linkedin
Article topics
Email Sign Up
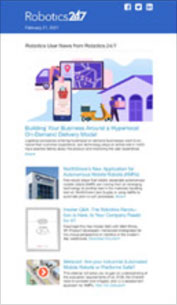