A report recently issued by San Francisco-based real estate investment trust company Prologis took a deep dive into how “automation has the power to revolutionize logistics operations.
The report, entitled “Automation and Logistics Real Estate #1: The State of Automation in Supply Chains,” highlighted three trends that the firm said will lead to higher levels of automation in Prologis’s facilities.
The trends cited in the report included: the ongoing COVID-19 pandemic leading to greater absenteeism and further stressing labor availability; technology continuing to improve, expand capabilities and reduce costs; and labor-intensive operations, notably e-commerce, growing quickly.
Even though the benefits of automation are evident, the report pointed out that automation adoption are in logistics facilities are limited, due to various factors, including high costs, low flexibility, and slow ROI, adding that move-in costs for fully automated facilities are four-to-five times higher than no-to-low automation move-in costs.
Despite these challenges, though, Melinda McLaughlin, Prologis, vice president of research, explained that buy-in is already increasing.
“Today’s automation companies are leveraging better technology to provide more flexible solutions, which then can reduce costs and accelerate the return-on-investment,” she said.
Another observation made in the report pointed to how automation is concentrated in e-fulfillment, as e-commerce is three times more labor intensive compared to traditional logistics operations and its sales are twice as volatile compared to brick-and-mortar retail. And it added that it is a fast-growing segment, which, in turn, makes it a “desirable target for investments that can improve labor productivity and smooth out peaks.”
McLaughlin noted that a few reasons that e-fulfillment and e-commerce are three times more labor intensive compared to traditional logistics operations.
This includes working through unique orders picked, packed and quickly shipped parcel-by-parcel creating the need for more employees, relative to traditional operations that consist of processing pallets of uniform goods, she said.
With the Prologis report stating that automation adoption is “low but rising.” coupled with the need to quickly get goods to consumers, McLaughlin said that will impact how it is addressed in the coming years.
“As mentioned in the paper, the case for automation became even more compelling in 2020 as the e-commerce evolution accelerated and labor became even harder to secure,” said McLaughlin. “Tomorrow’s supply chain will need to be more resilient, more dynamic, and offer higher service, in the form of faster delivery times and broader product variety. Automation is just one tool that can be used to help meet these needs, and we expect that more flexible automation will help drive adoption going forward. As automation lessens the role of labor availability on location choice, users can locate in the best location for their supply chain needs, and for many, that will be in areas close to end consumers.”
In terms of how automation is changing logistics real estate requirements, the report offered up three ways in which that is happening, including:
- automation enables greater choice in location, and most types can be incorporated into any modern facility;
- physical requirements for automation are not changing the rate of functional obsolescence; and
- automation opens up new and more productive locations
About the Author
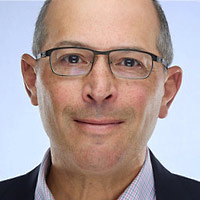
Follow Robotics 24/7 on Linkedin
Article topics
Email Sign Up
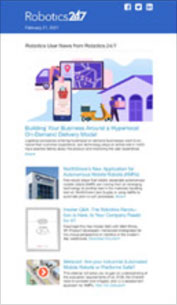
