Greif, in Alsip, Ill., manufactures steel drums and covers in all sizes to transport materials for the chemical, paint, food, pharmaceutical and hazardous waste industries.
When the company began looking for an automated system to replace the manual process of palletizing empty drums, its goal was to improve production efficiency and equipment reliability, while also improving safety and ergonomics for Grief’s workers.
To satisfy its multiple requirements, Greif chose a robotic palletizing system (Lambert Material Handling, http://www.lambertpalletizers.com). In addition to the robot, the customized palletizing system includes end-of-arm tooling, a pallet dispensing system, drum conveyors and pallet conveyors, which were designed and manufactured by the system integrator that also programmed the system to perform Greif’s specific function.
Here’s how it works: Chain-driven live roller conveyor delivers pallet stacks to a dispensing system that sizes the stack and separates individual pallets to be fed into the palletizing area. Coming from the upstream operation, 20 drums per minute are conveyed to a drum orientation station where they are rotated and properly positioned for automatic filling in end user operation. At the robot in-feed system, drums are spaced before picking and placement. When two drums are oriented and accumulated, the robot’s vacuum-style, end-of-arm tool picks and places four drums to form one layer. The full pallet moves out of the zone then an empty one enters. The transfer takes about 4 seconds.
A safety system, which includes light curtains, safety-painted steel wire mesh fencing and Class 3 safety switches at its door openings, prevents access to the robot and ancillary equipment while in operation.
The end result is a system that includes state-of-the-art equipment with the ability to handle a variety of pallet and drum configurations exceeding required throughput at 75% capacity.
About the Author

Follow Robotics 24/7 on Linkedin
About the Author

Follow Robotics 24/7 on Linkedin
Article topics
Email Sign Up
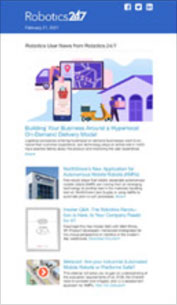
